A sputtering system is a sophisticated setup used in physical vapor deposition (PVD) to deposit thin films of material onto a substrate. It operates by bombarding a target material with high-energy ions, causing atoms to be ejected and deposited onto a substrate within a vacuum chamber. The system typically includes components such as a vacuum chamber, target material, substrate holder, magnetron, and power supply. Sputtering systems are widely used in industries like semiconductor manufacturing, optics, and coatings due to their ability to produce high-quality, uniform films. The process can be adapted for various applications, including reactive sputtering for depositing oxides or nitrides, and RF sputtering for insulating materials.
Key Points Explained:
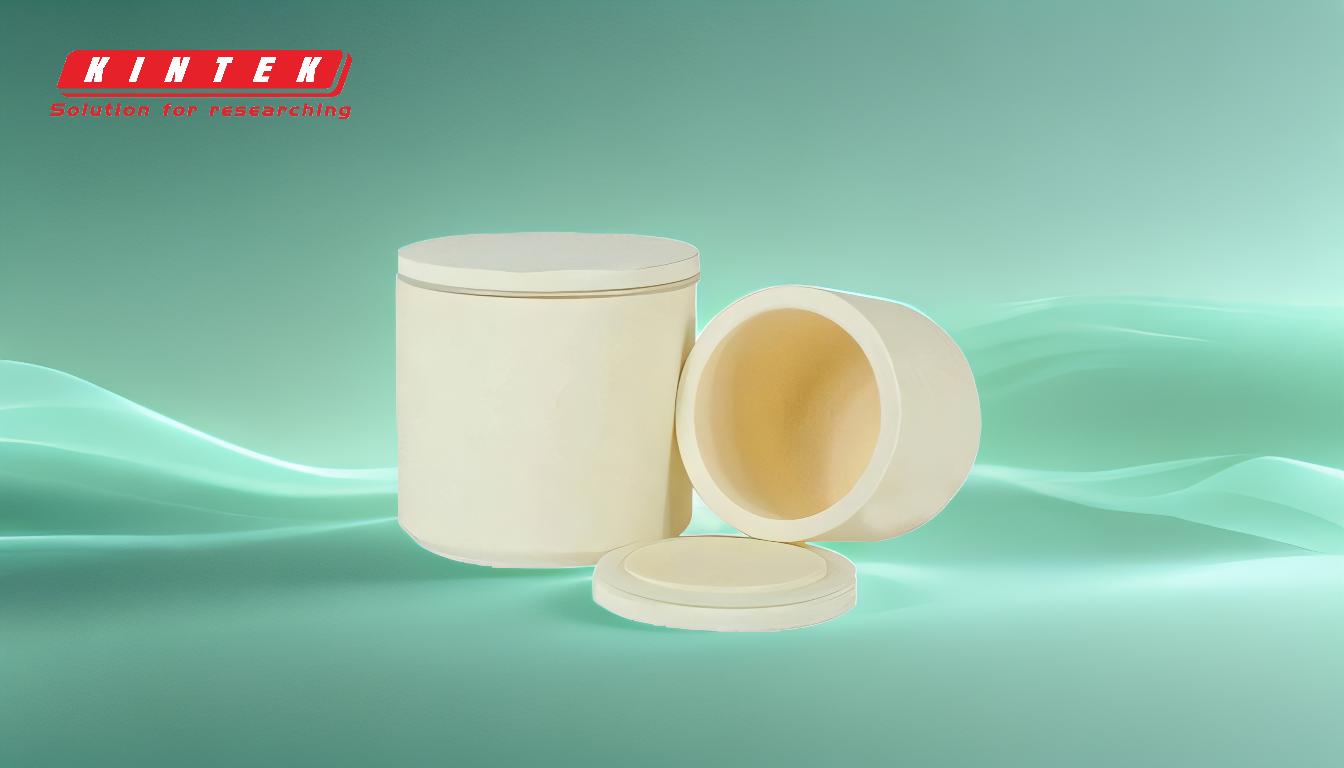
-
Basic Components of a Sputtering System:
- Vacuum Chamber: Maintains a low-pressure environment to ensure clean deposition and prevent contamination.
- Target Material: The source material that is bombarded to produce the thin film.
- Substrate Holder: Holds the substrate where the thin film is deposited.
- Magnetron: Generates a magnetic field to enhance the sputtering process by confining electrons near the target.
- Power Supply: Provides the energy needed to ionize the gas and bombard the target material.
-
Sputtering Process:
- High-energy ions bombard the target material, causing atoms to be ejected into the gas phase.
- These atoms travel through the vacuum chamber and deposit onto the substrate, forming a thin film.
- The process is highly controllable, allowing for precise thickness and composition of the deposited film.
-
Types of Sputtering:
- Reactive Sputtering: Involves sputtering a metal target in the presence of a reactive gas (e.g., oxygen or nitrogen) to deposit compounds like oxides or nitrides.
- RF Sputtering: Uses radio frequency (RF) power to sputter insulating materials, with typical parameters including an RF source frequency of 13.56 MHz and chamber pressures between 0.5 to 10 mTorr.
-
Vacuum Requirements:
- Sputtering systems require a high-vacuum environment (base pressure of 10^-6 mbar or better) to ensure clean surfaces and avoid contamination.
- During sputtering, the pressure is maintained in the mTorr range (10^-3 to 10^-2 mbar), with gas flow controlled by a flow controller.
-
Applications and Advantages:
- Semiconductor Manufacturing: Used for depositing thin films in integrated circuits.
- Optics: Produces anti-reflective and reflective coatings.
- Coatings: Provides wear-resistant and decorative coatings.
- The process offers high deposition rates, excellent film uniformity, and the ability to deposit a wide range of materials, including metals, alloys, and compounds.
-
Magnetron Sputtering:
- Involves two electrodes in a low-pressure inert gas atmosphere (e.g., argon).
- The target material is mounted on the cathode, and a set of permanent magnets beneath the cathode enhances the sputtering efficiency by confining electrons.
-
Heat Management:
- The sputtering process generates significant heat, requiring specialized chilling systems to manage temperature and ensure consistent deposition quality.
By understanding these key points, a purchaser can evaluate sputtering systems based on their specific application needs, considering factors like the type of materials to be deposited, required film properties, and system configuration.
Summary Table:
Aspect | Details |
---|---|
Key Components | Vacuum chamber, target material, substrate holder, magnetron, power supply |
Process | High-energy ions bombard target material, ejecting atoms for deposition |
Types | Reactive sputtering (oxides/nitrides), RF sputtering (insulating materials) |
Vacuum Requirements | Base pressure: 10^-6 mbar; sputtering pressure: 10^-3 to 10^-2 mbar |
Applications | Semiconductors, optics, wear-resistant coatings, decorative coatings |
Advantages | High deposition rates, uniform films, versatile material compatibility |
Ready to enhance your thin film deposition process? Contact us today to find the perfect sputtering system for your needs!