When ceramic materials are heated, they undergo a series of physical and chemical changes depending on the temperature, composition, and structure of the ceramic. These changes can include thermal expansion, phase transitions, sintering, and, in some cases, decomposition or melting. The behavior of ceramics under heat is critical in applications such as manufacturing, engineering, and materials science. Understanding these changes helps in selecting the right ceramic for specific high-temperature applications, ensuring durability and performance.
Key Points Explained:
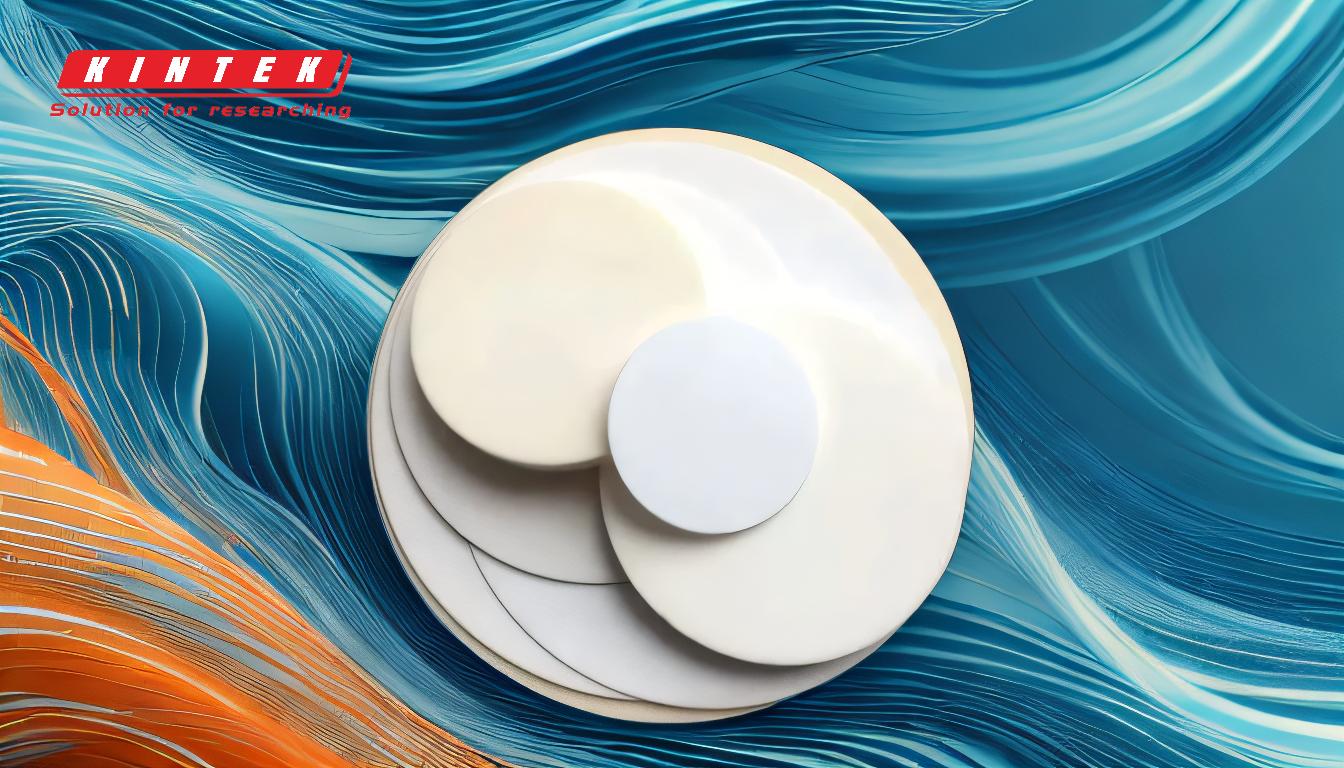
-
Thermal Expansion:
- Explanation: Ceramics generally expand when heated due to the increased vibrational energy of their atomic structure. The degree of expansion depends on the material's coefficient of thermal expansion (CTE). For example, alumina (Al₂O₃) has a CTE of about 8 × 10⁻⁶/°C, while silicon carbide (SiC) has a lower CTE of around 4 × 10⁻⁶/°C.
- Implications: High thermal expansion can lead to cracking or failure in ceramic components if not accounted for in design. This is particularly important in applications like thermal barriers or engine components.
-
Phase Transitions:
- Explanation: Some ceramics undergo phase transitions when heated, where their crystal structure changes. For example, zirconia (ZrO₂) transitions from monoclinic to tetragonal at around 1170°C and then to cubic at 2370°C.
- Implications: Phase transitions can affect mechanical properties such as strength and toughness. Engineers must consider these transitions when designing ceramics for high-temperature environments.
-
Sintering:
- Explanation: Sintering is a process where ceramic particles bond together when heated below their melting point. This occurs due to atomic diffusion, reducing porosity and increasing density. For example, alumina sinters at temperatures around 1600°C.
- Implications: Sintering is crucial in manufacturing dense, strong ceramic components. It is used in producing items like cutting tools, bearings, and electronic substrates.
-
Decomposition:
- Explanation: At very high temperatures, some ceramics may decompose chemically. For instance, silicon nitride (Si₃N₄) decomposes into silicon and nitrogen gas at temperatures above 1900°C.
- Implications: Decomposition limits the use of certain ceramics in extreme environments. Understanding decomposition temperatures is essential for selecting materials for high-temperature applications.
-
Melting:
- Explanation: Ceramics have very high melting points due to their strong ionic or covalent bonds. For example, alumina melts at approximately 2072°C, while silicon carbide melts at around 2730°C.
- Implications: High melting points make ceramics ideal for refractory applications, such as furnace linings and crucibles, where they must withstand extreme heat.
-
Thermal Shock Resistance:
- Explanation: Thermal shock occurs when a material experiences rapid temperature changes, leading to stress and potential cracking. Ceramics with low CTE and high fracture toughness, like silicon nitride, exhibit better thermal shock resistance.
- Implications: Thermal shock resistance is critical in applications like aerospace components and thermal barrier coatings.
-
Electrical and Thermal Conductivity:
- Explanation: Heating can alter the electrical and thermal conductivity of ceramics. For example, some ceramics become more conductive at high temperatures due to increased electron mobility.
- Implications: This property is exploited in applications like heating elements (e.g., silicon carbide heaters) and thermoelectric materials.
-
Oxidation and Chemical Stability:
- Explanation: Many ceramics, such as alumina and silicon carbide, are highly resistant to oxidation even at high temperatures. This makes them suitable for use in oxidizing environments.
- Implications: Oxidation resistance is vital in applications like gas turbine components and chemical processing equipment.
-
Mechanical Properties:
- Explanation: Heating can affect the hardness, strength, and toughness of ceramics. For instance, zirconia-toughened alumina (ZTA) retains high strength and toughness even at elevated temperatures.
- Implications: Retaining mechanical properties at high temperatures is essential for structural ceramics used in engines and cutting tools.
-
Applications and Material Selection:
- Explanation: The behavior of ceramics under heat directly influences their suitability for specific applications. For example, silicon carbide is chosen for high-temperature furnace components due to its thermal conductivity and oxidation resistance.
- Implications: Understanding how ceramics respond to heat helps engineers select the right material for applications ranging from aerospace to electronics.
By considering these factors, purchasers and engineers can make informed decisions about ceramic materials for high-temperature applications, ensuring optimal performance and longevity.
Summary Table:
Property | Explanation | Implications |
---|---|---|
Thermal Expansion | Ceramics expand due to increased atomic vibration. CTE varies by material. | High expansion can cause cracking; critical in thermal barriers and engines. |
Phase Transitions | Crystal structure changes at specific temperatures (e.g., zirconia at 1170°C). | Affects strength and toughness; crucial for high-temperature designs. |
Sintering | Particles bond below melting point, reducing porosity and increasing density. | Essential for manufacturing dense, strong components like cutting tools. |
Decomposition | Some ceramics decompose at very high temperatures (e.g., Si₃N₄ above 1900°C). | Limits use in extreme environments; critical for material selection. |
Melting | Ceramics have high melting points (e.g., alumina at 2072°C, SiC at 2730°C). | Ideal for refractory applications like furnace linings and crucibles. |
Thermal Shock Resistance | Low CTE and high fracture toughness improve resistance to rapid temperature changes. | Vital for aerospace components and thermal barrier coatings. |
Electrical/Thermal Conductivity | Conductivity increases at high temperatures due to electron mobility. | Used in heating elements (e.g., SiC heaters) and thermoelectric materials. |
Oxidation Resistance | High resistance to oxidation (e.g., alumina, SiC) in oxidizing environments. | Suitable for gas turbines and chemical processing equipment. |
Mechanical Properties | Strength, hardness, and toughness are retained at high temperatures (e.g., ZTA). | Critical for structural ceramics in engines and cutting tools. |
Applications | Heat behavior influences material suitability (e.g., SiC for furnace components). | Guides selection for aerospace, electronics, and high-temperature engineering. |
Need help selecting the right ceramic for your high-temperature application? Contact our experts today for tailored solutions!