Molding tools are essential in manufacturing for creating components efficiently and cost-effectively. They enable the precise and rapid production of molds, making them ideal for mass production. By controlling the timing and sequence of process steps, molding tools ensure consistent quality and high output, which is critical for industries requiring large quantities of identical parts. These tools are widely used in industries such as automotive, consumer goods, and electronics, where precision, speed, and scalability are paramount.
Key Points Explained:
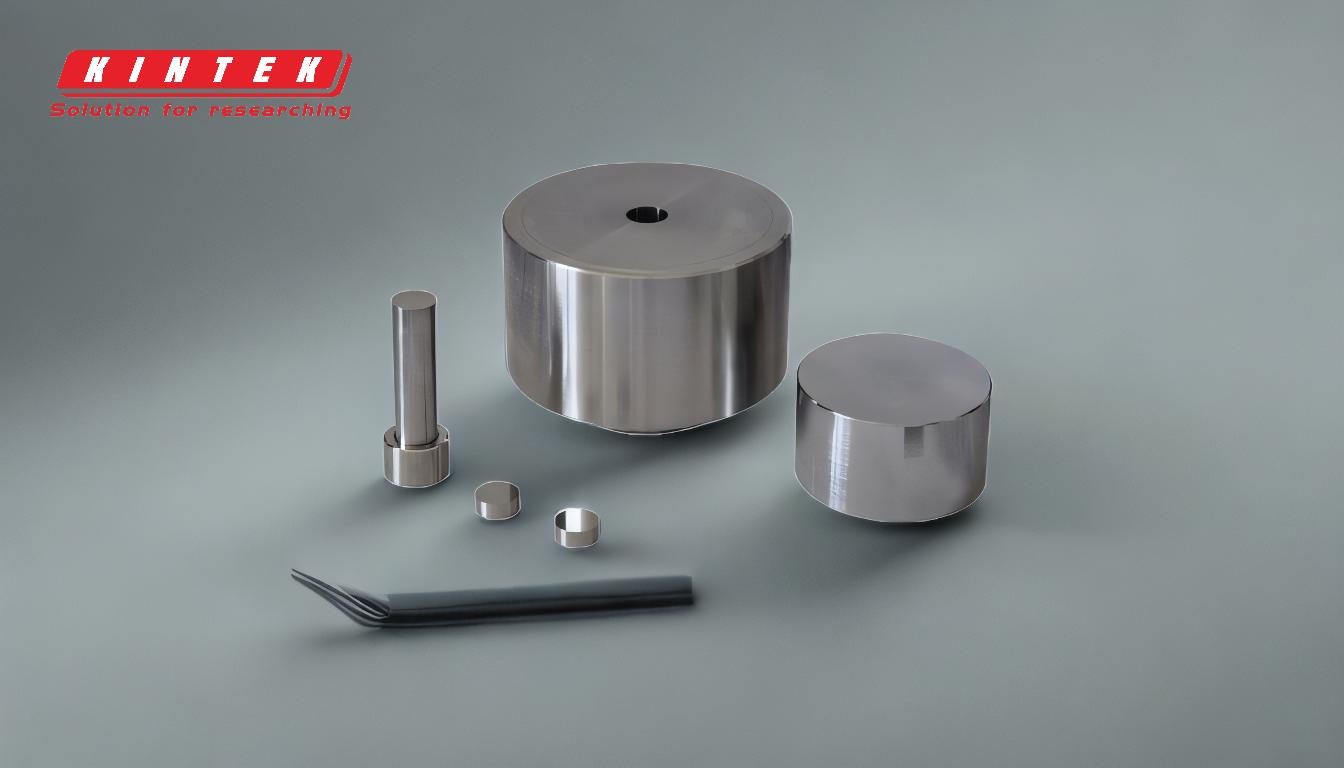
-
Purpose of Molding Tools:
- Molding tools are designed to create molds that are used to manufacture components. These molds can be made from various materials, such as plastic, metal, or rubber, depending on the application.
- The primary goal is to produce parts inexpensively while maintaining high precision and consistency.
-
Efficiency in Production:
- Molding tools streamline the manufacturing process by ensuring precise timing of all process steps. This coordination allows for the rapid production of molds, one after the other.
- The ability to produce molds quickly is crucial for meeting high-volume production demands without compromising quality.
-
Mass Production Capability:
- The speed and efficiency of molding tools make them ideal for mass production. They enable manufacturers to produce large quantities of identical components in a short time.
- This capability is particularly valuable in industries like automotive, consumer goods, and electronics, where large-scale production is required.
-
Cost-Effectiveness:
- By reducing the time and labor required to produce molds, molding tools lower the overall cost of manufacturing. This cost efficiency is achieved through automation and the ability to reuse molds multiple times.
- The initial investment in molding tools is often offset by the long-term savings in production costs.
-
Precision and Consistency:
- Molding tools ensure that each mold is produced with high precision, resulting in components that meet strict quality standards.
- Consistency in production is critical for industries where even minor deviations can lead to product failures or safety issues.
-
Versatility in Applications:
- Molding tools are used across a wide range of industries, including automotive, aerospace, medical devices, and consumer products. Their versatility lies in their ability to produce molds for various materials and shapes.
- This adaptability makes molding tools a valuable asset for manufacturers with diverse product lines.
-
Scalability:
- Molding tools can be scaled up or down depending on production needs. This scalability allows manufacturers to adjust their output based on market demand without significant changes to their production processes.
- The ability to scale production quickly is a key advantage in today's fast-paced market environment.
In summary, molding tools are indispensable in modern manufacturing for their ability to produce high-quality components efficiently, cost-effectively, and at scale. Their precision, consistency, and versatility make them a cornerstone of mass production across various industries.
Summary Table:
Key Aspect | Description |
---|---|
Purpose | Create molds for manufacturing components with precision and cost efficiency. |
Efficiency | Streamline production with precise timing and rapid mold creation. |
Mass Production | Ideal for high-volume output of identical parts in industries like automotive. |
Cost-Effectiveness | Reduce labor and time costs through automation and reusable molds. |
Precision & Consistency | Ensure high-quality components with minimal deviations for safety and reliability. |
Versatility | Adaptable for various materials and shapes across multiple industries. |
Scalability | Adjust production output quickly to meet market demands. |
Ready to enhance your manufacturing process with precision molding tools? Contact us today to learn more!