Heat treatment processes are essential in altering the structural and physical properties of metals to make them suitable for various manufacturing applications. Two of the most fundamental heat treatment processes are Annealing and Quenching. Annealing involves heating the metal to a specific temperature and then cooling it slowly to soften the material, relieve internal stresses, and improve ductility. Quenching, on the other hand, involves rapidly cooling the metal after heating to increase its hardness and strength, though it may also make the material more brittle. These processes are widely used in industries to achieve desired material properties for specific applications.
Key Points Explained:
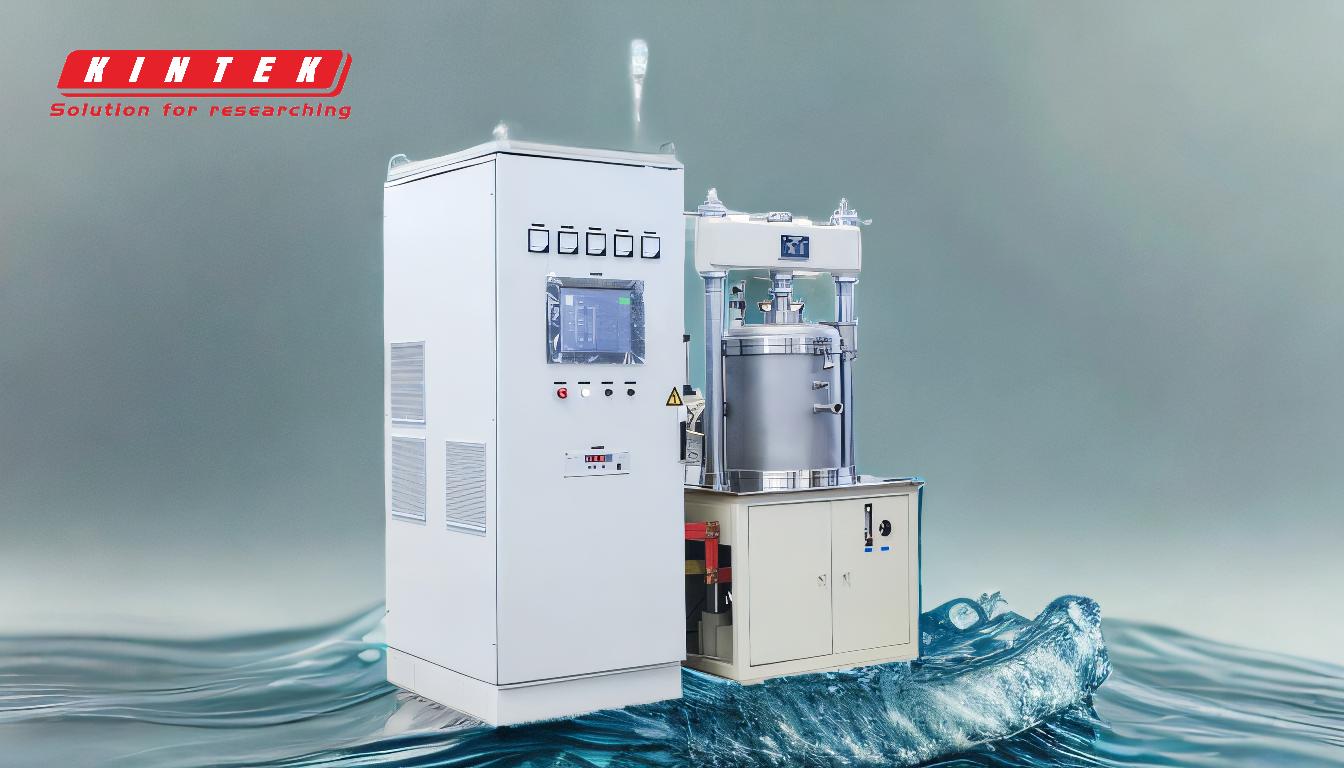
1. Annealing
- Definition: Annealing is a heat treatment process that involves heating a metal to a specific temperature (above its recrystallization temperature) and then cooling it slowly to alter its microstructure and properties.
-
Purpose:
- Softens the metal, making it more workable.
- Relieves internal stresses caused by previous manufacturing processes (e.g., machining, welding).
- Improves ductility and toughness, making the material less brittle.
- Enhances machinability and prepares the metal for further processing.
-
Process Steps:
- Heating the metal to a temperature above its recrystallization point.
- Holding the metal at this temperature for a specific duration to allow uniform heating.
- Slowly cooling the metal in a controlled environment (e.g., furnace cooling or air cooling).
-
Applications:
- Used in steel manufacturing to improve ductility for cold working.
- Applied to copper and aluminum to enhance electrical conductivity.
- Common in the production of tools, wires, and sheets.
2. Quenching
- Definition: Quenching is a heat treatment process where a metal is heated to a high temperature and then rapidly cooled (often in water, oil, or air) to increase its hardness and strength.
-
Purpose:
- Increases the hardness and strength of the metal.
- Creates a martensitic structure in steel, which is very hard but brittle.
- Improves wear resistance and durability.
-
Process Steps:
- Heating the metal to a temperature above its critical point (austenitizing temperature).
- Holding the metal at this temperature to ensure uniform heating.
- Rapidly cooling the metal using a quenching medium (e.g., water, oil, or air).
-
Applications:
- Used in the production of tools, gears, and automotive components.
- Essential for hardening steel parts like knives, blades, and springs.
- Often followed by tempering to reduce brittleness.
Comparison of Annealing and Quenching:
Aspect | Annealing | Quenching |
---|---|---|
Cooling Rate | Slow cooling (furnace or air cooling). | Rapid cooling (water, oil, or air). |
Primary Effect | Softens the metal and improves ductility. | Hardens the metal and increases strength. |
Brittleness | Reduces brittleness. | Increases brittleness (if not tempered). |
Applications | Used for workability and stress relief. | Used for hardness and wear resistance. |
Additional Considerations:
- Tempering: Often performed after quenching to reduce brittleness and improve toughness. It involves reheating the quenched metal to a lower temperature and then cooling it.
- Case Hardening: A process that hardens the surface of the metal while keeping the core soft, often used for gears and bearings.
- Normalizing: Similar to annealing but involves cooling in air, resulting in a finer grain structure and improved mechanical properties.
By understanding these two fundamental heat treatment processes—annealing and quenching—manufacturers can tailor the properties of metals to meet specific application requirements, ensuring optimal performance and longevity of the final product.
Summary Table:
Aspect | Annealing | Quenching |
---|---|---|
Cooling Rate | Slow cooling (furnace or air cooling). | Rapid cooling (water, oil, or air). |
Primary Effect | Softens the metal and improves ductility. | Hardens the metal and increases strength. |
Brittleness | Reduces brittleness. | Increases brittleness (if not tempered). |
Applications | Used for workability and stress relief. | Used for hardness and wear resistance. |
Need help choosing the right heat treatment process for your application? Contact our experts today!