Diamond coating refers to a thin layer of diamond material applied to the surface of various substrates to enhance their properties. These coatings leverage the exceptional characteristics of diamond, such as high hardness, excellent thermal conductivity, chemical inertness, and optical transparency. They are widely used in industrial, scientific, and technological applications, including solar cells, optical devices, biosensors, protective coatings, and precision tooling. The quality and performance of diamond coatings can be tailored by adjusting deposition parameters and gas phase composition, making them versatile for specific use cases. Their unique properties, combined with the ability to fine-tune their microstructure and morphology, enable a wide range of applications across multiple industries.
Key Points Explained:
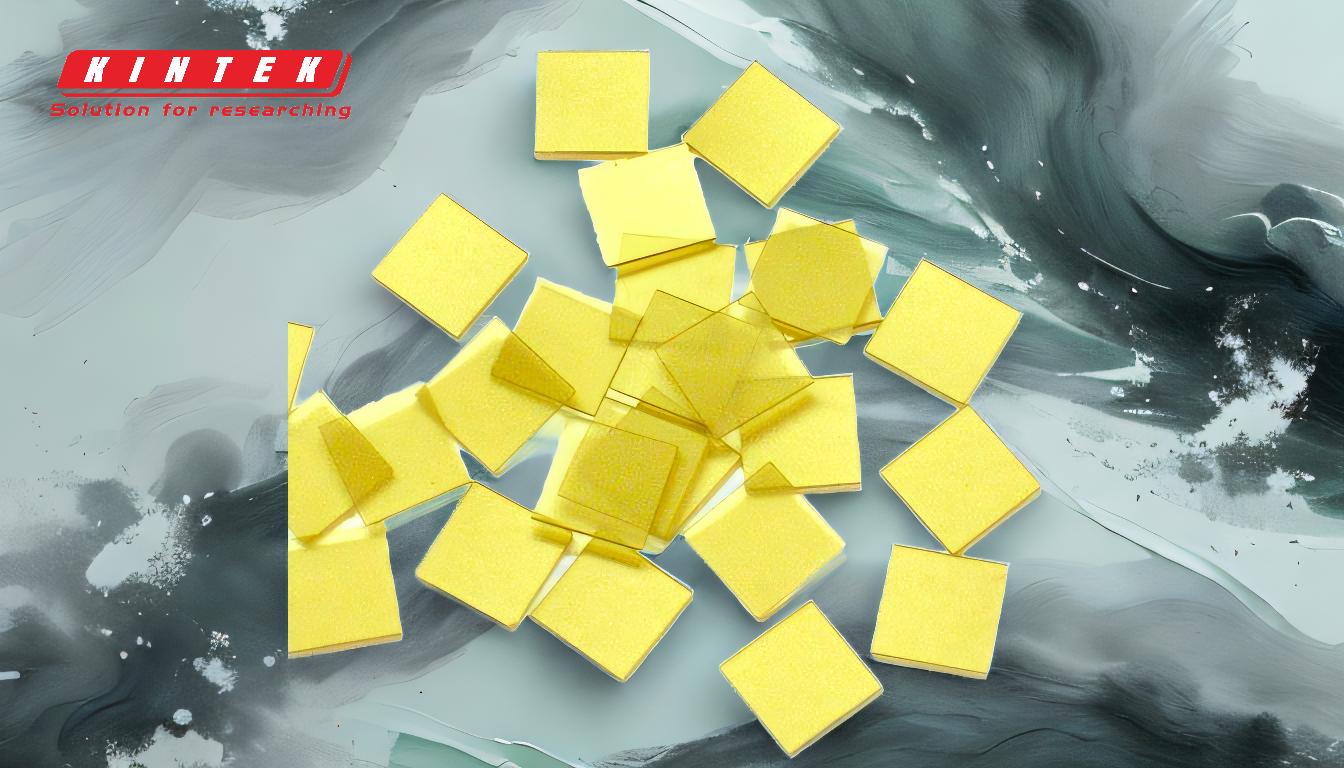
-
Definition and Composition of Diamond Coatings:
- Diamond coatings are thin films of diamond material deposited onto substrates.
- They share properties similar to bulk diamond, such as high hardness, thermal conductivity, and chemical inertness.
- These coatings can be tailored in terms of grain size, surface roughness, and crystallinity by controlling deposition parameters and gas phase composition.
-
Key Properties of Diamond Coatings:
- High Hardness: Diamond coatings are extremely hard, making them ideal for protective and wear-resistant applications.
- Excellent Thermal Conductivity: They efficiently dissipate heat, which is crucial in high-temperature environments.
- Chemical Inertness: Diamond coatings resist chemical reactions, making them suitable for harsh environments.
- Optical Transparency: Their transparency enables use in optical devices and solar cells.
- Semi-Conductivity: This property allows diamond coatings to be used in electronic and photochemical applications.
-
Applications of Diamond Coatings:
- Industrial Tools: Used as coatings on cutting tools to improve efficiency, extend tool life, and meet high-precision demands.
- Solar Cells and Optical Devices: Their transparency and semi-conductivity make them ideal for solar cells and optical components.
- Biosensors: Diamond coatings are used in biosensors due to their biocompatibility and chemical stability.
- Protective Coatings: They provide wear and corrosion resistance in harsh environments.
- Fundamental Research: Diamond thin films are used in academic studies to explore material properties and applications.
-
Customization and Tailoring:
- The microstructure, morphology, and surface properties of diamond coatings can be adjusted to meet specific application requirements.
- Deposition parameters (e.g., temperature, pressure) and gas phase composition are key factors in controlling the quality and characteristics of the coatings.
-
Advantages of Nanometer Diamond Films:
- Nanometer diamond films combine the properties of nanomaterials with those of diamond.
- They offer enhanced performance in precision tooling and modern machinery industries due to their improved hardness and wear resistance.
-
Future Potential:
- The ability to tune diamond coatings for specific applications opens up possibilities for innovation in fields such as electronics, energy, and biotechnology.
- Ongoing research aims to further optimize deposition techniques and expand the range of applications for diamond coatings.
By understanding these key points, purchasers and users of diamond coatings can make informed decisions about their suitability for specific applications and ensure optimal performance in their respective fields.
Summary Table:
Aspect | Details |
---|---|
Definition | Thin diamond films applied to substrates for enhanced properties. |
Key Properties | High hardness, thermal conductivity, chemical inertness, optical transparency, semi-conductivity. |
Applications | Industrial tools, solar cells, optical devices, biosensors, protective coatings. |
Customization | Adjustable microstructure, morphology, and surface properties. |
Future Potential | Innovations in electronics, energy, and biotechnology. |
Unlock the potential of diamond coatings for your applications—contact us today to learn more!