A calcining furnace is a specialized industrial furnace designed for the calcination process, which involves heating materials to high temperatures to drive off moisture, remove volatile constituents, or induce chemical changes such as oxidation. This process is critical in industries like cement production, where calcium carbonate is decomposed into calcium oxide and carbon dioxide. Calcining furnaces are equipped with features like high-temperature uniformity, programmable controls, and energy-efficient designs to ensure precise and efficient operation. They are widely used in applications ranging from cement manufacturing to material purification and chemical processing.
Key Points Explained:
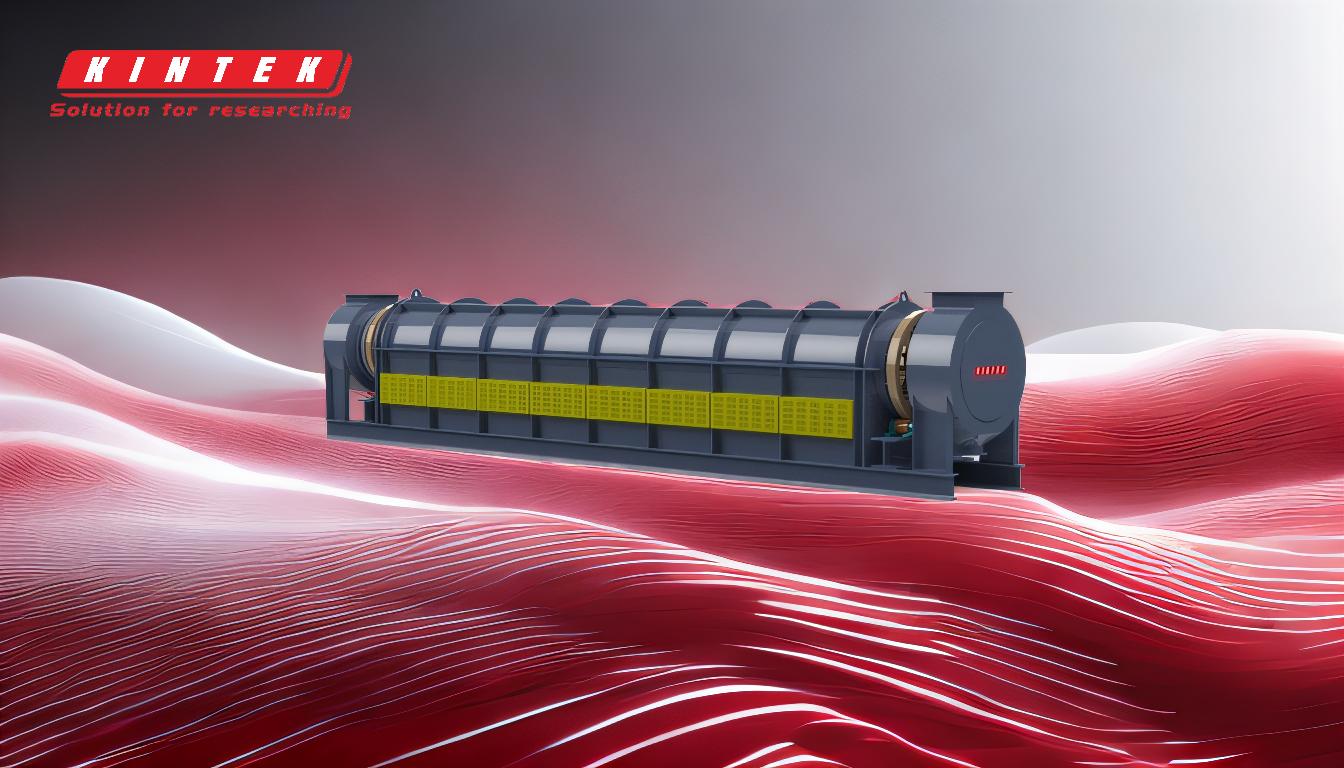
-
Definition and Purpose of a Calcining Furnace:
- A calcining furnace is an industrial furnace used for the calcination process, which involves heating materials to high temperatures to achieve specific chemical or physical transformations.
- The primary purposes of calcination include:
- Driving off absorbed moisture (dehydration).
- Removing volatile constituents like carbon dioxide or sulfur dioxide.
- Oxidizing part or all of the material.
-
Key Applications:
- Cement Production: The most common use of calcining furnaces is in cement manufacturing, where calcium carbonate (limestone) is heated to produce calcium oxide (lime) and carbon dioxide.
- Material Purification: Calcination is used to purify materials by removing impurities or volatile components.
- Chemical Processing: It is employed in processes like oxidation or decomposition to alter the chemical composition of materials.
-
Key Features of Calcining Furnaces:
- High-Temperature Uniformity: Heating elements are positioned on all sides of the chamber to ensure even heat distribution, which is crucial for consistent results.
- Programmable Controls: Modern calcining furnaces often feature programmable segments (e.g., 16 or 30 segments) for precise control over heating rates and temperature profiles.
- Energy Efficiency: Many furnaces use ceramic fiber insulation and double-layer steel casings with cooling fans to minimize energy consumption and ensure operator safety by keeping surface temperatures low.
- Safety Features: Features like automatic temperature control and cooling systems ensure safe operation, even at high temperatures.
-
Comparison with Other Furnaces:
- Sintering Furnaces: While sintering furnaces are also used for high-temperature processes, they focus on bonding particles together rather than driving off volatile components.
- Carbonization Furnaces: These are designed for converting organic materials into carbon, often with a focus on energy efficiency and smokeless operation, unlike calcining furnaces, which focus on chemical transformations.
-
Industrial Significance:
- Calcining furnaces play a vital role in industries like construction (cement production), metallurgy (metal purification), and chemical manufacturing (material decomposition).
- Their ability to precisely control temperature and heating rates makes them indispensable for processes requiring high levels of accuracy and repeatability.
-
Design and Operational Considerations:
- Material Compatibility: The furnace design must account for the specific materials being processed, ensuring compatibility with high temperatures and chemical reactions.
- Temperature Range: Calcining furnaces typically operate at temperatures up to 1200°C, with some models capable of even higher ranges depending on the application.
- Heating Rate Control: Precise control over heating rates is essential to achieve the desired chemical or physical changes without damaging the material.
By understanding these key points, a purchaser can evaluate the suitability of a calcining furnace for their specific needs, ensuring optimal performance and efficiency in their industrial processes.
Summary Table:
Aspect | Details |
---|---|
Purpose | Heating materials to high temperatures for dehydration, oxidation, or decomposition. |
Key Applications | Cement production, material purification, chemical processing. |
Key Features | High-temperature uniformity, programmable controls, energy efficiency, safety features. |
Temperature Range | Up to 1200°C or higher, depending on the application. |
Comparison | Differs from sintering and carbonization furnaces in focus and operation. |
Industrial Significance | Vital for construction, metallurgy, and chemical manufacturing industries. |
Ready to enhance your industrial processes with a calcining furnace? Contact us today to find the perfect solution for your needs!