The two basic classes of furnaces used in heat treatment are batch furnaces and continuous furnaces. Batch furnaces are designed for processing materials in discrete loads, where the entire load is treated at once, making them ideal for smaller-scale or specialized operations. Continuous furnaces, on the other hand, are designed for high-volume production, where materials move through the furnace continuously, ensuring consistent and efficient heat treatment. These classifications are based on the operational mode and are critical for selecting the right furnace type depending on production scale, material type, and specific heat treatment requirements.
Key Points Explained:
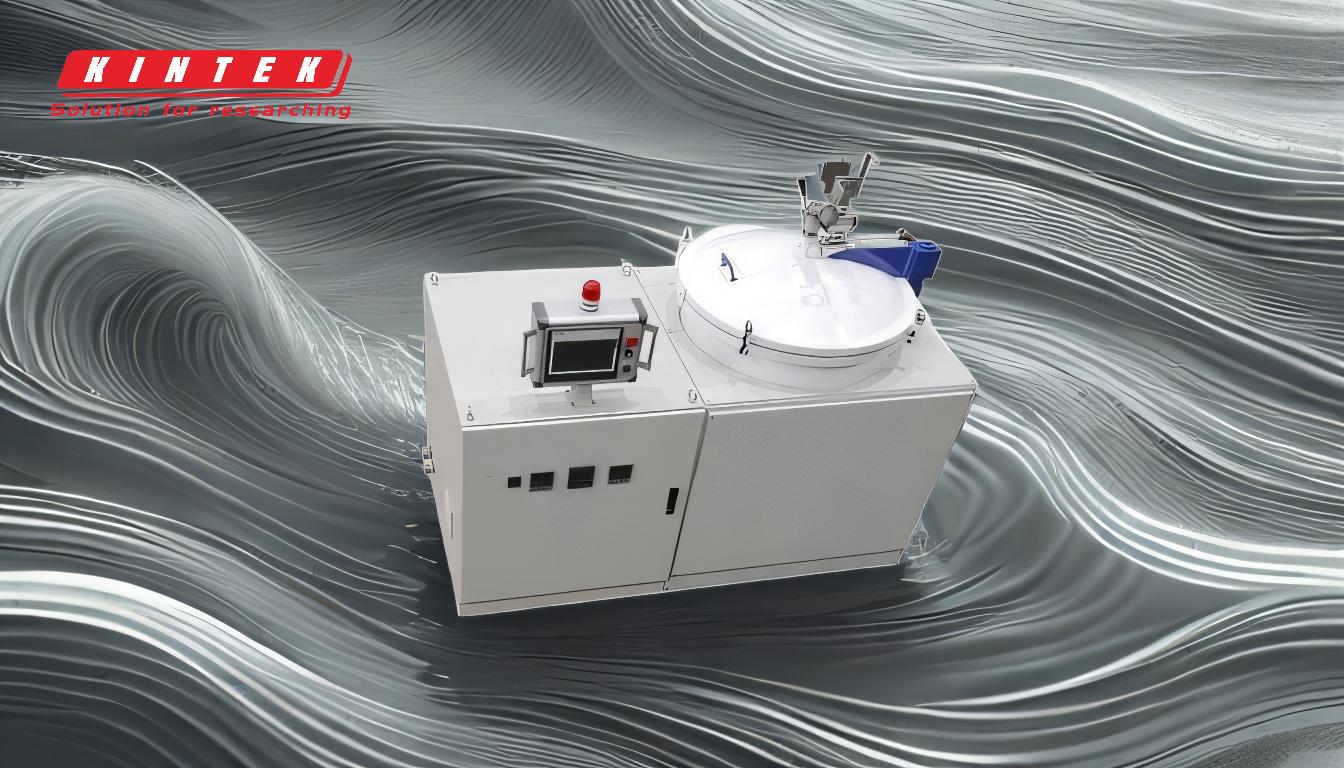
-
Batch Furnaces
- Batch furnaces process materials in discrete loads, meaning the entire load is treated at once.
- They are ideal for smaller-scale operations, custom heat treatments, or when flexibility in processing different materials is required.
- Examples include:
- Box-Type Batch Furnaces: Used for general-purpose heat treatment of steel, operating at temperatures up to 1050°C.
- Pit Furnaces (Vertical Furnaces): Suitable for long or heavy components, often used in aerospace applications.
- Bell Furnaces: Designed for annealing processes, particularly for coiled steel.
- Salt Bath Furnaces: Used for precise temperature control in specialized treatments like tempering or carburizing.
- Advantages: Flexibility, ability to handle varied loads, and suitability for low-to-medium production volumes.
-
Continuous Furnaces
- Continuous furnaces are designed for high-volume production, where materials move through the furnace in a continuous flow.
- They are ideal for large-scale operations requiring consistent and efficient heat treatment.
- Examples include:
- Roller Hearth Furnaces: Used for annealing or hardening processes, where materials are transported on rollers.
- Pusher Furnaces: Employed for high-temperature treatments like hardening or normalizing, with materials pushed through the furnace.
- Conveyor Belt Furnaces: Suitable for smaller components, providing uniform heating as materials move on a conveyor belt.
- Advantages: High throughput, consistent quality, and energy efficiency for large-scale production.
-
Key Differences Between Batch and Continuous Furnaces
- Operational Mode: Batch furnaces process materials in discrete loads, while continuous furnaces process materials in a continuous flow.
- Production Scale: Batch furnaces are better suited for low-to-medium production volumes, whereas continuous furnaces excel in high-volume production.
- Flexibility: Batch furnaces offer greater flexibility for custom or varied heat treatments, while continuous furnaces are optimized for consistent, repeatable processes.
- Energy Efficiency: Continuous furnaces are generally more energy-efficient for large-scale operations due to their continuous operation and reduced heat loss.
-
Applications and Selection Criteria
- Batch Furnaces: Preferred for specialized treatments, small-scale production, or when handling diverse materials. Common in aerospace, tooling, and custom manufacturing.
- Continuous Furnaces: Ideal for industries requiring high-volume production, such as automotive, steel manufacturing, and electronics.
By understanding these two basic classes of furnaces, purchasers can make informed decisions based on production requirements, material types, and specific heat treatment processes.
Summary Table:
Feature | Batch Furnaces | Continuous Furnaces |
---|---|---|
Operational Mode | Discrete loads, entire load treated at once | Continuous flow of materials through the furnace |
Production Scale | Low-to-medium production volumes | High-volume production |
Flexibility | High flexibility for custom or varied heat treatments | Optimized for consistent, repeatable processes |
Energy Efficiency | Less energy-efficient for large-scale operations | More energy-efficient due to continuous operation and reduced heat loss |
Applications | Aerospace, tooling, custom manufacturing | Automotive, steel manufacturing, electronics |
Need help choosing the right furnace for your heat treatment process? Contact our experts today for personalized advice!