Induction heating is a versatile and efficient method of heating conductive materials using a magnetic field, without direct contact. It is widely used across industries, from metallurgy and semiconductor manufacturing to domestic cooking. One prominent example of induction heating is its use in induction cooktops, where it provides fast, precise, and energy-efficient heating for cooking. Additionally, induction heating is employed in industrial processes like heat treatment, melting refractory metals, and welding, as well as in specialized applications such as medical tissue heating and plastic welding. Its ability to deliver targeted and controlled heating makes it a preferred choice in many modern applications.
Key Points Explained:
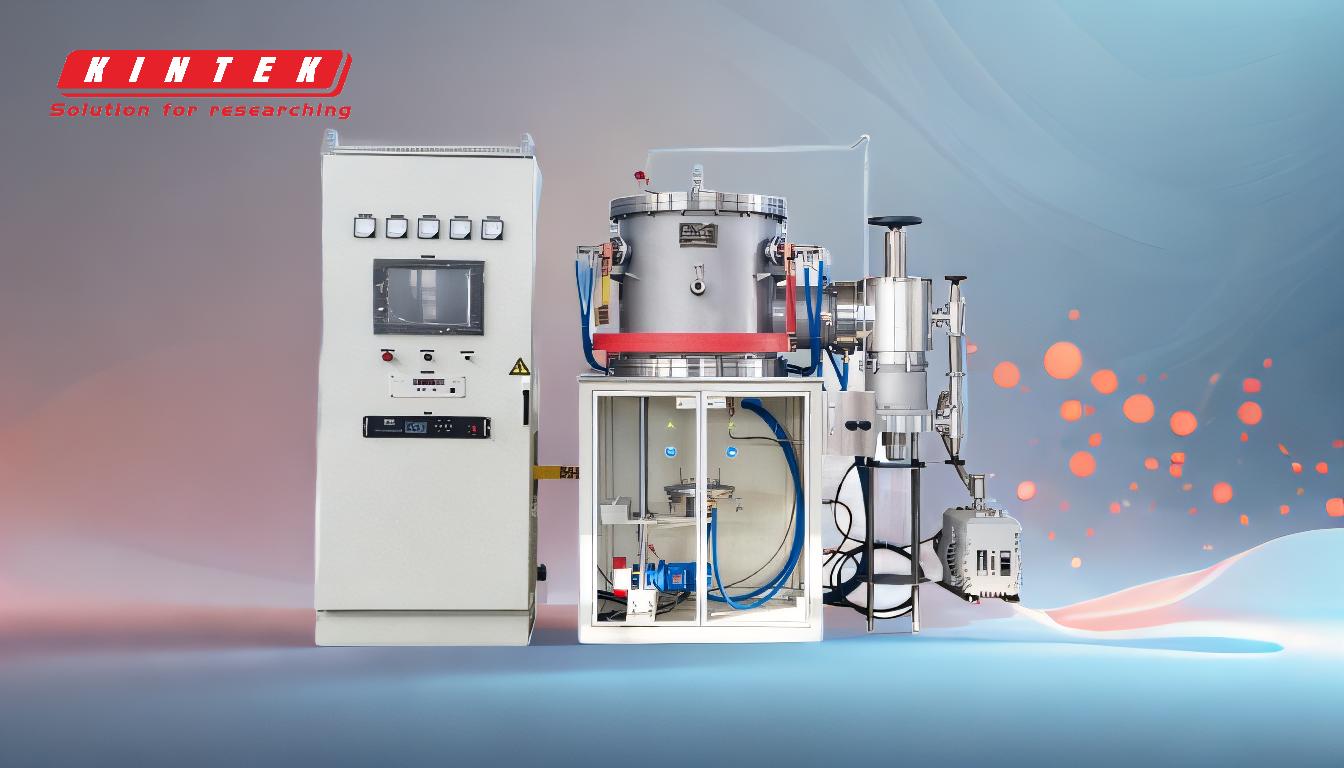
-
Induction Cooktops:
- Induction cooktops are a common example of induction heating in domestic settings. They use electromagnetic fields to directly heat the cookware, rather than the cooktop surface. This results in faster heating, precise temperature control, and energy efficiency.
- The cookware must be made of a ferromagnetic material (e.g., cast iron or stainless steel) to generate eddy currents and heat up. Non-conductive materials like glass or ceramic will not work on induction cooktops.
- This application highlights the convenience and safety of induction heating, as the cooktop surface remains relatively cool, reducing the risk of burns.
-
Industrial Heat Treatment:
- Induction heating is extensively used in metallurgy for heat treatment processes, such as hardening, tempering, and annealing. It allows for localized heating, which is crucial for modifying the properties of specific parts of a metal component.
- For example, in the automotive industry, induction heating is used to harden gears and shafts, improving their durability and wear resistance.
-
Melting Refractory Metals:
- Induction heating is ideal for melting metals that require extremely high temperatures, such as tungsten, molybdenum, and titanium. These metals are used in aerospace, defense, and high-tech industries.
- Induction furnaces provide a clean and controlled environment for melting, ensuring high-quality alloys and minimal contamination.
-
Czochralski Crystal Growth and Zone Refining:
- In the semiconductor industry, induction heating is used in the Czochralski process to grow single-crystal silicon, which is essential for manufacturing microchips and solar cells.
- Zone refining, another semiconductor application, uses induction heating to purify materials by melting and recrystallizing them, removing impurities in the process.
-
Induction Welding:
- Induction welding is used to join metals and even plastics doped with ferromagnetic particles. In this process, eddy currents heat the edges of the materials, which are then pressed together to form a strong bond.
- This method is commonly used in the production of metal tubes and pipes, as well as in specialized applications like sealing tamper-resistant caps on pharmaceutical bottles.
-
Targeted Heating for Medical Applications:
- Induction heating is being explored for medical purposes, such as heating biological tissues for treatments like hyperthermia therapy, which targets cancer cells with controlled heat.
- This application demonstrates the precision and non-invasive nature of induction heating, making it suitable for sensitive medical procedures.
-
Plastic Injection Molding:
- Induction heating is used in plastic injection molding machines to improve energy efficiency and reduce cycle times. By heating specific parts of the mold, the process ensures uniform melting and faster production.
-
Advantages Over Traditional Heating Methods:
- Induction heating offers several benefits, including faster heating rates, precise temperature control, and energy efficiency. It eliminates the need for direct contact, reducing contamination and wear.
- Unlike flame or oven heating, induction heating is cleaner and safer, as it does not involve open flames or combustion byproducts.
-
Emerging Applications:
- With technological advancements, induction heating is expanding into new areas, such as heating low-resistivity materials and optimizing process parameters for specialized applications.
- Research is ongoing to further enhance its capabilities and explore innovative uses in industries like renewable energy, electronics, and advanced manufacturing.
In summary, induction heating is a highly adaptable and efficient technology with a wide range of applications. From everyday uses like induction cooktops to advanced industrial processes like metal melting and semiconductor manufacturing, it continues to play a critical role in modern technology and industry.
Summary Table:
Application | Description |
---|---|
Induction Cooktops | Fast, precise, and energy-efficient heating for domestic cooking. |
Industrial Heat Treatment | Used for hardening, tempering, and annealing metals in industries like automotive. |
Melting Refractory Metals | Ideal for melting high-temperature metals like tungsten and titanium. |
Czochralski Crystal Growth | Essential for growing single-crystal silicon in semiconductor manufacturing. |
Induction Welding | Joins metals and plastics with strong, precise bonds. |
Medical Applications | Non-invasive heating for treatments like hyperthermia therapy. |
Plastic Injection Molding | Improves energy efficiency and reduces cycle times in plastic molding. |
Learn how induction heating can transform your processes—contact us today!