Annealing is a heat treatment process used to alter the physical and sometimes chemical properties of a material, typically metals, to increase ductility and reduce hardness, making it more workable. The furnace used for annealing depends on the material being treated, the required temperature, and the specific annealing process. Common types of furnaces used for annealing include roller hearth furnaces, pusher furnaces, box furnaces, pot/pit furnaces, conveyor belt furnaces, and integral-quench furnaces. These furnaces are designed to provide precise temperature control and uniform heating, which are critical for achieving the desired material properties.
Key Points Explained:
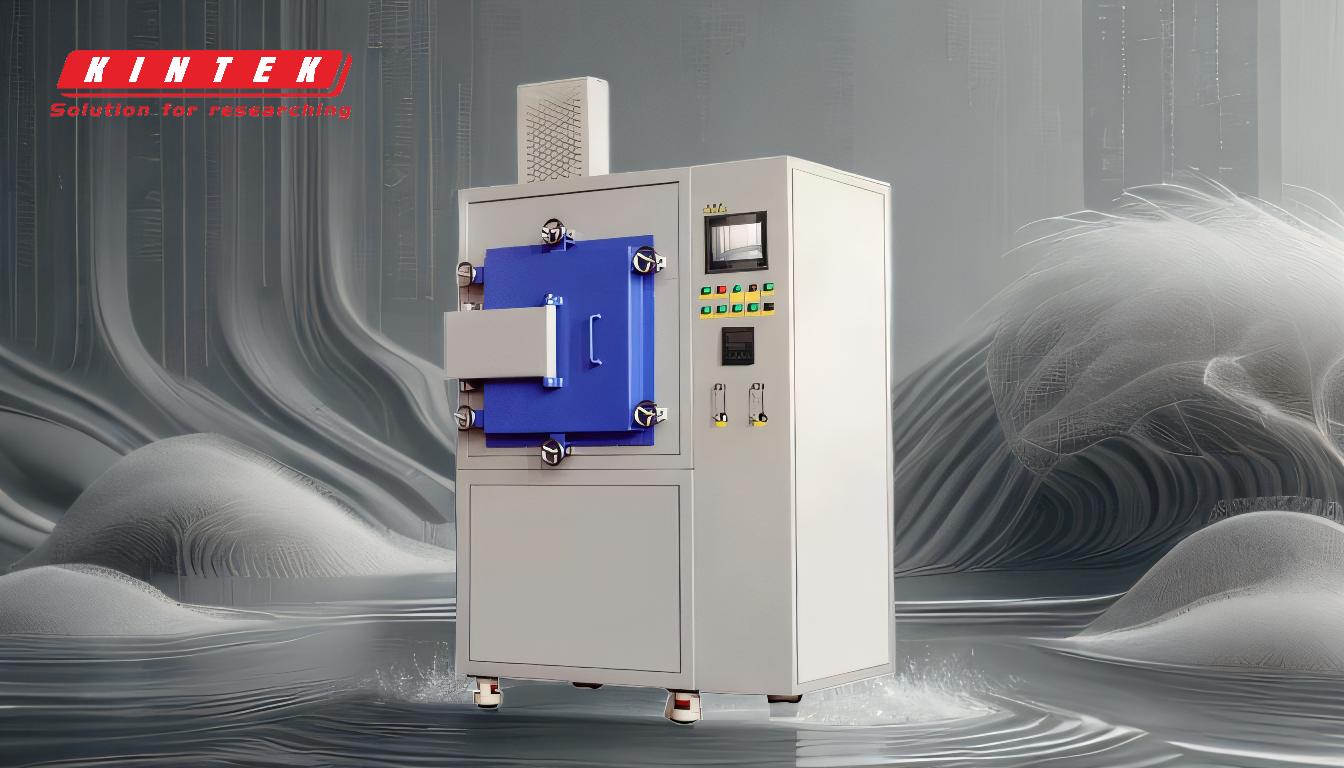
-
Types of Annealing Furnaces:
- Roller Hearth Furnaces: These are continuous furnaces where materials are moved through the heating chamber on rollers. They are ideal for annealing long products like rods, wires, and strips.
- Pusher Furnaces: In these furnaces, materials are pushed through the heating chamber in batches. They are suitable for annealing large volumes of parts or components.
- Box Furnaces: These are batch-type furnaces where materials are placed inside a sealed chamber. They are versatile and can be used for annealing a variety of materials, including metals and alloys.
- Pot/Pit Furnaces: These furnaces are used for annealing small batches of materials, often in a controlled atmosphere to prevent oxidation.
- Conveyor Belt Furnaces: These are continuous furnaces where materials are transported through the heating chamber on a conveyor belt. They are commonly used for annealing small parts or components.
- Integral-Quench Furnaces: These furnaces combine heating and quenching in a single unit, making them suitable for processes that require rapid cooling after annealing.
-
Temperature Ranges for Annealing:
- Low-Temperature Annealing (0-700°C): Used for tempering or sub-critical annealing of steel. Furnaces used in this range often have forced air circulation or liquid baths (oil, lead, or salt) to ensure uniform heating.
- Medium-Temperature Annealing (700-1050°C): Used for hardening, normalizing, and carburizing of carbon and low alloy steels. General-purpose furnaces are typically used in this range.
- High-Temperature Annealing (1000-1400°C): Used for heat treatment of high-speed steels and other high-temperature cycles. High-temperature furnaces are required for this range.
-
Material-Specific Annealing Furnaces:
- Annealing Furnaces for Stainless Steel and Copper: These furnaces are specifically designed for processing stainless steel (SS) or copper wire, rod, strand, strip, and tube products. They are suitable for copper, copper alloy, nickel, nickel chrome, titanium, stainless steel, and refractory metals.
- Furnaces for Aerospace Heat Treating: These include specialized furnaces like vacuum retorts, heat treating salt pots, and pit furnace retorts, which are used for annealing aerospace components that require precise temperature control and uniform heating.
-
Furnace Features for Annealing:
- Temperature Uniformity: Essential for achieving consistent material properties. Furnaces are equipped with strategically positioned heating elements around the chamber to ensure uniform heating.
- Controlled Atmosphere: Some annealing processes require a controlled atmosphere (e.g., inert gas) to prevent oxidation or other chemical reactions during heating.
- Cooling Systems: Integral-quench furnaces and other specialized furnaces may include cooling systems to rapidly cool materials after annealing, which is critical for certain heat treatment processes.
-
Applications of Annealing Furnaces:
- Industrial Products: Furnaces like Rotary Drum Furnaces, Roller Hearth Kilns, Pusher Slab Kilns, and Lift Bottom Kilns are used for sintering and annealing industrial products.
- Aerospace Components: Specialized furnaces are used for annealing aerospace components, where precision and uniformity are critical.
In summary, the choice of furnace for annealing depends on the material, the required temperature range, and the specific annealing process. Each type of furnace offers unique features and benefits, ensuring that the annealing process is carried out efficiently and effectively to achieve the desired material properties.
Summary Table:
Aspect | Details |
---|---|
Types of Furnaces | Roller Hearth, Pusher, Box, Pot/Pit, Conveyor Belt, Integral-Quench |
Temperature Ranges | Low (0-700°C), Medium (700-1050°C), High (1000-1400°C) |
Key Features | Temperature Uniformity, Controlled Atmosphere, Cooling Systems |
Applications | Industrial Products, Aerospace Components, Stainless Steel, Copper Alloys |
Discover the perfect annealing furnace for your needs—contact our experts today!