Furnace cleaning is a detailed process that involves cleaning the internal components of a furnace to ensure its efficient and safe operation. This includes cleaning the heat exchanger, blower motor, combustion chamber, burners, fan, and other parts. The process typically involves using high-pressure air and an industrial vacuum to remove dust and debris. Additionally, non-toxic cleaners and damp cloths are used for manual cleaning, and all electrical components must be handled carefully. Professional maintenance is often recommended to ensure safety and effectiveness. Below is a detailed breakdown of the key steps and considerations involved in furnace cleaning.
Key Points Explained:
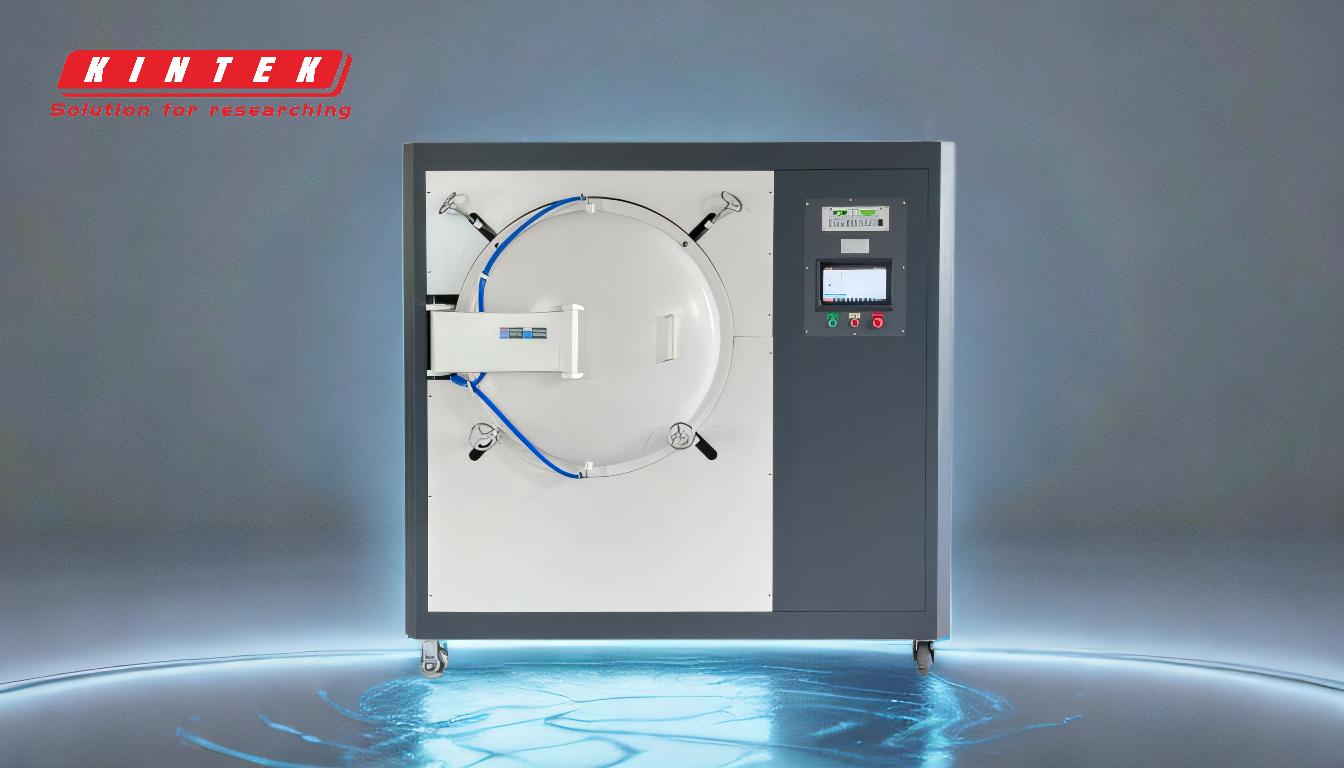
-
Safety First: Power Disconnection
- Why it’s important: Before starting any cleaning process, it is crucial to disconnect the furnace from its power source to prevent electrical hazards.
-
Steps:
- Unplug the power cord.
- Ensure any backup power systems are also disconnected.
- This step ensures that there is no risk of electric shock while cleaning the furnace.
-
Accessing the Furnace Interior
- Why it’s important: To clean the internal components, you need to access them by removing the front panel and other access points.
-
Steps:
- Remove the access door and door switch.
- Carefully remove the control board if necessary.
- Slide out the fan unit to access the blower assembly.
- This step allows you to reach the components that need cleaning.
-
Cleaning the Blower Assembly
- Why it’s important: The blower assembly is a critical component that can accumulate dust and debris, affecting the furnace's efficiency.
-
Steps:
- Use a vacuum to remove loose dust and debris.
- Clean the blower assembly with non-toxic soap and water.
- Use a toothbrush to reach into crevices and clean the fan blades thoroughly.
- Pay special attention to the spaces between the fan blades.
- Vacuum or wipe down belts, pulleys, and the motor until they are clean.
- This step ensures that the blower operates efficiently and reduces wear and tear.
-
Cleaning the Interior of the Furnace
- Why it’s important: The interior of the furnace can accumulate dust and debris, which can affect its performance and air quality.
-
Steps:
- Use a non-toxic cleaner and tap water with a damp cloth or towel to clean the entire interior.
- Vacuum the interior thoroughly to remove any remaining dust.
- This step ensures that the furnace operates efficiently and maintains good air quality.
-
Reassembling the Furnace
- Why it’s important: After cleaning, it is essential to reassemble the furnace correctly to ensure it operates safely and efficiently.
-
Steps:
- Replace the fan unit and secure all wires and screws.
- Reconnect the power cord.
- Replace the front panel and ensure all screws are tightened.
- This step ensures that the furnace is reassembled correctly and is ready for use.
-
Professional Maintenance
- Why it’s important: While some cleaning tasks can be done by homeowners, professional maintenance is recommended for safety and effectiveness.
-
Considerations:
- Professionals have the tools and expertise to clean and inspect the furnace thoroughly.
- They can identify and address any potential issues that may not be visible to the untrained eye.
- Regular professional maintenance can extend the lifespan of the furnace and prevent costly repairs.
-
Tools and Materials Needed
- Why it’s important: Having the right tools and materials ensures that the cleaning process is effective and safe.
-
List of Tools and Materials:
- High-pressure air compressor.
- Industrial vacuum.
- Non-toxic cleaner.
- Damp cloth or towel.
- Toothbrush for detailed cleaning.
- Screwdrivers for disassembly and reassembly.
- This step ensures that you have everything you need to clean the furnace effectively.
-
Final Checks
- Why it’s important: After cleaning and reassembling the furnace, it is essential to perform final checks to ensure everything is in working order.
-
Steps:
- Double-check all connections and screws.
- Ensure the front panel is securely in place.
- Test the furnace to ensure it is operating correctly.
- This step ensures that the furnace is safe to use and operating efficiently.
By following these steps, you can ensure that your furnace is clean, efficient, and safe to operate. Regular cleaning and maintenance can extend the lifespan of your furnace and improve its performance, ultimately saving you money on energy bills and costly repairs.
Summary Table:
Step | Key Actions | Why It’s Important |
---|---|---|
1. Power Disconnection | Unplug the furnace and disconnect backup power. | Prevents electrical hazards during cleaning. |
2. Access Interior | Remove front panel, door switch, and fan unit. | Allows access to internal components for thorough cleaning. |
3. Clean Blower | Use a vacuum, non-toxic soap, and a toothbrush for detailed cleaning. | Removes dust and debris, ensuring efficient blower operation. |
4. Clean Interior | Wipe with non-toxic cleaner and vacuum thoroughly. | Improves air quality and furnace efficiency. |
5. Reassemble Furnace | Secure all wires, screws, and panels. | Ensures safe and efficient operation post-cleaning. |
6. Professional Help | Schedule regular maintenance with a professional. | Identifies hidden issues and extends furnace lifespan. |
7. Tools Needed | High-pressure air, industrial vacuum, non-toxic cleaner, screwdrivers, etc. | Ensures effective and safe cleaning. |
8. Final Checks | Test the furnace and ensure all connections are secure. | Confirms the furnace is operating safely and efficiently. |
Ensure your furnace runs efficiently and safely—contact our experts today for professional maintenance and cleaning services!