A rotary kiln is a cylindrical, slightly inclined furnace that rotates slowly to process materials at extremely high temperatures. It is designed to carry out various thermal processes such as calcination, incineration, thermal desorption, and organic combustion. The kiln operates by feeding materials into the upper end, where they tumble and mix as they move downward due to gravity and rotation. Hot gases, generated either internally or externally, flow through the kiln to heat the materials uniformly. The combination of rotation, inclination, and high temperatures ensures thorough processing, enabling chemical reactions or physical changes in the materials before they exit at the lower end.
Key Points Explained:
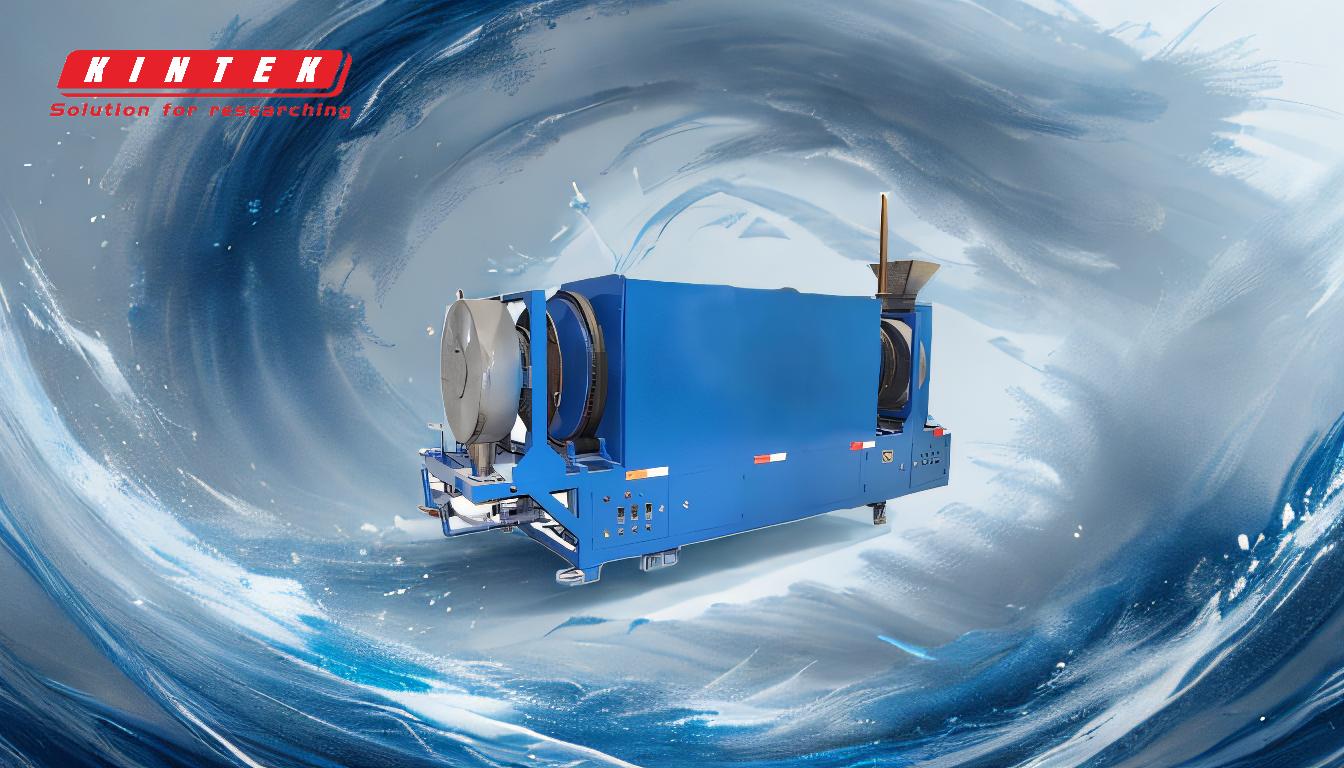
-
Structure and Design of a Rotary Kiln
- A rotary kiln is a large, hollow, cylindrical vessel slightly inclined from the horizontal.
- The inclination and rotation allow materials to move from the upper (feed) end to the lower (discharge) end.
- The kiln's internal configuration can be adjusted to optimize material tumbling and heat exposure.
-
Material Movement and Mixing
- Materials are fed into the kiln through the upper end using a feeding device, such as a screw feeder.
- As the kiln rotates, the materials tumble and mix, ensuring even exposure to heat.
- The rotation and inclination facilitate the gradual movement of materials toward the exit port.
-
Heat Generation and Transfer
- High temperatures ranging from 800°F to 2,200°F are generated inside the kiln.
- Heat is provided by hot gases, which can flow in the same direction as the material (co-current) or in the opposite direction (counter-current).
- The hot gases may be produced by an external furnace or by a flame inside the kiln, fueled by gas, oil, pulverized petroleum coke, or coal.
-
Thermal Processes in a Rotary Kiln
- Calcination: Heating materials to high temperatures to decompose or remove volatile components.
- Incineration: Burning waste materials to reduce volume and eliminate harmful substances.
- Thermal Desorption: Removing contaminants from materials through heat.
- Organic Combustion: Burning organic materials to produce energy or reduce waste.
- Sintering/Induration: Heating materials to form a solid mass without melting.
- Heat Setting: Applying heat to set or cure materials.
-
Operational Adjustments
- The kiln's rotation speed and inclination can be adjusted to control the residence time of materials inside the kiln.
- The flow of hot gases can be optimized to ensure uniform heating and efficient processing.
- Internal configurations, such as baffles or lifters, can be used to enhance material mixing and heat transfer.
-
Applications of Rotary Kilns
- Rotary kilns are widely used in industries such as cement production, metallurgy, waste management, and chemical processing.
- They are essential for processes requiring high-temperature treatment, such as producing lime, alumina, and iron ore pellets.
-
Advantages of Rotary Kilns
- Continuous processing allows for high throughput and efficiency.
- Uniform heating ensures consistent product quality.
- Versatility in handling various materials and processes.
By combining these elements, rotary kilns provide a robust and efficient solution for high-temperature thermal processing, making them indispensable in many industrial applications.
Summary Table:
Aspect | Details |
---|---|
Structure | Cylindrical, slightly inclined vessel for material movement and heat exposure. |
Material Movement | Fed at upper end, tumbles and mixes due to rotation and inclination. |
Heat Generation | High temperatures (800°F–2,200°F) from hot gases (co-current/counter-current). |
Thermal Processes | Calcination, incineration, thermal desorption, organic combustion, sintering. |
Applications | Cement production, metallurgy, waste management, chemical processing. |
Advantages | High throughput, uniform heating, versatility in materials and processes. |
Need a rotary kiln for your industrial needs? Contact our experts today to find the perfect solution!