In the context of furnaces, a retort refers to a sealed chamber or vessel used in industrial or laboratory settings to carry out processes that require controlled environments, such as heat treatment, chemical reactions, or material processing. The retort is designed to isolate the material being processed from external contaminants, ensuring precise control over temperature, pressure, and atmosphere. This setup is particularly useful in applications like annealing, brazing, sintering, or other thermal processes where contamination or oxidation must be avoided. Retorts are commonly used in industries such as metallurgy, ceramics, and semiconductor manufacturing.
Key Points Explained:
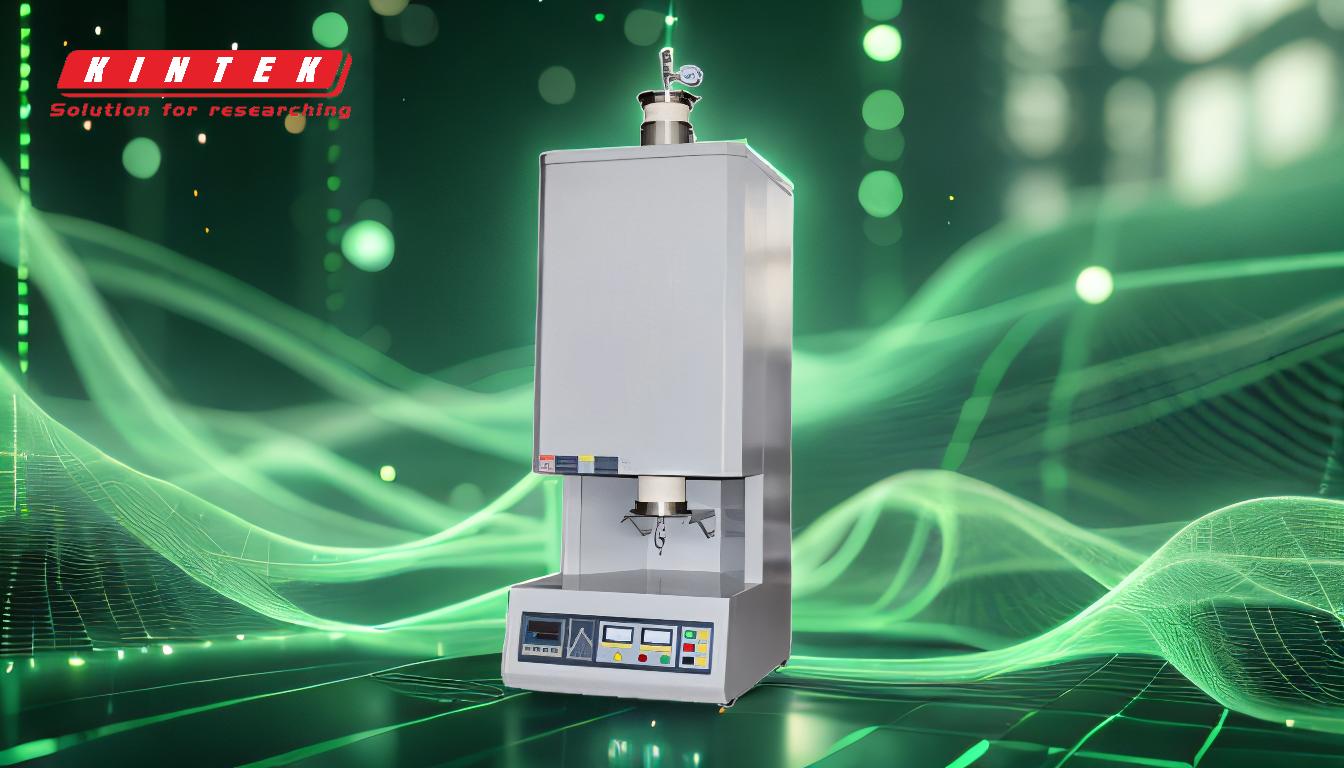
-
Definition of a Retort in Furnaces:
- A retort is a sealed chamber or vessel integrated into a furnace to create an isolated environment for processing materials. It is often made of materials like stainless steel, ceramics, or other alloys that can withstand high temperatures and corrosive atmospheres. The retort ensures that the material inside is protected from external contaminants, such as oxygen or moisture, which could interfere with the process.
-
Purpose of a Retort:
- The primary purpose of a retort is to provide a controlled environment for processes that require specific atmospheric conditions. For example:
- Heat Treatment: Retorts are used in processes like annealing, where metals are heated and cooled to alter their properties without oxidation.
- Brazing: A retort furnace can create an oxygen-free environment to prevent oxidation during the joining of metals.
- Sintering: In powder metallurgy, retorts are used to compact and fuse powdered materials without contamination.
- The primary purpose of a retort is to provide a controlled environment for processes that require specific atmospheric conditions. For example:
-
Types of Retorts:
- Retorts can vary in design and material depending on the application:
- Batch Retorts: Used for processing materials in discrete batches, often in smaller-scale operations.
- Continuous Retorts: Designed for continuous processing, where materials move through the retort in a controlled manner, ideal for large-scale industrial applications.
- Material-Specific Retorts: Some retorts are tailored for specific materials, such as those used in the semiconductor industry for silicon wafer processing.
- Retorts can vary in design and material depending on the application:
-
Atmosphere Control in Retorts:
- Retorts are often equipped with systems to control the internal atmosphere. This can include:
- Inert Gases: Nitrogen or argon is used to create an oxygen-free environment.
- Vacuum Systems: Some retorts operate under vacuum conditions to eliminate any gaseous contaminants.
- Reactive Gases: In certain processes, gases like hydrogen or carbon dioxide are introduced to facilitate specific chemical reactions.
- Retorts are often equipped with systems to control the internal atmosphere. This can include:
-
Applications of Retort Furnaces:
- Retort furnaces are widely used in various industries:
- Metallurgy: For processes like hardening, tempering, and annealing of metals.
- Ceramics: For sintering ceramic materials to achieve high strength and density.
- Semiconductor Manufacturing: For processes like diffusion and oxidation of silicon wafers.
- Chemical Processing: For reactions that require precise temperature and atmospheric control.
- Retort furnaces are widely used in various industries:
-
Advantages of Using a Retort:
- Contamination Prevention: The sealed environment prevents oxidation and contamination, ensuring high-quality results.
- Precision Control: Retorts allow for precise control over temperature, pressure, and atmosphere, which is critical for many industrial processes.
- Versatility: Retorts can be adapted for a wide range of applications, making them a valuable tool in many industries.
-
Challenges and Considerations:
- While retorts offer many advantages, there are also challenges:
- Cost: Retort furnaces can be expensive due to the specialized materials and systems required.
- Maintenance: The sealed nature of retorts means they require regular maintenance to ensure integrity and performance.
- Energy Consumption: Retort furnaces often consume significant energy, especially in high-temperature applications.
- While retorts offer many advantages, there are also challenges:
By understanding the role and functionality of a retort in furnaces, industries can better leverage this technology to achieve precise and contamination-free processing of materials.
Summary Table:
Aspect | Details |
---|---|
Definition | Sealed chamber for isolating materials in controlled environments. |
Purpose | Prevents contamination, ensures precise temperature and atmosphere control. |
Types | Batch, Continuous, Material-Specific. |
Atmosphere Control | Inert gases, vacuum systems, reactive gases. |
Applications | Metallurgy, ceramics, semiconductor manufacturing, chemical processing. |
Advantages | Contamination prevention, precision control, versatility. |
Challenges | High cost, maintenance requirements, energy consumption. |
Ready to enhance your industrial processes with retort furnaces? Contact us today to learn more!