A vacuum casting machine is a specialized equipment used in manufacturing and prototyping to create high-quality replicas of original parts using silicone molds and polyurethane resins. It operates under vacuum conditions to eliminate air bubbles, ensuring precise and detailed reproductions. This process is widely used for small-batch production, rapid prototyping, and creating functional parts with properties similar to injection-molded components. Vacuum casting machines are essential in industries like automotive, aerospace, consumer goods, and medical devices, where accuracy, material versatility, and cost-effectiveness are critical.
Key Points Explained:
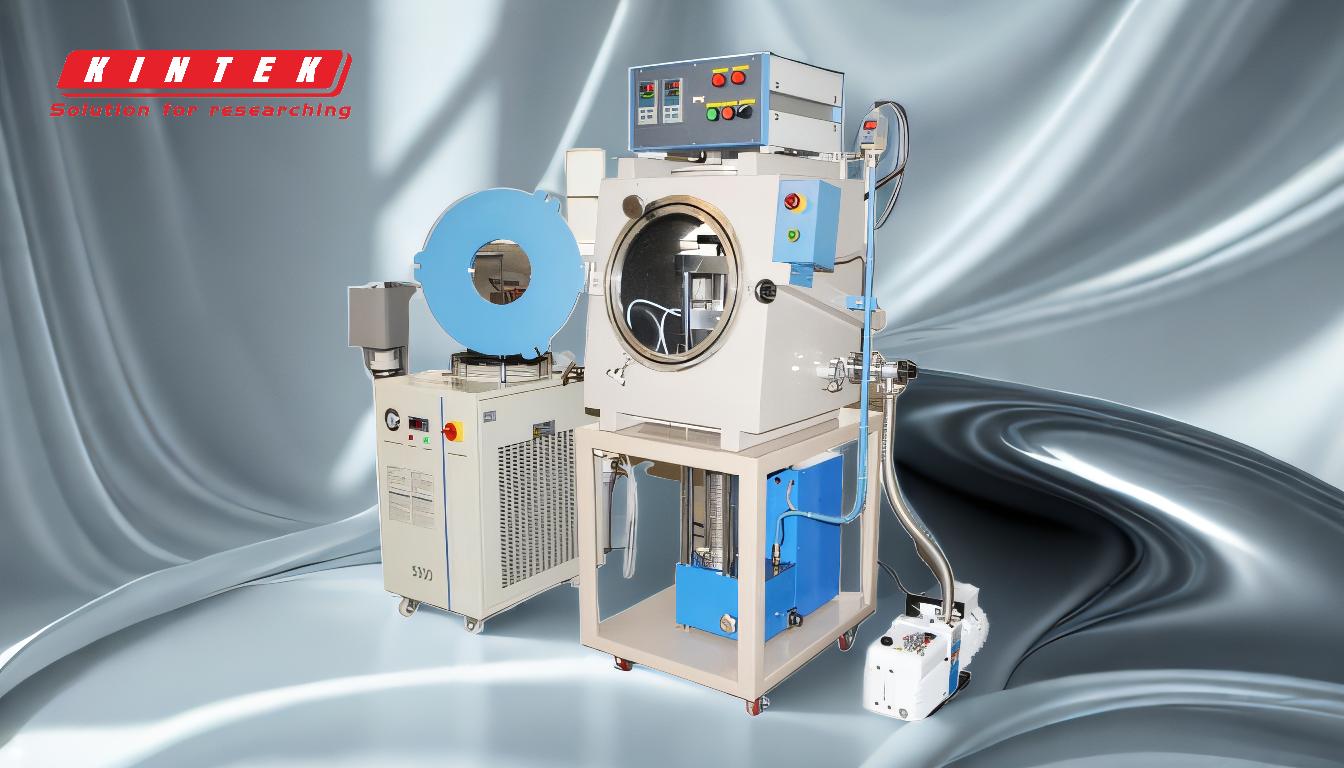
-
Definition and Purpose of a Vacuum Casting Machine
- A vacuum casting machine is a device designed to produce high-quality replicas of parts using silicone molds and liquid resins.
- It is primarily used for prototyping and small-batch production, offering a cost-effective alternative to traditional manufacturing methods like injection molding.
- The vacuum environment ensures the removal of air bubbles, resulting in parts with excellent surface finish and dimensional accuracy.
-
How Vacuum Casting Works
-
Step 1: Mold Creation
A silicone mold is created from a master model, which can be made using 3D printing or CNC machining. -
Step 2: Resin Preparation
Polyurethane resin is mixed with additives to achieve desired material properties, such as flexibility, strength, or transparency. -
Step 3: Vacuum Casting Process
The resin is poured into the silicone mold under vacuum conditions to eliminate air bubbles. The mold is then cured in an oven to harden the resin. -
Step 4: Demolding
Once cured, the part is removed from the mold, and post-processing (e.g., trimming, painting) may be applied.
-
Step 1: Mold Creation
-
Key Components of a Vacuum Casting Machine
-
Vacuum Chamber
The sealed chamber where the casting process takes place under reduced pressure. -
Vacuum Pump
Creates the vacuum environment by removing air from the chamber. -
Mixing System
Ensures thorough mixing of resin and additives before pouring into the mold. -
Curing Oven
Used to accelerate the hardening process of the resin.
-
Vacuum Chamber
-
Advantages of Vacuum Casting
-
High Precision
Produces parts with fine details and tight tolerances. -
Material Versatility
Allows the use of various resins to mimic different materials, such as ABS, polypropylene, or rubber. -
Cost-Effective
Ideal for small-batch production without the need for expensive tooling. -
Fast Turnaround
Suitable for rapid prototyping, enabling quick iterations and design validation.
-
High Precision
-
Applications of Vacuum Casting Machines
-
Prototyping
Used to create functional prototypes for testing and validation. -
Small-Batch Production
Suitable for producing limited quantities of parts for niche markets or pre-production runs. -
Medical Devices
Enables the production of custom medical components with high precision. -
Consumer Goods
Used to manufacture parts for electronics, appliances, and other consumer products.
-
Prototyping
-
Considerations for Purchasing a Vacuum Casting Machine
-
Chamber Size
Choose a machine with a chamber size that accommodates your typical part dimensions. -
Vacuum Level
Ensure the machine can achieve the required vacuum pressure for your applications. -
Material Compatibility
Verify that the machine supports the types of resins and additives you plan to use. -
Ease of Use
Look for features like automated controls and user-friendly interfaces to streamline operations. -
After-Sales Support
Consider the availability of technical support, spare parts, and maintenance services.
-
Chamber Size
By understanding these key points, you can make an informed decision when selecting a vacuum casting machine for your specific needs.
Summary Table:
Key Aspect | Details |
---|---|
Definition | A device for producing high-quality replicas using silicone molds and resins. |
Process | Mold creation, resin preparation, vacuum casting, and demolding. |
Key Components | Vacuum chamber, vacuum pump, mixing system, and curing oven. |
Advantages | High precision, material versatility, cost-effectiveness, and fast turnaround. |
Applications | Prototyping, small-batch production, medical devices, and consumer goods. |
Purchase Considerations | Chamber size, vacuum level, material compatibility, ease of use, and support. |
Ready to enhance your prototyping and production process? Contact us today to find the perfect vacuum casting machine for your needs!