A vertical muffle furnace is a specialized heating device used in various industrial and laboratory settings for high-temperature applications. It is designed to achieve precise temperature control and uniform heating while isolating materials from combustion contaminants. This makes it ideal for processes such as ashing samples, heat treatment, materials research, and testing. Vertical muffle furnaces are widely used in industries like ceramics, metallurgy, electronics, glass, chemicals, and pharmaceuticals. They are also employed in analytical chemistry, coal analysis, and material development. Their ability to operate at extremely high temperatures (often exceeding 2000 ℃) makes them indispensable for tasks like sintering, brazing, and heat treatment of mechanical parts.
Key Points Explained:
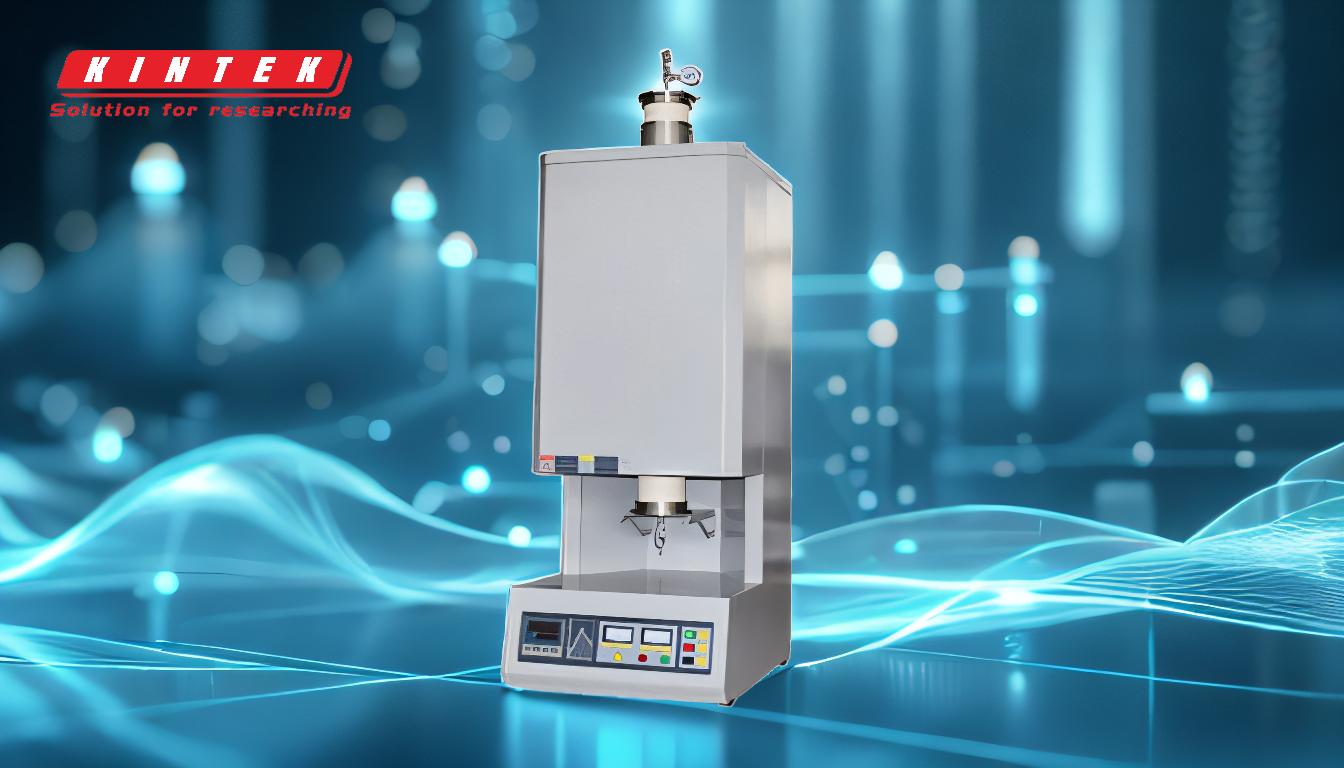
-
Primary Applications of Vertical Muffle Furnaces:
- Ashing Samples: Used to determine the ash content of materials by burning off organic components.
- Heat Treatment: Processes like annealing, tempering, quenching, and normalizing to enhance material properties.
- Materials Research: Testing and developing new materials under high-temperature conditions.
- Sintering and Brazing: Bonding materials at high temperatures without melting them completely.
-
Industries and Sectors Utilizing Vertical Muffle Furnaces:
- Ceramics and Glass: For firing and processing ceramic and glass materials.
- Metallurgy: Heat treatment of metals and alloys to improve mechanical properties.
- Electronics: Processing electronic components and materials.
- Pharmaceuticals: Drug testing and sample pretreatment.
- Analytical Chemistry: Water quality analysis, environmental analysis, and coal analysis.
- Cement and Foundry: Processing raw materials and testing high-temperature properties.
-
Advantages of Vertical Muffle Furnaces:
- Temperature Control: Precise and uniform heating for consistent results.
- Contaminant-Free Environment: Isolation of materials from combustion byproducts.
- High-Temperature Capability: Suitable for applications requiring temperatures over 2000 ℃.
- Versatility: Can be used for a wide range of materials and processes.
-
Specific Use Cases:
- Coal Analysis: Determining moisture, ash, volatile matter, and ash melting points.
- Mechanical Industry: Heating billets, forging, and heat treatment of mechanical parts.
- Nuclear Industry: Processing materials under extreme conditions.
- Food Industry: Burning raw materials for analysis.
-
Operational Features:
- Heating Methods: Conduction, convection, and blackbody radiation for efficient heat transfer.
- Design: Vertical orientation allows for better space utilization and handling of samples.
- Safety: Designed to handle high temperatures safely, with insulation to prevent heat loss.
By combining these key points, it is clear that vertical muffle furnaces are essential tools in both industrial and laboratory environments, offering precise and reliable high-temperature processing capabilities for a wide range of applications.
Summary Table:
Key Aspect | Details |
---|---|
Primary Applications | Ashing samples, heat treatment, materials research, sintering, brazing |
Industries | Ceramics, metallurgy, electronics, pharmaceuticals, analytical chemistry |
Advantages | Precise temperature control, contaminant-free environment, high-temperature capability, versatility |
Specific Use Cases | Coal analysis, mechanical industry, nuclear industry, food industry |
Operational Features | Conduction, convection, blackbody radiation; vertical design; safety-focused |
Learn how a vertical muffle furnace can elevate your high-temperature processes—contact us today!