Annealing is a heat treatment process used to alter the physical and sometimes chemical properties of a material, typically to increase its ductility and reduce its hardness, making it more workable. The process involves heating the material to a specific temperature, holding it at that temperature for a certain period, and then cooling it at a controlled rate. The two primary processes of annealing are hydrogen annealing and conventional annealing, each with distinct characteristics and applications.
Key Points Explained:
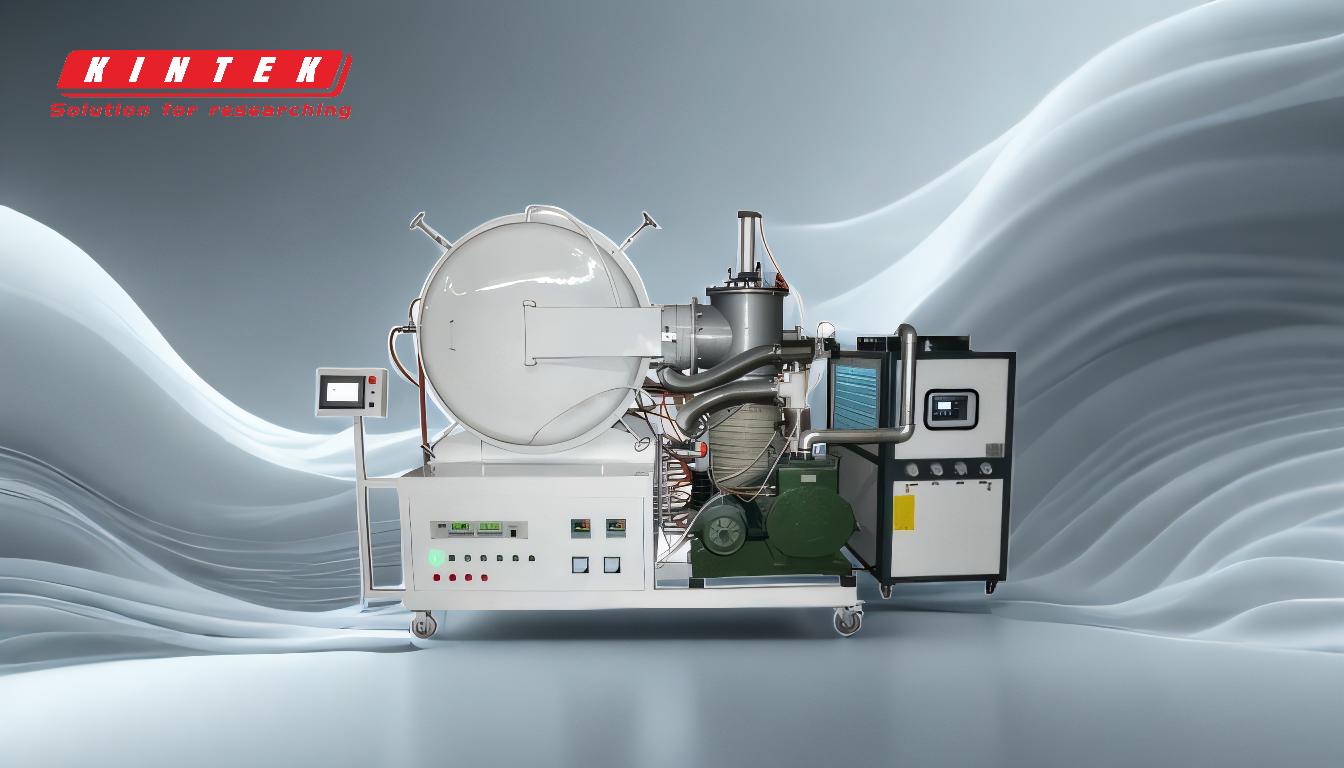
-
Hydrogen Annealing:
- Process Overview: Hydrogen annealing involves heating the material in a controlled atmosphere of 100% hydrogen. This environment prevents oxidation and discoloration of the product.
- Surface Cleaning: Hydrogen acts as a reducing gas, which helps in cleaning the surface of oxidized parts by reducing the oxides present on the material.
- Bright Annealing: This process is often referred to as 'bright annealing' because it results in a clean, bright surface finish.
- Decarburization Risk: One of the drawbacks of hydrogen annealing is the potential for decarburization of steel parts, which can weaken the material. Precautions must be taken to mitigate this risk.
- Cost Considerations: Hydrogen is the most expensive atmosphere for annealing. However, lower-cost alternatives like nitrogen-hydrogen blends can be used effectively to reduce costs while still providing some of the benefits of hydrogen annealing.
-
Conventional Annealing:
- Process Overview: Conventional annealing typically involves heating the material in a furnace without the use of a specialized atmosphere like hydrogen. The process follows the three main stages of annealing: recovery, recrystallization, and grain growth.
- Recovery Stage: In this initial stage, the material is heated to relieve internal stresses. This stage does not involve any significant change in the microstructure but helps in reducing the internal energy of the material.
- Recrystallization Stage: The material is heated above its recrystallization temperature but below its melting point. This stage allows new, strain-free grains to form, replacing the deformed grains.
- Grain Growth Stage: As the material cools, new grains continue to grow, leading to a more uniform and pliable microstructure. This stage is crucial for achieving the desired mechanical properties, such as increased ductility and reduced hardness.
-
Comparison of Hydrogen and Conventional Annealing:
- Atmosphere: Hydrogen annealing requires a controlled hydrogen atmosphere, whereas conventional annealing can be performed in a standard furnace atmosphere.
- Surface Finish: Hydrogen annealing provides a superior surface finish due to the reducing nature of hydrogen, which is not typically achieved with conventional annealing.
- Cost: Hydrogen annealing is more expensive due to the cost of hydrogen gas and the need for specialized equipment. Conventional annealing is generally more cost-effective.
- Material Suitability: Hydrogen annealing is particularly useful for materials that are prone to oxidation or require a high-quality surface finish. Conventional annealing is suitable for a broader range of materials and applications.
-
Applications of Annealing:
- Hydrogen Annealing: This process is often used in industries where a high-quality surface finish is critical, such as in the production of stainless steel components, wire, and other precision parts.
- Conventional Annealing: This process is widely used in the manufacturing of various metal products, including steel, aluminum, and copper, where the primary goal is to improve ductility and reduce hardness.
In summary, the two primary processes of annealing—hydrogen annealing and conventional annealing—serve different purposes and are chosen based on the specific requirements of the material and the desired outcome. Hydrogen annealing offers superior surface quality but at a higher cost, while conventional annealing is more versatile and cost-effective for a wide range of applications.
Summary Table:
Aspect | Hydrogen Annealing | Conventional Annealing |
---|---|---|
Atmosphere | Controlled hydrogen atmosphere (100% H₂ or N₂-H₂ blends) | Standard furnace atmosphere |
Surface Finish | Superior, clean, and bright finish (bright annealing) | Standard finish, no special surface treatment |
Cost | Higher due to hydrogen gas and specialized equipment | More cost-effective |
Material Suitability | Ideal for oxidation-prone materials or those requiring high-quality surface finishes | Suitable for a wide range of materials and applications |
Applications | Stainless steel components, wire, precision parts | Steel, aluminum, copper, and other metal products |
Need help choosing the right annealing process for your materials? Contact our experts today for personalized advice!