Annealing is a critical heat treatment process used across various industries to improve the properties of metals, particularly their ductility, strength, and ability to withstand further processing. It is widely utilized in industries where metals undergo complex shaping, reforming, or require stress relief. Key industries include medical, automotive, forging, ferrous castings, and electrical applications such as transformers and motors. Additionally, annealing is beneficial for metals like aluminum, brass, and copper, not just steel and alloy steel. The process is essential for reversing work hardening, relieving internal stresses, and enhancing electrical properties, making it indispensable in manufacturing and engineering.
Key Points Explained:
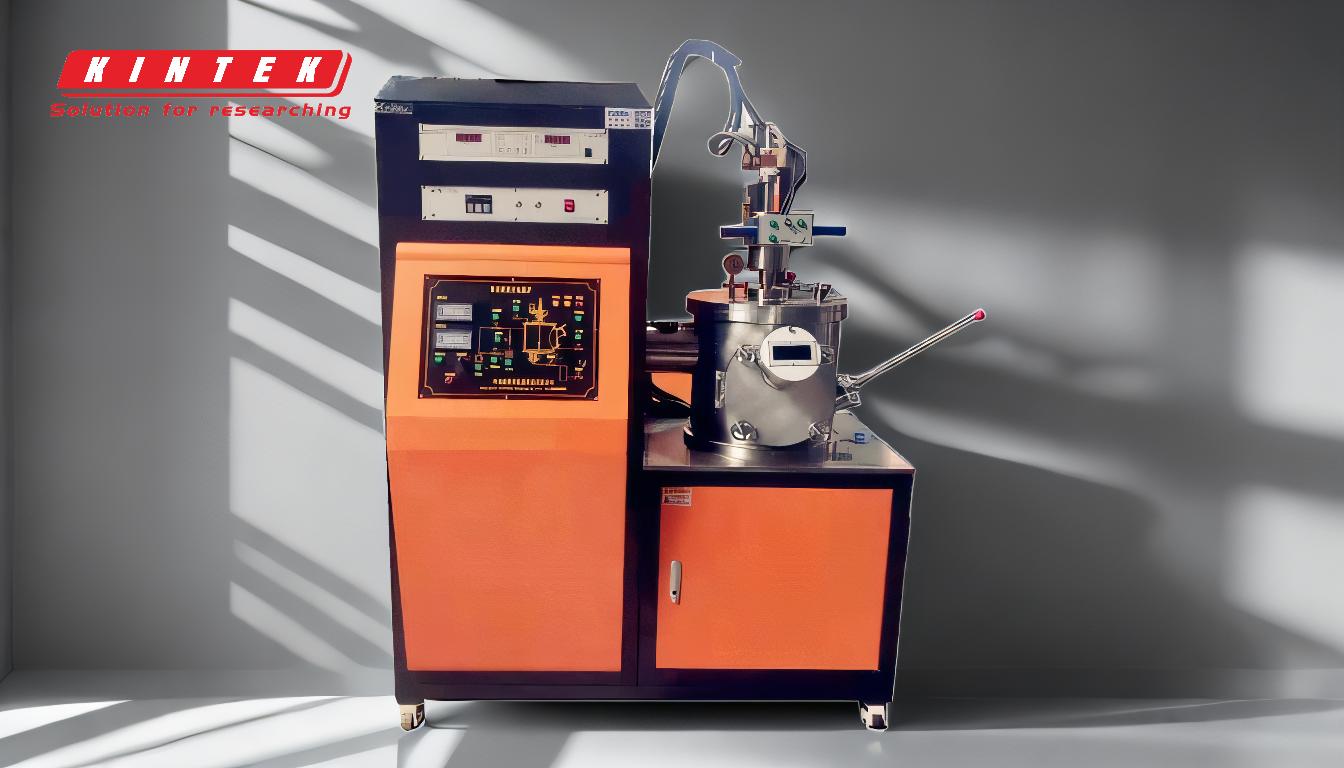
-
Medical Industry:
- Application: Annealing is used in the medical industry to produce precision components such as surgical instruments, implants, and medical devices.
- Purpose: It ensures that metals like stainless steel and titanium are ductile enough for intricate shaping while maintaining strength and biocompatibility.
- Example: Annealing is critical for creating stents and orthopedic implants, where material flexibility and durability are paramount.
-
Automotive Industry:
- Application: Annealing is employed in the manufacturing of automotive parts such as gears, shafts, and engine components.
- Purpose: It improves the formability and machinability of metals, allowing for complex designs and reducing the risk of cracking during fabrication.
- Example: Annealing is used in the production of transmission components to ensure they can withstand high stress and wear.
-
Forging Industry:
- Application: Annealing is integral to forging processes, where metals are shaped under high pressure and temperature.
- Purpose: It restores ductility after cold working, enabling further forging without material failure.
- Example: Forged steel parts like crankshafts and connecting rods often undergo annealing to enhance their mechanical properties.
-
Ferrous Castings Industry:
- Application: Annealing is used in the production of cast iron and steel components.
- Purpose: It relieves internal stresses caused by casting and improves machinability and toughness.
- Example: Annealing is applied to cast iron engine blocks to reduce brittleness and improve performance.
-
Electrical Applications:
- Application: Annealing is crucial in the manufacturing of electrical components such as transformers, motors, and wiring.
- Purpose: It enhances electrical conductivity and reduces internal stresses, ensuring reliable performance.
- Example: Copper and aluminum wires are annealed to improve their flexibility and conductivity for use in electrical systems.
-
Other Metals:
- Application: Annealing is not limited to steel; it is also applied to non-ferrous metals like aluminum, brass, and copper.
- Purpose: It improves ductility, reduces hardness, and prepares these metals for further processing.
- Example: Aluminum sheets used in aerospace applications are annealed to make them easier to form into complex shapes.
-
Reversing Work Hardening:
- Application: Annealing is used to counteract the effects of work hardening caused by cold forming, drawing, or bending.
- Purpose: It restores the metal's ductility, allowing for additional processing without cracking.
- Example: Cold-drawn steel tubes are annealed to enable further shaping without material failure.
-
Stress Relief:
- Application: Annealing is used to remove internal stresses induced by welding, machining, or grinding.
- Purpose: It prevents distortion during subsequent high-temperature treatments and improves dimensional stability.
- Example: Welded structures in construction and heavy machinery are annealed to ensure long-term structural integrity.
-
Improving Electrical Properties:
- Application: Annealing is used to enhance the electrical properties of metals, particularly in wiring and electronic components.
- Purpose: It increases conductivity and reduces resistance, improving efficiency.
- Example: Copper wires in electrical circuits are annealed to optimize their performance.
-
Versatility Across Industries:
- Application: Annealing is a versatile process applicable to a wide range of industries and materials.
- Purpose: It ensures that metals meet the specific requirements of their intended applications, whether for strength, flexibility, or conductivity.
- Example: From medical implants to automotive parts and electrical systems, annealing plays a vital role in modern manufacturing.
In summary, annealing is a foundational process in industries that rely on metal fabrication and shaping. Its ability to enhance material properties, relieve stresses, and enable further processing makes it indispensable in sectors ranging from healthcare to automotive and electrical engineering.
Summary Table:
Industry | Applications | Purpose |
---|---|---|
Medical | Surgical instruments, implants, medical devices | Ensures ductility and biocompatibility for precision components |
Automotive | Gears, shafts, engine components | Improves formability and machinability for complex designs |
Forging | Crankshafts, connecting rods | Restores ductility after cold working |
Ferrous Castings | Cast iron engine blocks | Relieves internal stresses and improves toughness |
Electrical | Transformers, motors, wiring | Enhances conductivity and reduces internal stresses |
Other Metals | Aluminum, brass, copper | Improves ductility and prepares metals for further processing |
Reversing Hardening | Cold-drawn steel tubes | Restores ductility for additional shaping |
Stress Relief | Welded structures, heavy machinery | Prevents distortion and improves dimensional stability |
Electrical Properties | Copper wires, electronic components | Increases conductivity and reduces resistance |
Versatility | Medical implants, automotive parts, electrical systems | Ensures metals meet application-specific requirements |
Learn how annealing can optimize your metal processing—contact our experts today!