Sintering ceramics involves a series of techniques and processes that transform powdered materials into dense, solid structures through the application of heat and sometimes pressure. The process typically includes preparation of the powder, shaping, and heating to fuse particles. Techniques vary based on the materials used, the desired properties of the final product, and the equipment available. Common methods include Conventional Sintering, Spark Plasma Sintering (SPS), Microwave Sintering, and Hot-Pressure Sintering. Each method has unique advantages and is chosen based on specific requirements such as temperature control, speed, and the need for pressure application.
Key Points Explained:
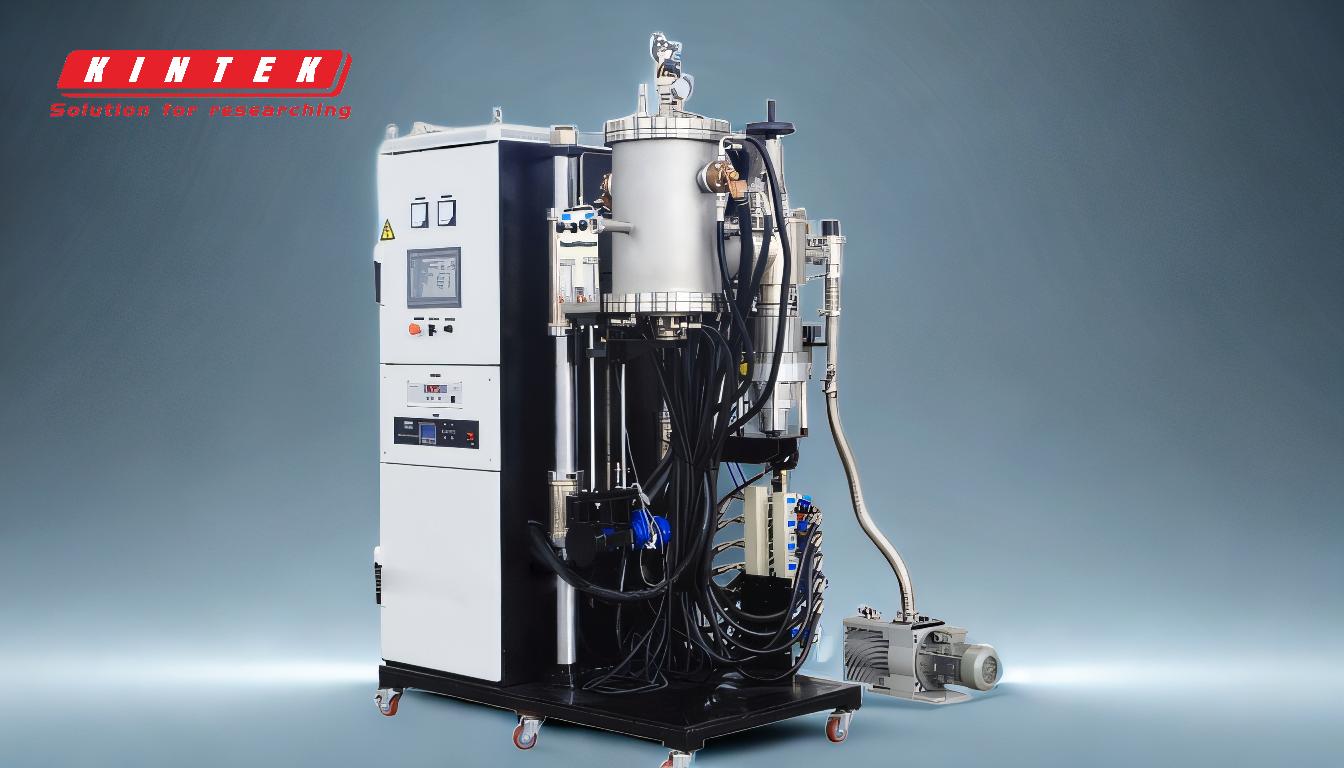
-
Preparation of Powder Compact:
- Mixing: The process begins with mixing ceramic powders with binders, deflocculants, and sometimes water to form a slurry. This mixture ensures uniform distribution of particles and aids in the shaping process.
- Spray Drying: The slurry is then spray-dried to form a free-flowing powder, which is easier to handle and press into molds.
- Pressing: The dried powder is pressed into a mold to form a 'green body'. This preform has the desired shape but lacks the strength and density of the final product.
-
Heating and Consolidation:
- Binder Burn-off: The green body is heated at a low temperature to remove the binder. This step is crucial to prevent defects in the final product.
- Sintering: The primary sintering process involves heating the ceramic to a temperature just below its melting point. This causes the particles to densify and merge, reducing porosity and increasing strength. The exact temperature and duration depend on the ceramic material and the desired properties.
-
Advanced Sintering Techniques:
- Conventional Sintering: This is the most common method, where the ceramic is heated in a furnace. It is suitable for a wide range of materials but can be time-consuming.
- Spark Plasma Sintering (SPS): This technique uses electrical currents to generate heat directly within the powder compact, allowing for rapid heating and cooling. It is particularly useful for materials that require high densities and fine microstructures.
- Microwave Sintering: This method uses microwave energy to heat the ceramic. It offers uniform heating and can significantly reduce sintering times compared to conventional methods.
- Hot-Pressure Sintering: In this method, pressure is applied during the heating process to enhance densification. It is ideal for materials that are difficult to sinter using conventional methods.
-
Factors Influencing Sintering:
- Material Properties: The type of ceramic, particle size, and purity significantly affect the sintering process. Materials with smaller particle sizes and higher purity generally sinter more easily.
- Temperature and Time: Precise control of temperature and sintering time is crucial to achieve the desired density and microstructure.
- Atmosphere: The sintering environment (e.g., air, vacuum, or inert gas) can influence the final properties of the ceramic. For example, sintering in a vacuum can prevent oxidation and improve densification.
-
Post-Sintering Processes:
- Cooling: After sintering, the ceramic must be cooled slowly to prevent cracking and to stabilize the microstructure.
- Finishing: Additional processes such as machining, polishing, or coating may be required to achieve the final dimensions and surface quality.
By understanding these key points, a purchaser can make informed decisions about the appropriate sintering techniques and materials for their specific needs, ensuring optimal performance and cost-efficiency.
Summary Table:
Sintering Technique | Key Features | Best For |
---|---|---|
Conventional Sintering | Time-consuming, suitable for a wide range of materials | General-purpose ceramics with no specific time constraints |
Spark Plasma Sintering (SPS) | Rapid heating/cooling, high-density materials, fine microstructures | Materials requiring high densities and precision |
Microwave Sintering | Uniform heating, reduced sintering times | Fast processing and uniform heat distribution |
Hot-Pressure Sintering | Pressure-assisted densification, ideal for hard-to-sinter materials | Materials requiring enhanced densification and strength |
Ready to optimize your ceramic sintering process? Contact our experts today for tailored solutions!