DC sputtering is a versatile and widely used technique in various industries, primarily for depositing thin films of materials onto substrates. It is particularly valued for its ability to produce uniform, high-quality coatings with precise thickness control. Applications range from creating microchip circuitry in the semiconductor industry to enhancing the durability and appearance of consumer goods like jewelry and watches. Additionally, DC sputtering is used in advanced fields such as aerospace, defense, and medical devices, where it contributes to the development of corrosion-resistant coatings, optical components, and specialized thin films. Its ability to deposit a wide range of materials, including metals, alloys, and dielectrics, makes it indispensable in modern manufacturing and research.
Key Points Explained:
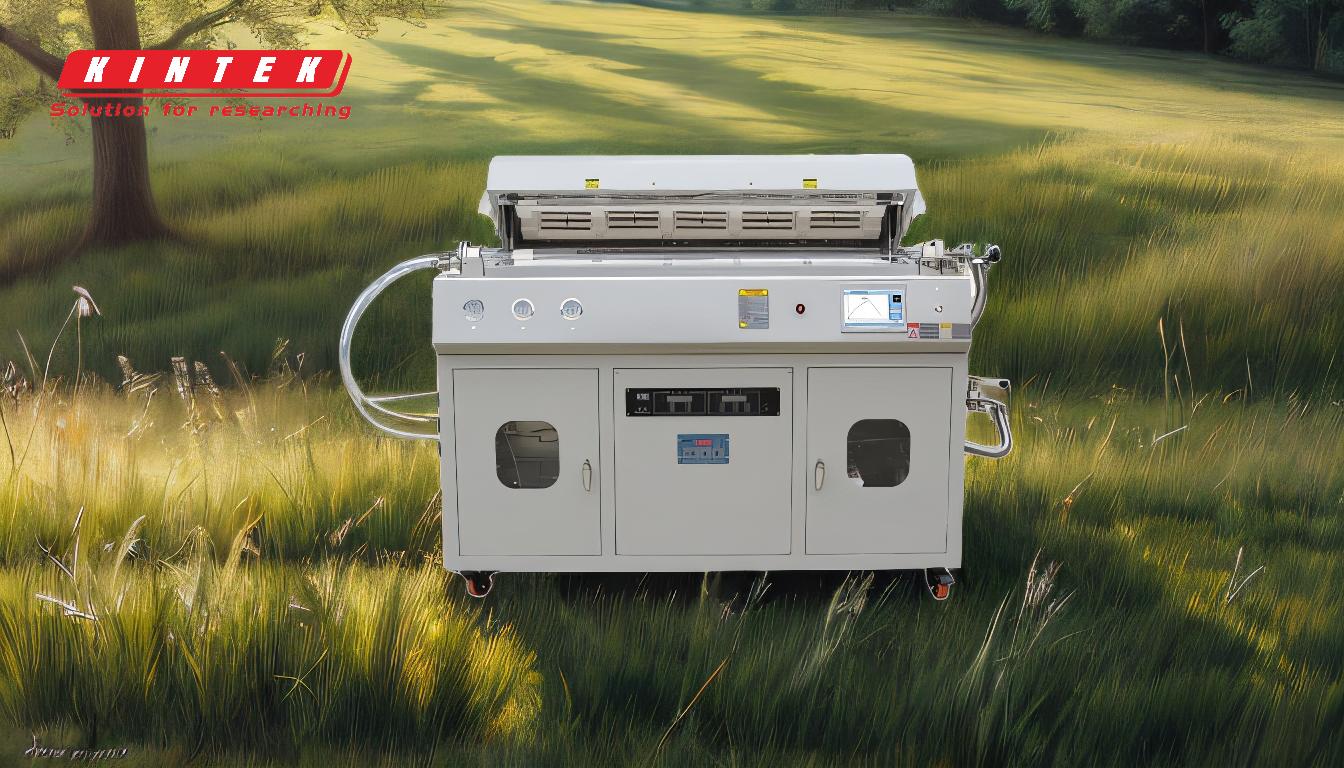
-
Semiconductor Industry:
- DC sputtering is extensively used in the semiconductor industry to create microchip circuitry on a molecular level. This process involves depositing thin films of conductive and insulating materials onto silicon wafers, which are then patterned to form the intricate circuits found in modern electronics. The precision and uniformity of DC sputtering make it ideal for this application.
-
Decorative and Functional Coatings:
- DC sputtering is employed to apply gold and other metal coatings on jewelry, watches, and decorative items, enhancing their appearance and durability. It is also used to create non-reflective coatings on glass and optical components, improving their performance in various applications.
-
Optical and Glass Coatings:
- The technique is used to deposit anti-reflective and high-emissivity films on glass, which are essential for applications like energy-efficient windows and optical lenses. These coatings help reduce glare, improve light transmission, and enhance thermal performance.
-
Packaging and Protective Films:
- DC sputtering is utilized to create gas-impermeable films on packaging plastics, protecting contents from moisture and other environmental factors. It is also used to apply corrosion-resistant coatings on metals, extending the lifespan of materials used in harsh environments.
-
Advanced Materials and Alloys:
- The process is capable of depositing thin films of advanced materials and alloys, such as molybdenum, tantalum, and niobium-based films. These materials are used in various high-tech applications, including improving the scratch resistance of shape memory alloys and creating chemically resistant coatings for industrial use.
-
Aerospace and Defense:
- In the aerospace and defense sectors, DC sputtering is used to apply specialized coatings, such as gadolinium films for neutron radiography. These coatings are critical for the development of advanced materials and components that must withstand extreme conditions.
-
Medical Devices:
- DC sputtering is employed to produce dielectric stacks that electrically isolate surgical tools, ensuring their safety and reliability. The technique is also used to create biocompatible coatings on medical implants, enhancing their performance and longevity.
-
Consumer Electronics:
- The production of computer hard disks, CDs, and DVDs relies on DC sputtering to deposit thin films of magnetic and reflective materials. These coatings are essential for data storage and retrieval, as well as for the durability and performance of optical media.
-
Energy and Lighting:
- DC sputtering is used in the energy sector to create coatings for solar panels and other energy-efficient devices. In the lighting industry, it is employed to produce high-efficiency coatings for lamps and LEDs, improving their brightness and energy consumption.
-
Research and Development:
- Researchers and engineers use DC sputtering to develop new materials and coatings with unique properties. This includes creating smaller, lighter, and more durable products, as well as advancing the field of surface physics and materials science.
In summary, DC sputtering is a critical technology with a wide range of applications across multiple industries. Its ability to deposit thin films with high precision and uniformity makes it indispensable for creating advanced materials, enhancing product performance, and driving innovation in various fields.
Summary Table:
Industry | Applications |
---|---|
Semiconductor | Microchip circuitry, conductive/insulating thin films |
Decorative Coatings | Gold and metal coatings for jewelry, watches, and decorative items |
Optical and Glass | Anti-reflective, high-emissivity films for energy-efficient windows and lenses |
Packaging | Gas-impermeable films for moisture protection |
Advanced Materials | Molybdenum, tantalum, and niobium-based films for scratch resistance |
Aerospace and Defense | Specialized coatings like gadolinium films for neutron radiography |
Medical Devices | Biocompatible coatings for implants, dielectric stacks for surgical tools |
Consumer Electronics | Magnetic and reflective films for hard disks, CDs, and DVDs |
Energy and Lighting | Coatings for solar panels, high-efficiency lamps, and LEDs |
Research and Development | Development of advanced materials and coatings with unique properties |
Unlock the potential of DC sputtering for your industry—contact our experts today to learn more!