Heat treatment is a critical process in materials engineering, particularly in aerospace and manufacturing industries, to enhance the mechanical properties of metals and plastics. The two most important stages of heat treatment are heating and cooling, as they directly influence the material's microstructure and final properties. Heating ensures the material reaches a specific temperature to facilitate structural changes, while cooling determines the rate at which these changes solidify, affecting hardness, strength, and durability. Soaking, although important, is a supporting stage that ensures uniform temperature distribution. Below, the key points of these stages are explained in detail.
Key Points Explained:
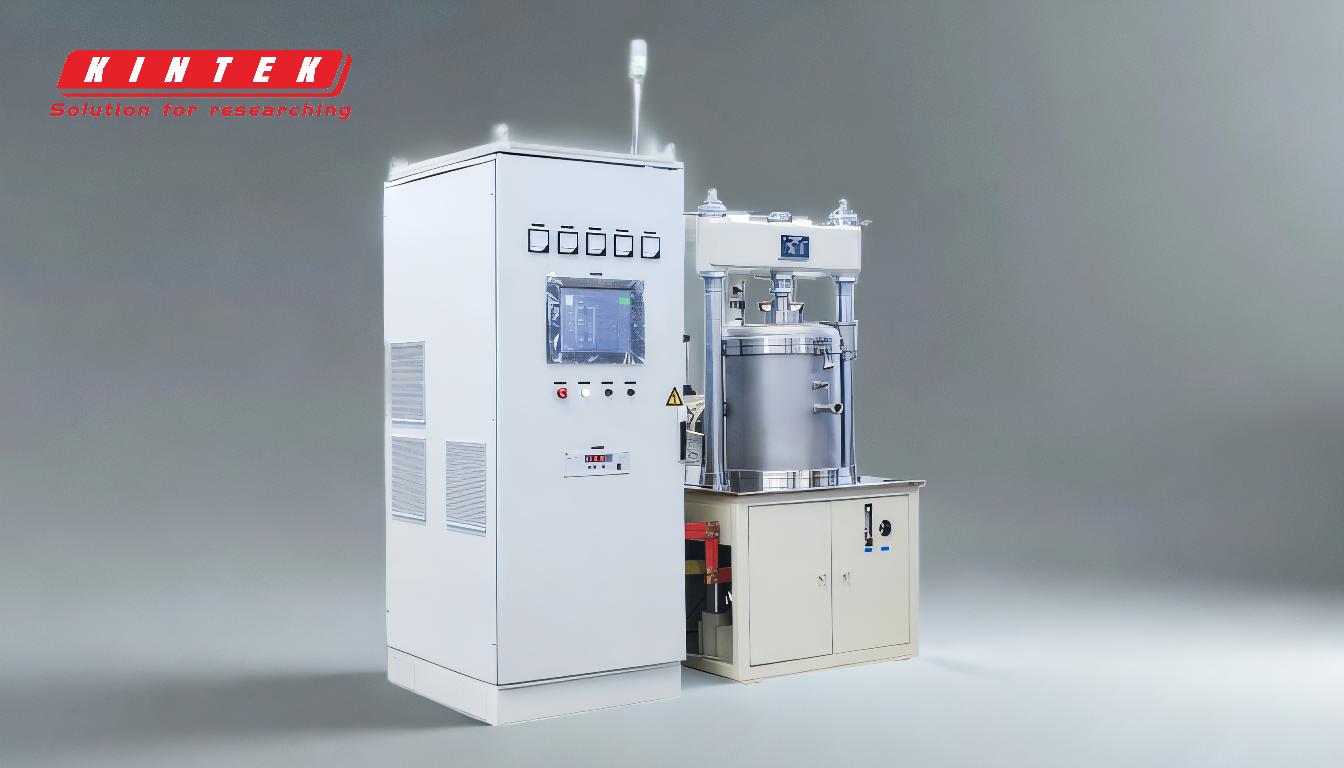
-
Heating Stage
- Purpose: The primary goal of heating is to raise the material's temperature to a specific level, enabling phase transformations in its microstructure.
- Temperature Range: Depending on the material and desired outcome, temperatures can range from a few hundred degrees to as high as 2,400°F.
- Importance: Heating ensures the material reaches a state where its internal structure can be altered. For example, in annealing, heating softens the metal, while in hardening, it prepares the material for rapid cooling to achieve increased hardness.
- Preventing Deformation: Controlled heating is crucial to avoid thermal stress and deformation, especially in aerospace components where precision is critical.
-
Cooling Stage
- Purpose: Cooling determines the final microstructure and mechanical properties of the material. The rate of cooling (e.g., rapid, slow, or controlled) directly impacts hardness, strength, and ductility.
- Methods: Cooling can be achieved through air cooling, oil quenching, water quenching, or furnace cooling, depending on the material and desired outcome.
- Importance: For instance, rapid cooling (quenching) is used to harden metals, while slow cooling (annealing) softens them. In aerospace applications, controlled cooling ensures components meet stringent performance and safety standards.
- Impact on Properties: The cooling rate affects grain structure, residual stress, and toughness, making it a critical stage in achieving the desired material characteristics.
-
Soaking Stage (Supporting Role)
- Purpose: Soaking ensures the material's temperature is uniform throughout, allowing the internal structure to fully transform.
- Duration: The soaking time can range from a few seconds to several hours, depending on the material and process.
- Importance: While not the primary focus, soaking is essential for achieving consistent results, especially in complex aerospace components where uniformity is critical.
-
Applications in Aerospace and Manufacturing
- Aerospace: Heat treatment is vital for producing lightweight, high-strength components that can withstand extreme conditions. The heating and cooling stages are carefully controlled to ensure optimal performance and safety.
- Manufacturing: Heat treatment processes like annealing, hardening, and stress relief are used to tailor materials for specific applications, from soft, machinable metals to hard, wear-resistant surfaces.
-
Considerations for Equipment and Consumables Purchasers
- Equipment: Purchasers should consider furnaces capable of precise temperature control and cooling systems that offer flexibility in cooling rates.
- Consumables: Quenching oils, gases, and other cooling mediums must be selected based on the material and desired properties.
- Quality Assurance: Ensuring consistent and repeatable results requires high-quality equipment and consumables, as well as adherence to standardized heat treatment protocols.
By understanding the critical roles of heating and cooling in heat treatment, purchasers can make informed decisions about equipment and consumables, ensuring optimal outcomes for their specific applications.
Summary Table:
Stage | Purpose | Key Factors |
---|---|---|
Heating | Raise material temperature for phase transformations | Temperature range (up to 2,400°F), controlled heating to prevent deformation |
Cooling | Determine final microstructure and properties | Cooling methods (air, oil, water, furnace), rate impacts hardness and strength |
Soaking | Ensure uniform temperature distribution | Duration varies (seconds to hours), essential for consistent results |
Optimize your heat treatment process with the right equipment—contact our experts today!