Evaporation coating, also known as physical vapor deposition (PVD), is a process used to create thin, uniform layers of material on a substrate. This is achieved by evaporating a source material in a vacuum chamber, allowing the vapor to condense onto the target object, forming a micro-thin coating. The process is widely used across industries such as aerospace, automotive, electronics, and consumer goods, offering benefits like high temperature resistance, wear resistance, and tailored optical properties. Applications range from decorative coatings on accessories to functional layers in OLEDs, solar cells, and EMI/RFI shielding. The two primary methods are thermal evaporation and electron-beam (e-beam) evaporation, each suited for specific materials and applications.
Key Points Explained:
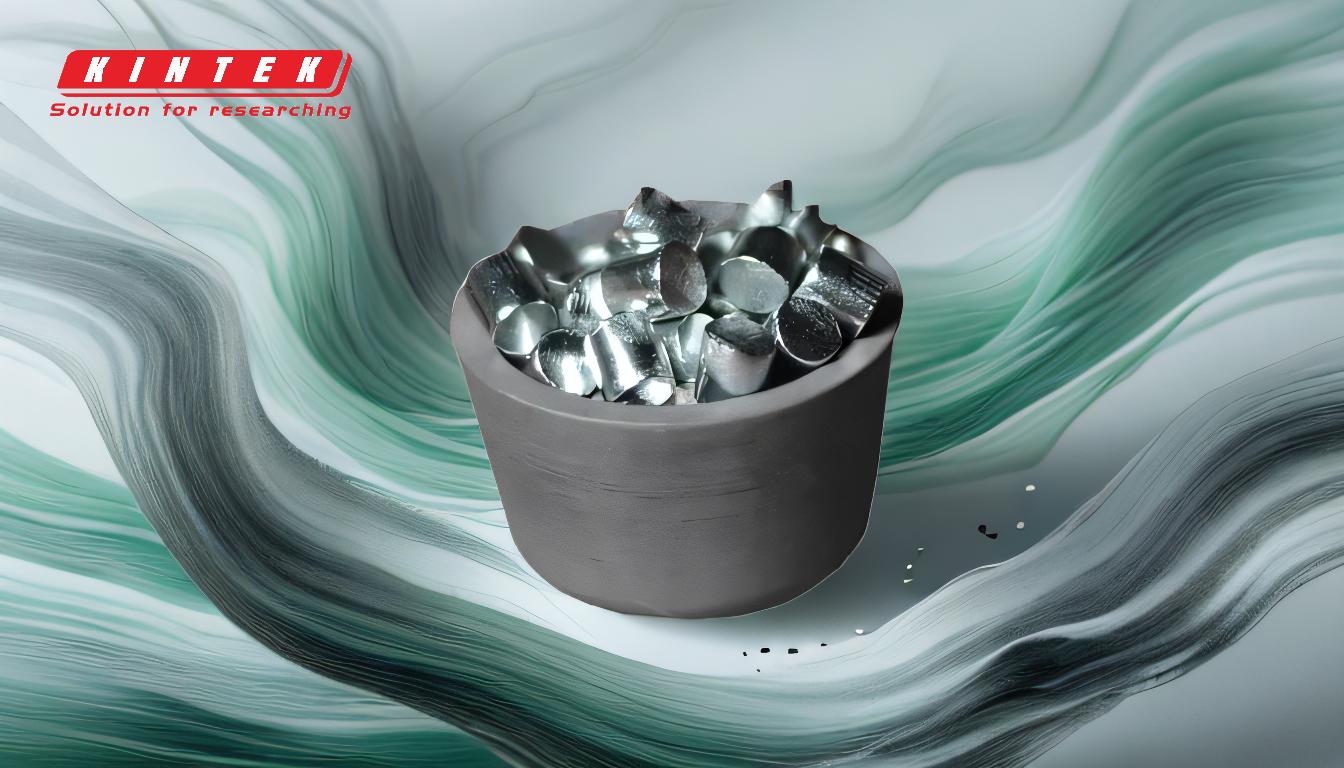
-
Definition of Evaporation Coating:
- Evaporation coating is a PVD technique where a source material is heated until it evaporates in a vacuum chamber.
- The vapor then condenses onto the target object, forming a thin, uniform layer.
- This process is used to enhance surface properties like durability, conductivity, or reflectivity.
-
Methods of Evaporation Coating:
-
Thermal Evaporation:
- Involves heating the source material using resistive heating elements.
- Commonly used for depositing single metals like silver or aluminum.
- Suitable for applications such as electrical contacts, decorative coatings, and thin-film devices.
-
E-beam Evaporation:
- Uses an electron beam to heat the source material, allowing for higher melting point materials.
- Ideal for applications requiring high temperature resistance, wear resistance, or specific optical properties.
- Used in industries like aerospace, automotive, and electronics.
-
Thermal Evaporation:
-
Applications of Evaporation Coating:
-
Decorative Applications:
- Used for coatings on cosmetic closures, sporting goods, mobile phone cases, watch cases, and glasses frames.
- Enhances aesthetic appeal and durability.
-
Thin-Film Devices:
- Essential for manufacturing OLEDs, solar cells, and microelectromechanical systems (MEMS).
- Provides precise control over layer thickness and composition.
-
Functional Coatings:
- Used for EMI/RFI shielding, light reflectors, and anti-static or soundproof enclosures.
- Applied in industries like automotive, medical, and aerospace.
-
Specialized Uses:
- Includes metal bonding layers in OLEDs and thin-film transistors, as well as coatings on polymers for food packaging and insulation.
- Also used in protective gear like NASA spacesuits and firefighter uniforms.
-
Decorative Applications:
-
Advantages of Evaporation Coating:
-
High Precision:
- Allows for the deposition of ultra-thin, uniform layers with precise control over thickness and composition.
-
Versatility:
- Suitable for a wide range of materials, including metals, alloys, and ceramics.
-
Enhanced Properties:
- Improves surface properties like wear resistance, chemical resistance, and optical performance.
-
Scalability:
- Can be scaled for both small-scale laboratory use and large-scale industrial production.
-
High Precision:
-
Industries Utilizing Evaporation Coating:
-
Aerospace:
- Used for coatings that provide high temperature resistance and durability.
-
Automotive:
- Applied in light reflectors, EMI/RFI shielding, and decorative components.
-
Electronics:
- Essential for creating thin-film devices like OLEDs and solar cells.
-
Consumer Goods:
- Enhances the appearance and durability of accessories like watches and phone cases.
-
Energy:
- Used in solar cells and other energy-related applications.
-
Medical:
- Applied in protective gear and medical devices requiring specific surface properties.
-
Aerospace:
-
Process Considerations:
-
Vacuum Environment:
- Ensures minimal contamination and allows for precise control over the deposition process.
-
Material Selection:
- The choice of source material depends on the desired properties of the final coating.
-
Temperature Control:
- Critical for achieving the desired evaporation rate and coating quality.
-
Substrate Preparation:
- Proper cleaning and surface treatment are essential for optimal adhesion and coating performance.
-
Vacuum Environment:
In summary, evaporation coating is a versatile and precise PVD technique used across various industries to enhance the properties of surfaces. Whether for decorative, functional, or specialized applications, it offers significant advantages in terms of precision, versatility, and performance.
Summary Table:
Aspect | Details |
---|---|
Definition | A PVD technique to create thin, uniform layers by evaporating source material. |
Methods | Thermal Evaporation, E-beam Evaporation |
Applications | Decorative coatings, OLEDs, solar cells, EMI/RFI shielding, protective gear |
Advantages | High precision, versatility, enhanced surface properties, scalability |
Industries | Aerospace, automotive, electronics, consumer goods, energy, medical |
Process Considerations | Vacuum environment, material selection, temperature control, substrate prep |
Ready to enhance your product's surface properties? Contact us today to learn more about evaporation coating solutions!