Quenching is a critical step in heat treatment processes, primarily used to rapidly cool a metal to achieve specific mechanical properties. This process transforms the microstructure of the metal, typically from austenite to martensite, which is harder and more brittle. Quenching is often followed by tempering to balance hardness and toughness, ensuring the material is both strong and durable. The cooling medium used in quenching, such as oil, water, or air, plays a significant role in determining the final properties of the metal. Understanding the quenching process is essential for achieving desired hardness, strength, and toughness in heat-treated metals.
Key Points Explained:
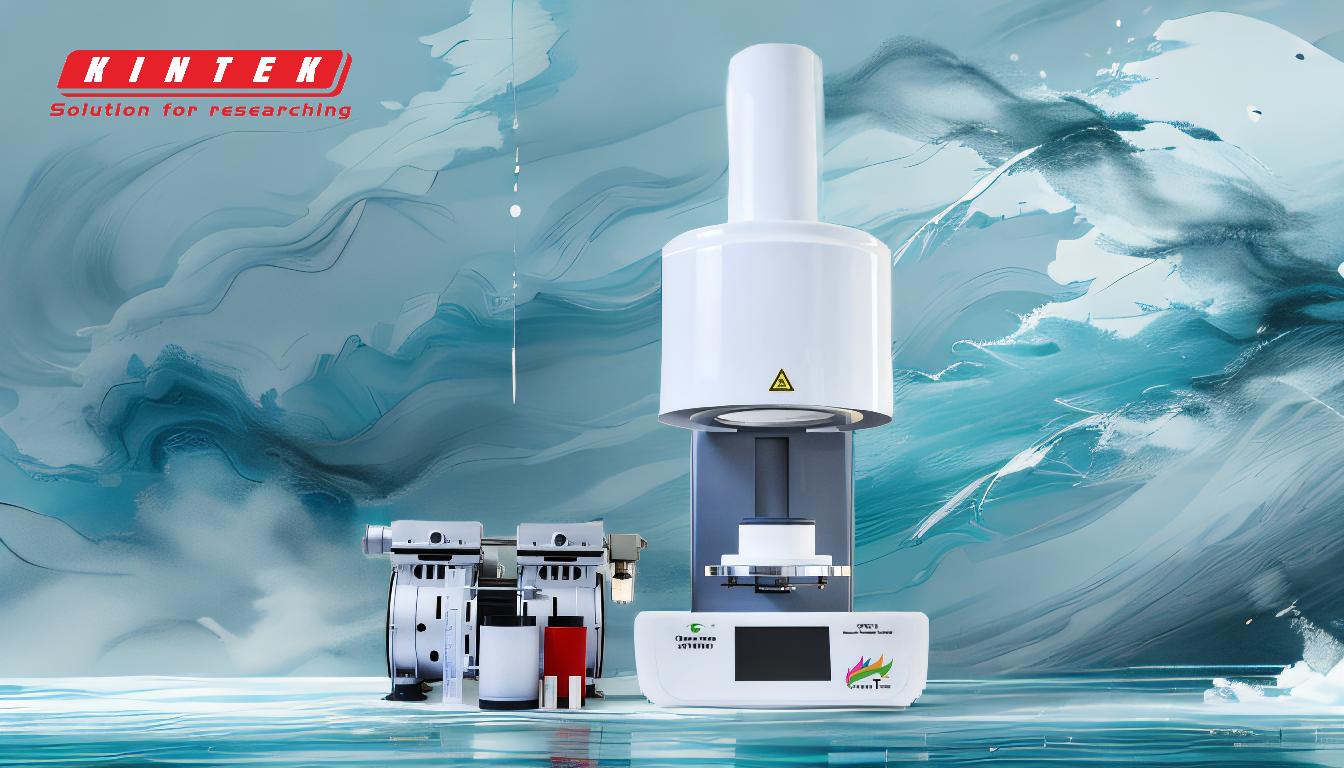
-
Purpose of Quenching:
- Quenching is primarily used to rapidly cool a metal after it has been heated to a high temperature, typically during the austenitizing phase. This rapid cooling transforms the microstructure from austenite to martensite, which is much harder and more brittle. The primary goal is to achieve high hardness and strength in the metal, which is essential for applications requiring wear resistance and durability.
-
Microstructural Transformation:
- During quenching, the rapid cooling traps the chemical elements diffused at high temperatures, creating internal stresses in the crystalline structure. This transformation from austenite to martensite is crucial for enhancing certain mechanical properties, such as hardness and strength. The martensitic structure is characterized by its needle-like appearance under a microscope and is known for its high hardness.
-
Cooling Mediums:
- The choice of cooling medium (oil, water, or air) significantly affects the outcome of the quenching process. Oil quenching, for example, is commonly used to achieve a martensitic structure while minimizing the risk of cracking or distortion. Water quenching is faster and can achieve higher hardness but may introduce more internal stresses. Air cooling is slower and is typically used for materials that are less sensitive to rapid cooling.
-
Quenching and Tempering:
- Quenching is often followed by tempering, a process that involves reheating the metal to a lower temperature to reduce brittleness and improve toughness. This two-step process allows manufacturers to achieve a balance between hardness and toughness, making the material suitable for a wide range of applications. Tempering also helps in relieving internal stresses introduced during quenching.
-
Quench Testing:
- Quench testing is conducted to determine the hardenability of steel, which is its ability to harden under specific conditions. This testing helps manufacturers select the appropriate alloy and heat treatment process to achieve the desired mechanical properties while minimizing risks such as distortion and thermal stresses. The results of quench testing are crucial for optimizing the heat treatment process.
-
Applications and Benefits:
- Quenching is widely used in industries that require high-strength and wear-resistant materials, such as automotive, aerospace, and tool manufacturing. The process enhances the mechanical properties of metals, making them suitable for demanding applications. By carefully controlling the quenching process, manufacturers can produce materials with tailored properties that meet specific performance requirements.
In summary, quenching is a vital heat treatment process that significantly impacts the mechanical properties of metals. By rapidly cooling the metal, quenching transforms its microstructure, increasing hardness and strength. The choice of cooling medium and the subsequent tempering process are crucial for achieving the desired balance of hardness and toughness. Understanding and optimizing the quenching process is essential for producing high-performance materials in various industrial applications.
Summary Table:
Aspect | Description |
---|---|
Purpose | Rapidly cools metal to achieve high hardness and strength. |
Microstructural Change | Transforms austenite to martensite, increasing hardness. |
Cooling Mediums | Oil, water, or air—each affects hardness and stress levels differently. |
Quenching & Tempering | Tempering reduces brittleness post-quenching, balancing hardness and toughness. |
Applications | Used in automotive, aerospace, and tool manufacturing for wear-resistant parts. |
Optimize your heat treatment process with expert guidance—contact us today!