The die compression ratio is a critical parameter in the context of tablet manufacturing, particularly in the pharmaceutical and chemical industries. It refers to the ratio of the initial volume of the powder or granule material in the die cavity to the final volume of the compressed tablet. This ratio is essential because it influences the tablet's density, hardness, and overall quality. A higher compression ratio typically results in a denser and harder tablet, but it must be carefully controlled to avoid issues such as capping, lamination, or excessive wear on the die and punches. Understanding and optimizing the die compression ratio is vital for ensuring consistent tablet quality and efficient production processes.
Key Points Explained:
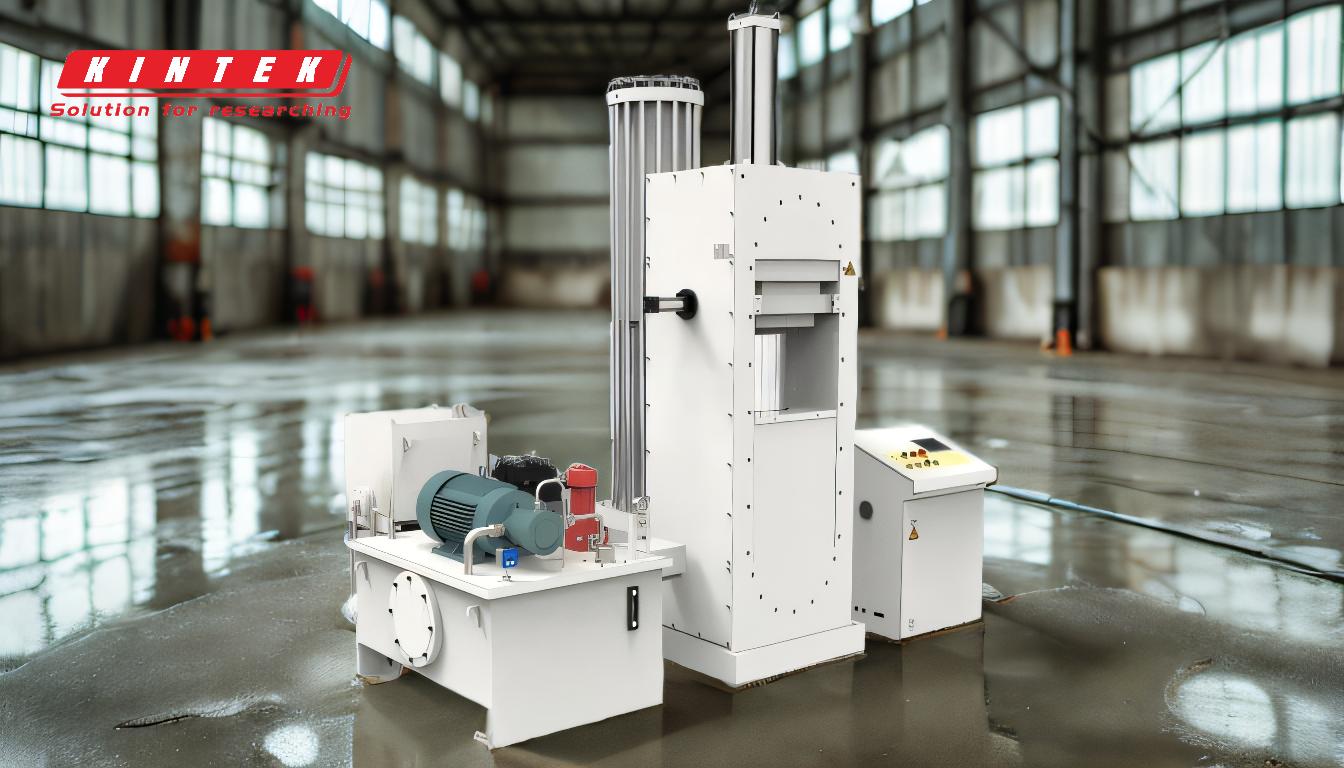
-
Definition of Die Compression Ratio:
- The die compression ratio is defined as the ratio of the initial volume of the powder or granule material in the die cavity to the final volume of the compressed tablet. Mathematically, it can be expressed as: [ \text{Compression Ratio} = \frac{\text{Initial Volume}}{\text{Final Volume}} ]
- This ratio is a measure of how much the material is compressed during the tablet manufacturing process.
-
Importance in Tablet Manufacturing:
- Tablet Density and Hardness: A higher compression ratio generally leads to a denser and harder tablet. This is because the material is compressed more, reducing the void spaces between particles.
- Tablet Quality: The compression ratio directly affects the tablet's physical properties, such as its strength, friability, and disintegration time. Proper control of the compression ratio is essential to produce tablets that meet quality standards.
- Production Efficiency: Optimizing the compression ratio can help reduce production issues such as capping (where the top of the tablet separates from the main body) or lamination (where the tablet splits into layers). It also minimizes wear and tear on the die and punches, extending their lifespan.
-
Factors Influencing Die Compression Ratio:
- Material Properties: The compressibility of the powder or granule material plays a significant role in determining the optimal compression ratio. Materials with higher compressibility can achieve higher compression ratios without causing defects.
- Die Geometry: The shape and size of the die cavity can affect how the material is compressed. For example, a larger die cavity may require a higher compression ratio to achieve the desired tablet density.
- Compression Force: The force applied during the compression process directly impacts the compression ratio. Higher compression forces can achieve higher compression ratios, but they must be carefully controlled to avoid over-compression.
-
Optimization of Die Compression Ratio:
- Trial and Error: In practice, the optimal compression ratio is often determined through trial and error, where different compression forces and die geometries are tested to achieve the desired tablet properties.
- Process Control: Advanced tablet presses often include sensors and control systems that allow for precise adjustment of the compression force, enabling more consistent control of the compression ratio.
- Quality Control: Regular testing of tablet properties, such as hardness, friability, and disintegration time, is essential to ensure that the compression ratio is optimized for consistent quality.
-
Challenges and Considerations:
- Material Variability: Variations in the raw material properties, such as particle size distribution or moisture content, can affect the compressibility and, consequently, the optimal compression ratio.
- Equipment Wear: Over time, the die and punches may wear out, leading to changes in the compression ratio. Regular maintenance and replacement of worn parts are necessary to maintain consistent tablet quality.
- Regulatory Compliance: In the pharmaceutical industry, the compression ratio must be carefully controlled to ensure that the tablets meet regulatory standards for quality and consistency.
In summary, the die compression ratio is a fundamental parameter in tablet manufacturing that influences the tablet's density, hardness, and overall quality. Understanding and optimizing this ratio is essential for producing high-quality tablets efficiently and consistently. By considering factors such as material properties, die geometry, and compression force, manufacturers can achieve the desired tablet properties while minimizing production issues and equipment wear.
Summary Table:
Aspect | Details |
---|---|
Definition | Ratio of initial powder volume to final tablet volume. |
Importance | Affects tablet density, hardness, and quality. |
Key Factors | Material properties, die geometry, and compression force. |
Optimization | Achieved through trial and error, process control, and quality testing. |
Challenges | Material variability, equipment wear, and regulatory compliance. |
Need help optimizing your tablet manufacturing process? Contact our experts today for tailored solutions!