In cement production, a rotary kiln is divided into distinct zones based on material flow and thermal processes. These zones include the kiln inlet cone, preheating zone, calcining zone, upper transition zone, clinkering zone, lower transition zone, and discharge area. Each zone serves a specific purpose in the transformation of raw materials into clinker, which is the intermediate product in cement manufacturing. The zones are designed to optimize heat transfer, fuel combustion, and material movement, ensuring efficient chemical and physical reactions. Understanding these zones is critical for equipment and consumable purchasers to ensure proper kiln operation and maintenance.
Key Points Explained:
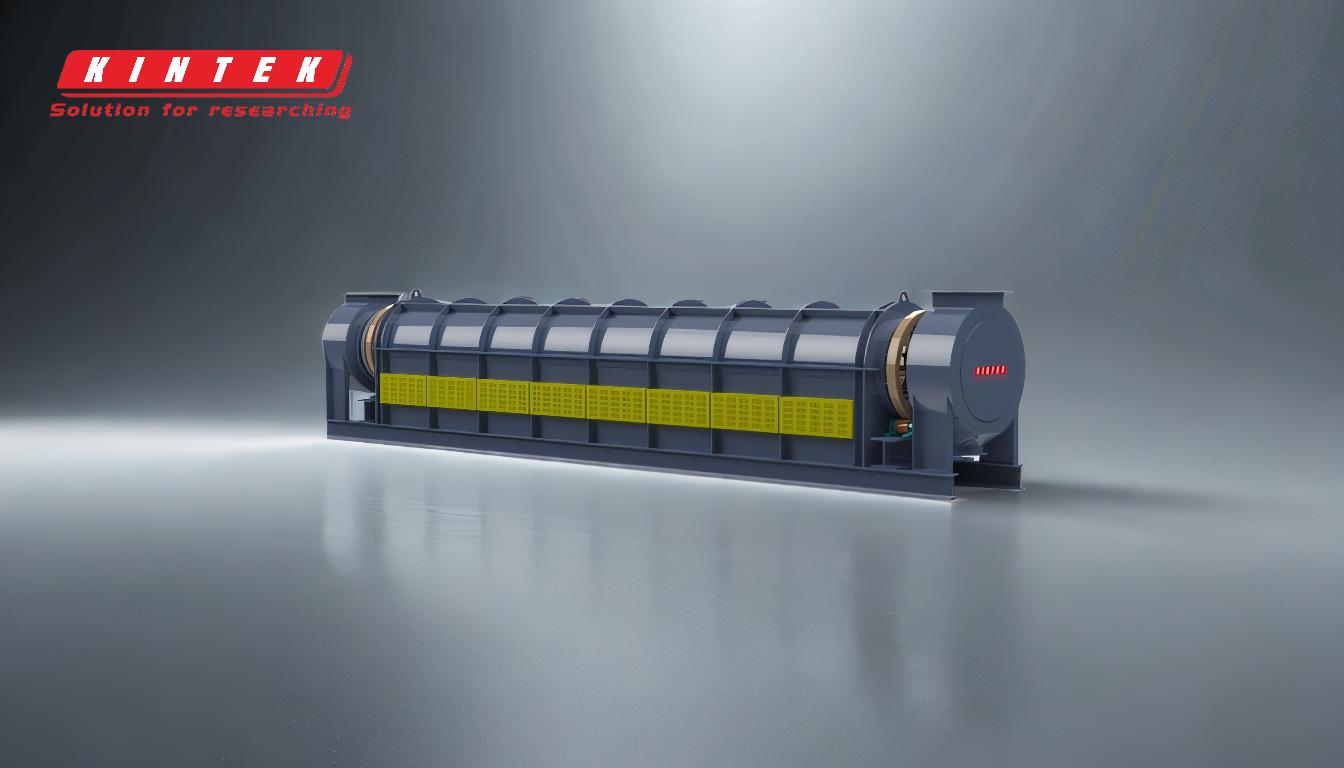
-
Kiln Inlet Cone:
- This is the entry point of raw materials into the rotary kiln.
- It is designed to facilitate the smooth flow of materials into the preheating zone.
- The cone shape helps in reducing turbulence and ensuring uniform distribution of materials.
-
Preheating Zone:
- Located just after the kiln inlet cone, this zone is where raw materials are heated to remove moisture and begin the initial stages of chemical decomposition.
- Temperatures in this zone typically range from 800°F to 1,200°F.
- The preheating zone is crucial for reducing energy consumption in subsequent zones by pre-drying and pre-heating the materials.
-
Calcining Zone:
- In this zone, the raw materials undergo calcination, a process where calcium carbonate (CaCO₃) decomposes into calcium oxide (CaO) and carbon dioxide (CO₂).
- Temperatures here range from 1,500°F to 1,800°F.
- This zone is critical for the formation of lime, which is essential for clinker production.
-
Upper Transition Zone:
- This zone acts as a bridge between the calcining zone and the clinkering zone.
- It ensures a smooth transition in temperature and chemical reactions, preventing thermal shock to the materials.
- The upper transition zone helps in stabilizing the material flow before it enters the high-temperature clinkering zone.
-
Clinkering Zone:
- The clinkering zone is the hottest part of the rotary kiln, with temperatures ranging from 2,200°F to 2,700°F.
- In this zone, the materials undergo sintering, forming clinker nodules through a series of complex chemical reactions.
- The clinkering zone is critical for the final quality of the clinker, as it determines the strength and composition of the cement.
-
Lower Transition Zone:
- This zone facilitates the cooling of clinker before it exits the kiln.
- It helps in reducing the temperature of the clinker to a level suitable for handling and further processing.
- The lower transition zone also ensures that the clinker does not cool too rapidly, which could lead to thermal stress and cracking.
-
Discharge Area:
- The final zone in the rotary kiln, where the clinker is discharged from the kiln for cooling and storage.
- This area is designed to handle high-temperature materials and ensure a smooth exit of clinker.
- Proper design of the discharge area is essential to prevent blockages and ensure continuous operation of the kiln.
Additional Considerations for Equipment and Consumable Purchasers:
- Refractory Lining: The refractory lining in each zone must be selected based on the temperature and chemical environment. High-quality refractory materials are essential for durability and efficiency.
- Heat Exchangers: Internal heat exchangers play a crucial role in optimizing heat transfer and fuel efficiency. Purchasers should ensure that these components are designed for the specific thermal requirements of each zone.
- Temperature Control: Each zone has specific temperature requirements. Advanced control systems are necessary to maintain optimal temperatures and ensure consistent clinker quality.
- Maintenance: Regular maintenance of the kiln, especially in high-temperature zones like the clinkering zone, is critical to prevent downtime and ensure long-term operation.
By understanding the zones of a rotary kiln and their respective functions, equipment and consumable purchasers can make informed decisions to optimize kiln performance and ensure the production of high-quality cement.
Summary Table:
Zone | Function | Temperature Range |
---|---|---|
Kiln Inlet Cone | Facilitates smooth material flow into the preheating zone | N/A |
Preheating Zone | Removes moisture and begins chemical decomposition | 800°F - 1,200°F |
Calcining Zone | Decomposes calcium carbonate into calcium oxide and carbon dioxide | 1,500°F - 1,800°F |
Upper Transition Zone | Ensures smooth transition between calcining and clinkering zones | N/A |
Clinkering Zone | Forms clinker nodules through sintering at high temperatures | 2,200°F - 2,700°F |
Lower Transition Zone | Cools clinker for handling and prevents thermal stress | N/A |
Discharge Area | Discharges clinker for cooling and storage | N/A |
Need expert advice on optimizing your rotary kiln? Contact us today to ensure peak performance and high-quality clinker production!