An inert atmosphere heat treatment involves heating materials in a controlled environment filled with non-reactive gases, such as argon or nitrogen, to prevent oxidation, contamination, or other unwanted chemical reactions. This process is essential for maintaining the material's desired properties, such as strength, hardness, and surface finish, during high-temperature operations. Inert atmospheres are commonly used in processes like sintering, bright annealing, carbonitriding, and hot isostatic pressing (HIP). By eliminating reactive gases, the treatment ensures clean, high-quality parts, especially for expensive or precision components. This method is critical in industries where material integrity and surface quality are paramount.
Key Points Explained:
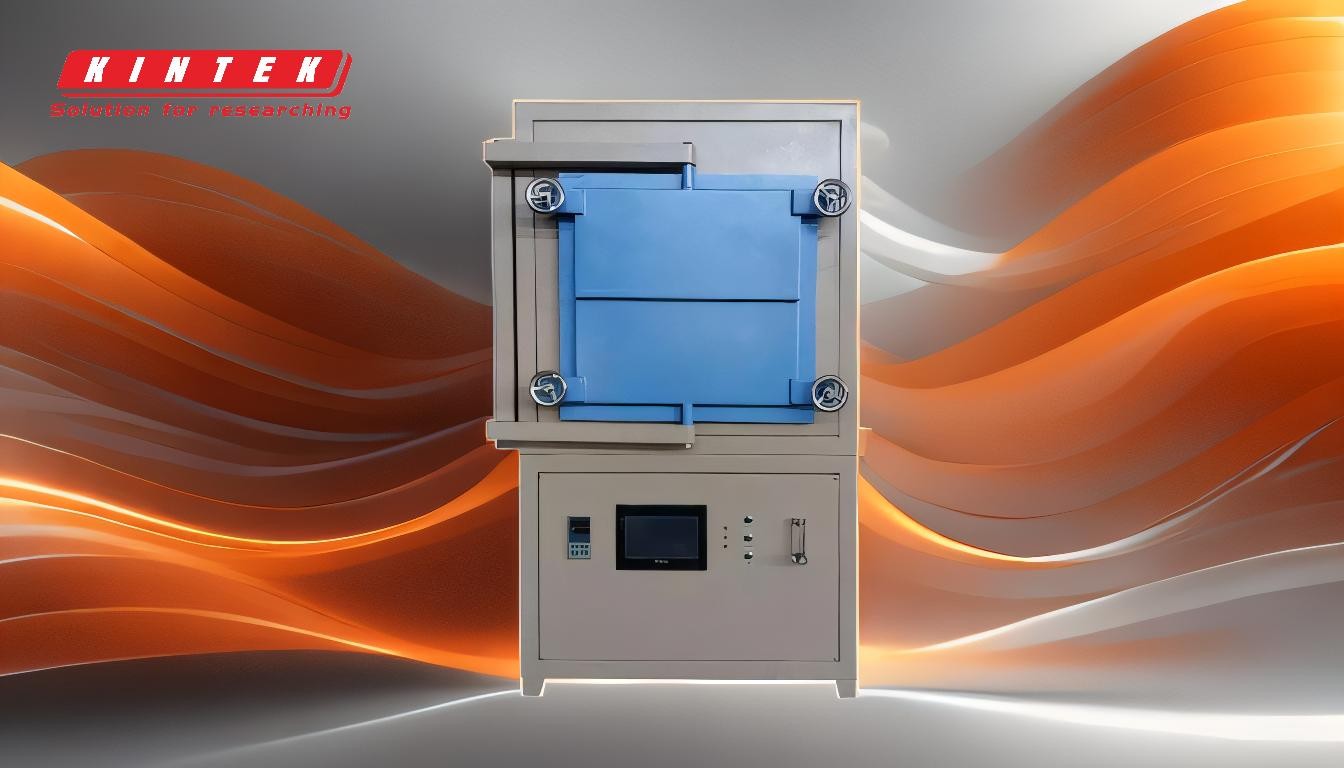
-
Definition of Inert Atmosphere Heat Treatment
- Inert atmosphere heat treatment involves heating materials in a controlled environment filled with non-reactive gases like argon or nitrogen.
- These gases are chosen due to their high natural abundance and inert properties, meaning they do not react with the materials being treated.
-
Purpose of Using an Inert Atmosphere
- Prevents Oxidation: Exposure to oxygen during heat treatment can cause oxidation, which degrades the material's surface and properties.
- Avoids Contamination: Reactive gases in the air can introduce impurities, altering the material's composition and performance.
- Maintains Material Integrity: By eliminating unwanted chemical reactions, the material retains its desired mechanical and physical properties.
-
Applications of Inert Atmosphere Heat Treatment
- Sintering: A process where powdered materials are heated to form a solid mass without melting, often used in metal and ceramic manufacturing.
- Bright Annealing: A heat treatment process that prevents oxidation to achieve a bright, clean surface finish on metals like stainless steel.
- Carbonitriding: A surface hardening process that introduces carbon and nitrogen into the material, enhancing wear resistance.
- Hot Isostatic Pressing (HIP): A technique that uses high pressure and temperature to eliminate porosity and improve material density.
- Vacuum Operations: Heat treatment in a vacuum or low-pressure environment to further reduce the risk of contamination.
-
Benefits of Inert Atmosphere Heat Treatment
- Clean Parts: Produces parts with minimal surface contamination or defects.
- Cost-Effective for High-Value Components: Prevents costly damage to expensive materials during heat treatment.
- Enhanced Material Properties: Ensures consistent hardness, strength, and surface quality.
-
Key Considerations for Equipment and Consumables Purchasers
- Gas Selection: Choose high-purity argon or nitrogen to ensure optimal results.
- Equipment Compatibility: Ensure heat treatment furnaces and chambers are designed to maintain a controlled inert atmosphere.
- Process Control: Invest in systems that monitor and regulate gas flow, temperature, and pressure for consistent outcomes.
- Cost Efficiency: Evaluate the cost of inert gases and their consumption rates to optimize operational expenses.
-
Challenges and Solutions
- Gas Leakage: Ensure proper sealing of heat treatment chambers to maintain the inert atmosphere.
- Gas Purity: Use high-quality, purified gases to avoid introducing impurities.
- Process Monitoring: Implement advanced sensors and control systems to maintain precise conditions throughout the treatment.
By understanding the principles and applications of inert atmosphere heat treatment, purchasers can make informed decisions about equipment and consumables, ensuring high-quality results and cost-effective operations.
Summary Table:
Aspect | Details |
---|---|
Definition | Heating materials in a non-reactive gas environment (e.g., argon, nitrogen). |
Purpose | Prevents oxidation, contamination, and maintains material integrity. |
Applications | Sintering, bright annealing, carbonitriding, HIP, vacuum operations. |
Benefits | Clean parts, cost-effective for high-value components, enhanced properties. |
Key Considerations | Gas selection, equipment compatibility, process control, cost efficiency. |
Challenges & Solutions | Gas leakage, gas purity, process monitoring. |
Optimize your heat treatment process with inert atmosphere solutions—contact our experts today!