Heat treatment is a critical process in metallurgy and materials science, used to alter the physical and mechanical properties of metals and alloys. The three main heat treatments are annealing, quenching, and tempering. Each of these processes serves a distinct purpose, such as improving ductility, increasing hardness, or relieving internal stresses. Annealing involves heating and slow cooling to soften the material, quenching rapidly cools the metal to increase hardness, and tempering reduces brittleness by reheating and cooling the quenched material. These treatments are essential for achieving desired material properties in various industrial applications.
Key Points Explained:
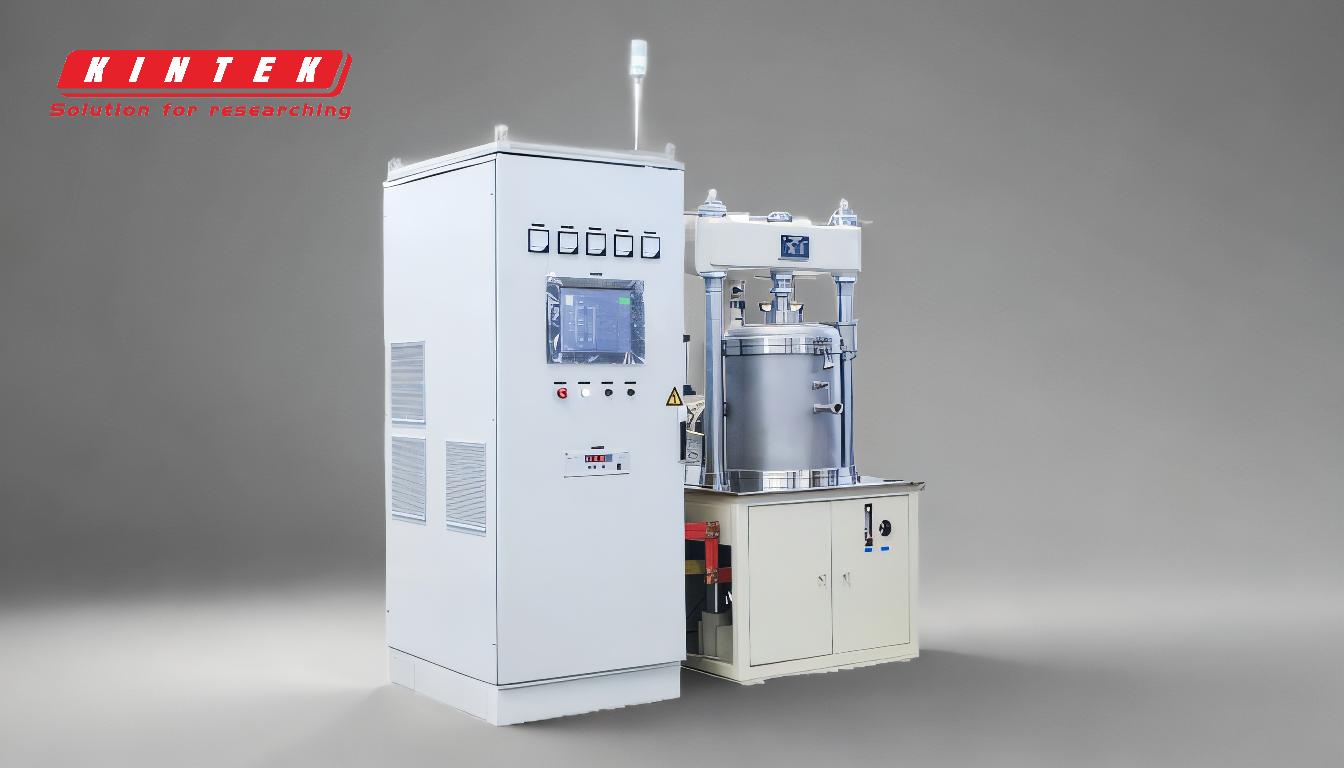
-
Annealing
- Purpose: Annealing is used to soften metals, improve ductility, and relieve internal stresses.
- Process: The material is heated to a specific temperature (above its recrystallization temperature) and then cooled slowly, often in a furnace.
- Results: This process refines the grain structure, making the material more workable and less brittle. It is commonly used for steels, copper, and aluminum.
- Applications: Annealing is ideal for materials that need to be machined, formed, or welded, as it reduces hardness and improves uniformity.
-
Quenching
- Purpose: Quenching is used to increase the hardness and strength of metals by rapidly cooling them.
- Process: The material is heated to a high temperature and then rapidly cooled, typically using water, oil, or air. This rapid cooling traps carbon atoms in the crystal structure, forming a harder phase called martensite.
- Results: Quenching makes the material harder but also more brittle. It is often followed by tempering to reduce brittleness.
- Applications: Quenching is widely used in the production of tools, gears, and components that require high surface hardness and wear resistance.
-
Tempering
- Purpose: Tempering is used to reduce the brittleness of quenched metals while maintaining their hardness and strength.
- Process: The quenched material is reheated to a temperature below its critical point and then cooled at a controlled rate. This process allows some of the martensite to transform into a more ductile structure.
- Results: Tempering improves toughness and ductility, making the material less prone to cracking or breaking under stress.
- Applications: Tempering is essential for components like springs, cutting tools, and structural parts that require a balance of hardness and toughness.
Additional Notes:
- While annealing, quenching, and tempering are the three main heat treatments, other processes like case hardening, normalizing, and precipitation strengthening are also important but serve more specialized purposes.
- The choice of heat treatment depends on the desired properties of the material and its intended application. For example, annealing is ideal for improving machinability, while quenching and tempering are better suited for enhancing strength and durability.
- Heat treatments are often used in combination to achieve the optimal balance of properties. For instance, quenching is typically followed by tempering to reduce brittleness and improve toughness.
By understanding these three main heat treatments, manufacturers and engineers can select the appropriate process to achieve the desired material properties for their specific applications.
Summary Table:
Heat Treatment | Purpose | Process | Results | Applications |
---|---|---|---|---|
Annealing | Soften metals, improve ductility | Heat above recrystallization temperature, then cool slowly | Refines grain structure, reduces hardness, improves workability | Ideal for machining, forming, or welding materials like steel, copper, aluminum |
Quenching | Increase hardness and strength | Heat to high temperature, then rapidly cool (water, oil, or air) | Forms martensite, increases hardness but also brittleness | Used for tools, gears, and wear-resistant components |
Tempering | Reduce brittleness, maintain hardness | Reheat quenched material below critical point, then cool at controlled rate | Improves toughness and ductility, reduces brittleness | Essential for springs, cutting tools, and structural parts |
Need help selecting the right heat treatment for your materials? Contact our experts today for tailored solutions!