Heat treatment of metals involves processes like annealing, hardening, and tempering, which require high temperatures and precise control. Safety precautions are critical to prevent accidents, injuries, and equipment damage. Key precautions include using proper personal protective equipment (PPE), ensuring proper ventilation, handling molten metals with care, and maintaining equipment regularly. Additionally, training workers on safety protocols and emergency procedures is essential to minimize risks. Below is a detailed breakdown of the safety measures and their importance.
Key Points Explained:
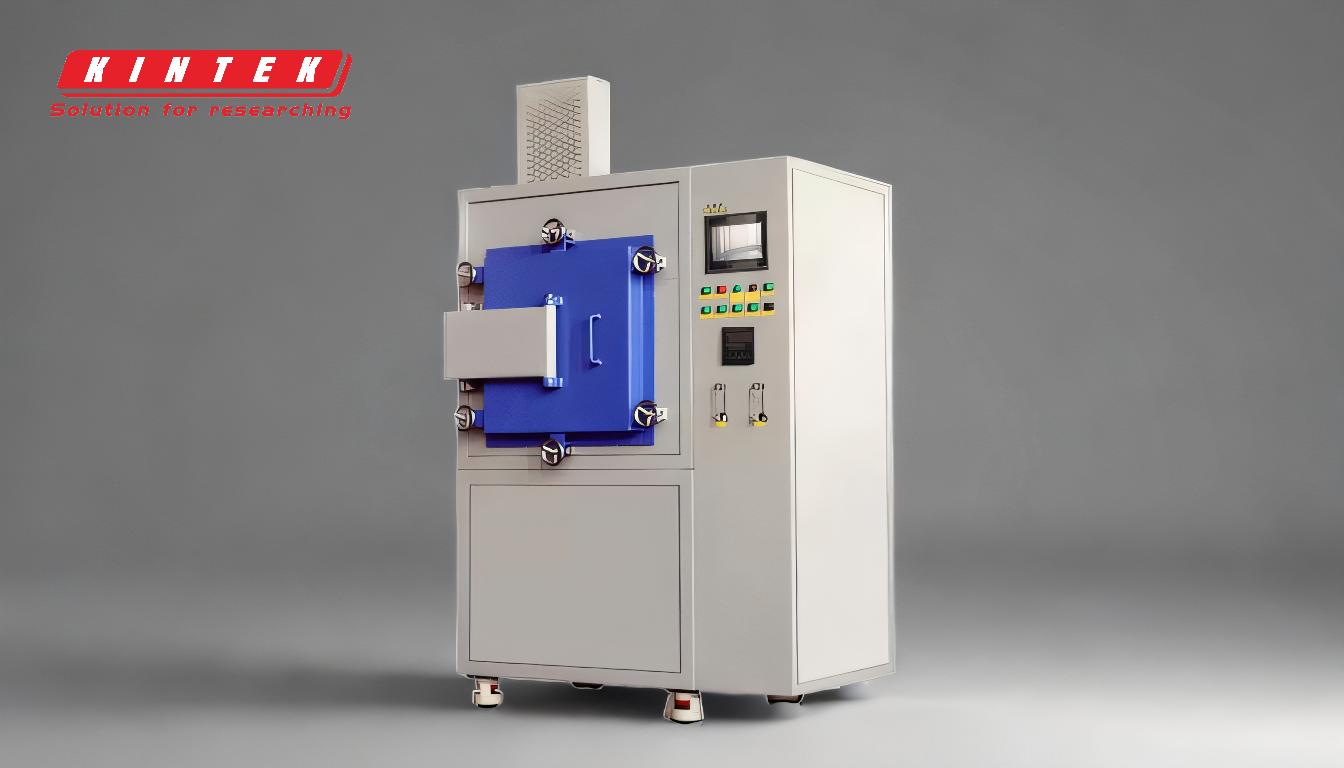
-
Personal Protective Equipment (PPE):
- Heat-Resistant Gloves: Essential for handling hot metals or tools to prevent burns.
- Safety Goggles or Face Shields: Protect eyes from sparks, molten metal splashes, and intense heat.
- Heat-Resistant Clothing: Prevents burns and injuries from hot surfaces or accidental contact with molten metal.
- Steel-Toed Boots: Protect feet from heavy objects and hot materials.
- Respirators or Masks: Necessary in environments with fumes or dust to prevent inhalation of harmful substances.
-
Proper Handling of Molten Metals:
- Use of Appropriate Tools: Tools like tongs, ladles, and crucibles designed for high temperatures must be used to transport and pour molten metals.
- Avoid Overfilling Containers: Overfilling can lead to spills, which are extremely hazardous.
- Secure Work Area: Ensure the workspace is free of clutter and spills to prevent tripping or accidental contact with hot materials.
-
Ventilation and Fume Control:
- Adequate Ventilation Systems: Heat treatment processes can release harmful fumes and gases. Proper ventilation ensures these are safely removed from the workspace.
- Local Exhaust Systems: Installed near heat treatment equipment to capture fumes at the source.
- Monitoring Air Quality: Regular checks to ensure the air is safe to breathe, especially in enclosed spaces.
-
Equipment Maintenance and Inspection:
- Regular Inspections: Check furnaces, ovens, and other equipment for wear, cracks, or malfunctions that could lead to accidents.
- Calibration of Temperature Controls: Ensures accurate temperature regulation, preventing overheating or underheating.
- Emergency Shut-Off Systems: Must be functional and easily accessible in case of equipment failure or other emergencies.
-
Training and Emergency Preparedness:
- Comprehensive Training: Workers should be trained on proper heat treatment procedures, safety protocols, and emergency response.
- Fire Safety Training: Heat treatment involves high temperatures, making fire safety knowledge crucial.
- First Aid and Burn Treatment: Workers should know how to treat burns and other injuries promptly.
- Emergency Drills: Regular drills to ensure workers know how to respond to fires, spills, or equipment failures.
-
Workplace Organization and Safety Signage:
- Clear Signage: Mark hazardous areas, emergency exits, and safety equipment locations.
- Designated Work Zones: Separate heat treatment areas from other activities to minimize risks to non-involved personnel.
- Spill Containment Measures: Use barriers or absorbent materials to contain spills and prevent them from spreading.
-
Chemical Safety:
- Proper Storage of Chemicals: Quenching fluids and other chemicals used in heat treatment should be stored safely, away from heat sources.
- Handling Quenching Fluids: Some fluids can release toxic fumes or cause skin irritation. Use appropriate PPE and follow manufacturer guidelines.
-
Fire Prevention and Control:
- Fire Extinguishers: Ensure fire extinguishers rated for metal fires are readily available.
- Flammable Material Control: Keep flammable materials away from heat treatment areas.
- Fire Blankets: Useful for smothering small fires or wrapping around a person in case of a clothing fire.
-
Environmental Considerations:
- Waste Disposal: Dispose of waste materials, such as used quenching fluids or metal scraps, in accordance with environmental regulations.
- Noise Control: Heat treatment processes can be noisy. Provide ear protection if necessary.
-
Monitoring and Documentation:
- Record Keeping: Maintain logs of equipment inspections, maintenance, and safety training.
- Incident Reporting: Document any accidents or near-misses to identify trends and improve safety measures.
By adhering to these safety precautions, the risks associated with heat treatment of metals can be significantly reduced, ensuring a safer and more productive work environment.
Summary Table:
Safety Precautions | Key Details |
---|---|
Personal Protective Equipment | Heat-resistant gloves, safety goggles, heat-resistant clothing, steel-toed boots, respirators. |
Handling Molten Metals | Use appropriate tools, avoid overfilling containers, secure work area. |
Ventilation & Fume Control | Adequate ventilation, local exhaust systems, air quality monitoring. |
Equipment Maintenance | Regular inspections, calibration of temperature controls, emergency shut-off systems. |
Training & Emergency Prep | Comprehensive training, fire safety, first aid, emergency drills. |
Workplace Organization | Clear signage, designated work zones, spill containment measures. |
Chemical Safety | Proper storage of chemicals, safe handling of quenching fluids. |
Fire Prevention | Fire extinguishers, flammable material control, fire blankets. |
Environmental Considerations | Waste disposal, noise control. |
Monitoring & Documentation | Record keeping, incident reporting. |
Ensure your heat treatment process is safe and efficient—contact our experts today for personalized advice!