The annealing process is a critical heat treatment method used to alter the physical and mechanical properties of metals, making them more ductile, reducing internal stresses, and improving their workability. The process involves three main steps: heating the metal to a specific temperature, holding it at that temperature for a set period, and then cooling it at a controlled rate. This process is typically carried out in specialized equipment like a chamber furnace or annealing furnace, which ensures precise temperature control and uniform heating. The annealing process is essential in industries where metal components need to be reshaped, machined, or subjected to further processing without cracking or breaking.
Key Points Explained:
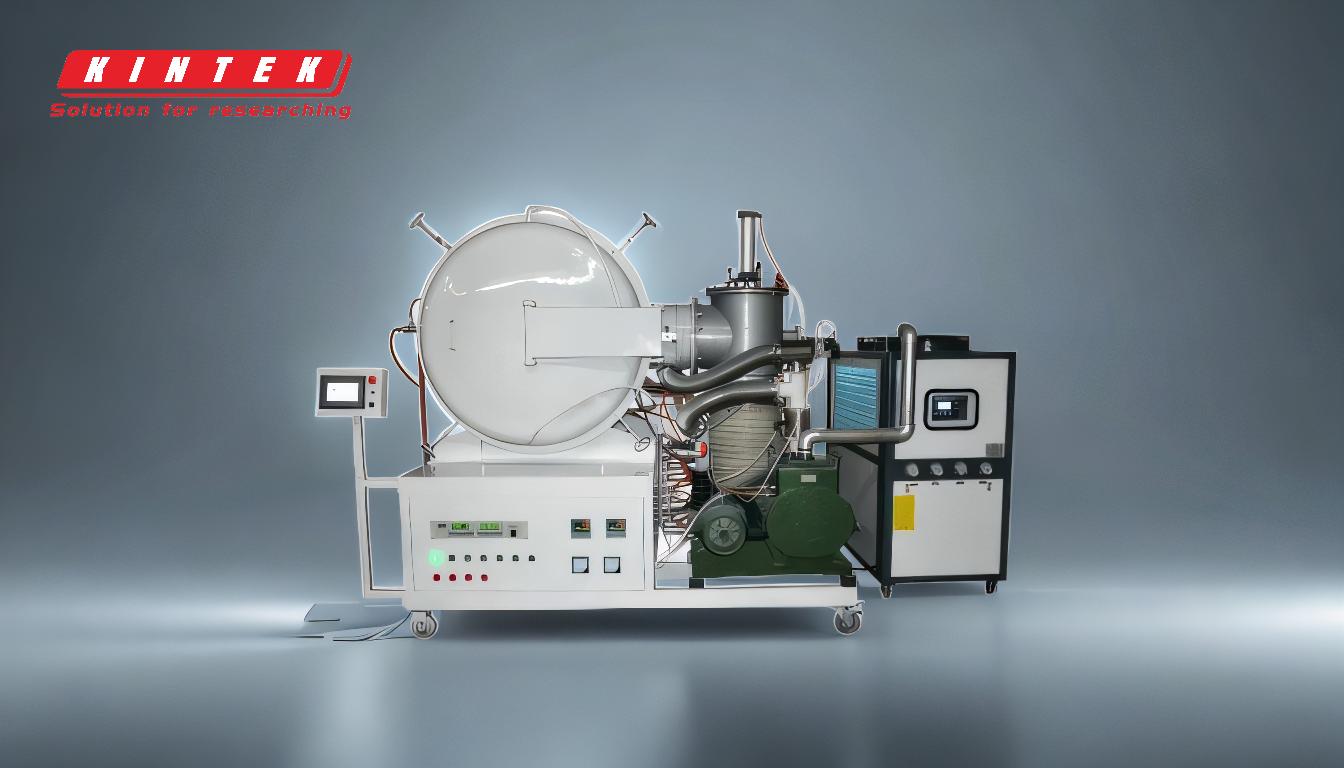
-
Heating the Metal to a Specified Temperature
- The first step in the annealing process is heating the metal to a temperature above its recrystallization point but below its melting point. This temperature varies depending on the type of metal and its composition.
- Heating the metal to this temperature allows its crystalline structure to become fluid, enabling the repair of defects and the redistribution of internal stresses.
- The use of a chamber furnace or annealing furnace ensures uniform heating, which is crucial for achieving consistent results across the entire workpiece.
-
Holding the Metal at the Specified Temperature (Holding Time)
- Once the metal reaches the desired temperature, it is held at that temperature for a predetermined period, known as the holding time.
- The holding time allows the metal's crystalline structure to fully recrystallize, ensuring that internal stresses are relieved and the material becomes more ductile.
- The duration of the holding time depends on factors such as the type of metal, its thickness, and the desired properties.
-
Controlled Cooling of the Metal
- After the holding period, the metal is cooled at a controlled rate. This slow cooling process is critical for achieving the desired mechanical properties, such as increased ductility and reduced hardness.
- Rapid cooling, as seen in processes like quenching, can lead to brittleness and internal stresses, which are counterproductive to the goals of annealing.
- The cooling rate is carefully managed to ensure that the metal's new crystalline structure is stable and free from defects.
-
Role of Equipment in the Annealing Process
- Specialized equipment like annealing furnaces and chamber furnaces play a vital role in the annealing process. These furnaces provide precise temperature control and uniform heating, which are essential for consistent results.
- The furnace ensures that the metal is heated evenly, preventing localized overheating or underheating, which could lead to uneven material properties.
- Modern annealing furnaces often come with programmable controls, allowing for precise adjustments to heating rates, holding times, and cooling rates based on the specific requirements of the metal being treated.
-
Applications and Benefits of Annealing
- Annealing is widely used in industries such as automotive, aerospace, and manufacturing, where metal components need to be reshaped, machined, or subjected to further processing.
- The process improves the metal's ductility, making it easier to work with and reducing the risk of cracking or breaking during subsequent operations.
- By relieving internal stresses and refining the crystalline structure, annealing also enhances the metal's overall performance and longevity.
In summary, the annealing process is a carefully controlled heat treatment method that involves heating, holding, and cooling metal to achieve desired mechanical properties. The use of specialized equipment like annealing furnaces ensures precision and consistency, making the process indispensable in various industrial applications.
Summary Table:
Step | Description |
---|---|
1. Heating | Heat the metal above its recrystallization point but below its melting point. |
2. Holding | Maintain the temperature for a set period to allow recrystallization. |
3. Cooling | Cool the metal at a controlled rate to achieve desired mechanical properties. |
Equipment | Use annealing or chamber furnaces for precise temperature control and uniformity. |
Discover how annealing can improve your metalworking processes—contact our experts today for tailored solutions!