An integral quench furnace is a specialized type of heat treatment furnace used primarily in metallurgical and manufacturing processes. It is designed to perform both heating and quenching operations in a single, integrated system, making it highly efficient for processes like hardening, tempering, and annealing. The furnace is particularly useful for industries requiring precise control over the heat treatment process, such as automotive, aerospace, and tool manufacturing. Its ability to handle high-temperature treatments and rapid cooling ensures that materials achieve the desired mechanical properties, such as increased hardness, strength, and wear resistance.
Key Points Explained:
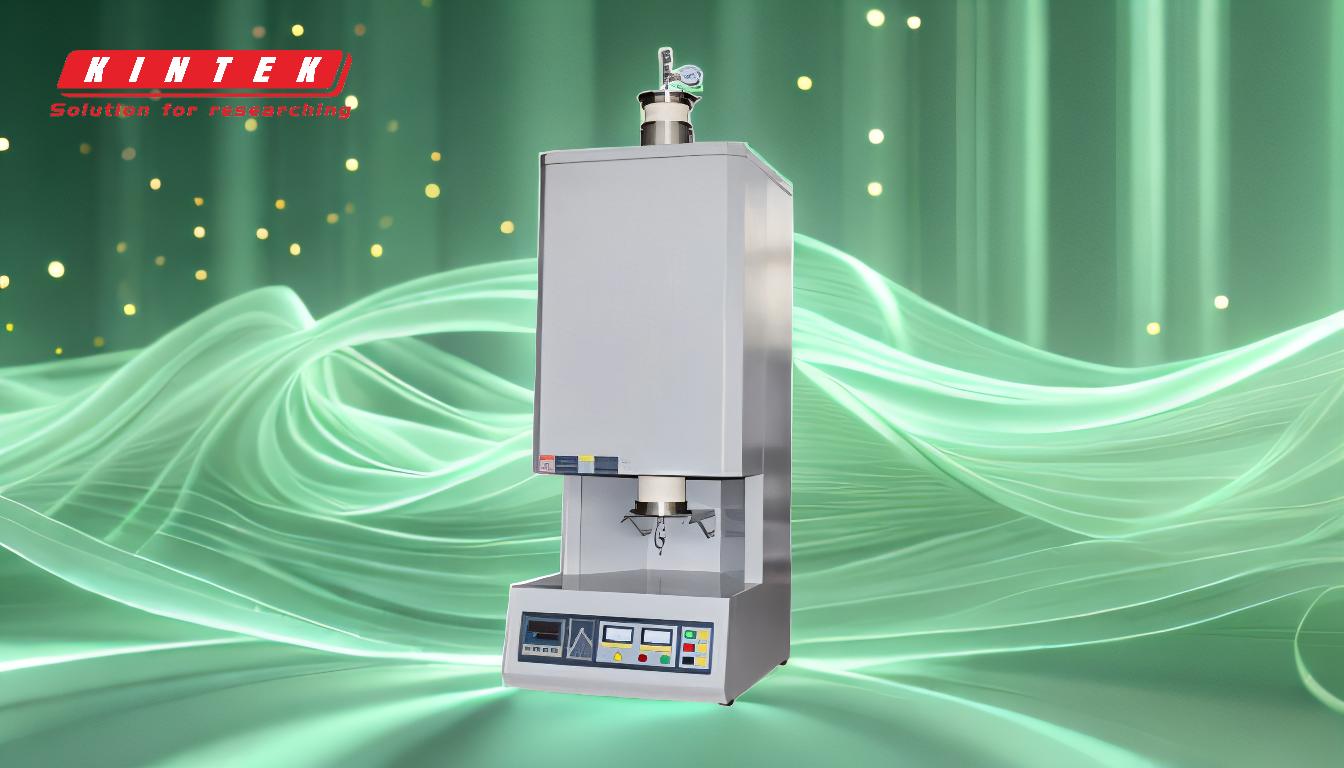
-
Definition and Purpose of an Integral Quench Furnace:
- An integral quench furnace is a type of heat treatment furnace that combines heating and quenching processes in one unit. This integration allows for seamless transition from heating to rapid cooling, which is essential for processes like hardening and tempering.
- The primary purpose of this furnace is to enhance the mechanical properties of metals, such as hardness, strength, and durability, by subjecting them to controlled heating and cooling cycles.
-
Key Components and Functionality:
- Heating Chamber: The furnace features a heating chamber where the metal is heated to a specific temperature. This chamber is designed to maintain uniform temperature distribution to ensure consistent treatment of the material.
- Quenching System: The quenching system is integrated into the furnace and is used to rapidly cool the heated metal. This rapid cooling is crucial for achieving the desired hardness and strength in the material.
- Atmosphere Control: Many integral quench furnaces are equipped with atmosphere control systems to prevent oxidation or decarburization of the metal during the heating process. This is particularly important for maintaining the quality and integrity of the treated material.
-
Applications in Various Industries:
- Automotive Industry: Integral quench furnaces are used to heat treat components like gears, shafts, and bearings, which require high hardness and wear resistance.
- Aerospace Industry: The furnace is used for treating critical components that must withstand extreme conditions, such as turbine blades and engine parts.
- Tool Manufacturing: Tools like drills, cutters, and dies are often treated in integral quench furnaces to enhance their durability and performance.
-
Advantages of Using an Integral Quench Furnace:
- Efficiency: The integration of heating and quenching processes in a single unit reduces the time and energy required for heat treatment.
- Precision: The furnace allows for precise control over temperature and cooling rates, ensuring consistent and high-quality results.
- Versatility: It can be used for a wide range of heat treatment processes, including hardening, tempering, and annealing, making it a versatile tool in metallurgical applications.
-
Comparison with Other Heat Treatment Furnaces:
- Unlike batch furnaces, which require separate quenching processes, integral quench furnaces streamline the heat treatment process by combining heating and quenching in one unit.
- Compared to continuous furnaces, integral quench furnaces offer more flexibility in terms of process control and are better suited for small to medium-sized batches.
-
Maintenance and Operational Considerations:
- Regular maintenance is essential to ensure the longevity and efficiency of the furnace. This includes checking the heating elements, quenching system, and atmosphere control systems.
- Operators must be trained to handle the furnace safely, especially during the quenching process, which involves rapid cooling and can pose safety risks if not managed properly.
In summary, an integral quench furnace is a highly efficient and versatile tool used in various industries for heat treatment processes. Its ability to combine heating and quenching in a single unit makes it an invaluable asset for achieving precise and consistent results in metal treatment.
Summary Table:
Aspect | Details |
---|---|
Definition | Combines heating and quenching in one unit for seamless heat treatment. |
Key Components | Heating chamber, quenching system, atmosphere control. |
Applications | Automotive, aerospace, tool manufacturing. |
Advantages | Efficiency, precision, versatility. |
Maintenance | Regular checks on heating elements, quenching system, and atmosphere control. |
Ready to enhance your heat treatment process? Contact us today to learn more about integral quench furnaces!