A furnace tray is an essential component used in various types of furnaces, such as muffle furnaces, industrial furnaces, or laboratory furnaces. It serves as a platform or support structure for holding materials, samples, or workpieces during heating, cooling, or processing. The tray is designed to withstand high temperatures and often plays a critical role in ensuring even heat distribution and efficient operation of the furnace. Furnace trays are typically made from materials that can endure extreme thermal conditions, such as stainless steel, ceramic, or refractory metals, depending on the specific application and temperature requirements.
Key Points Explained:
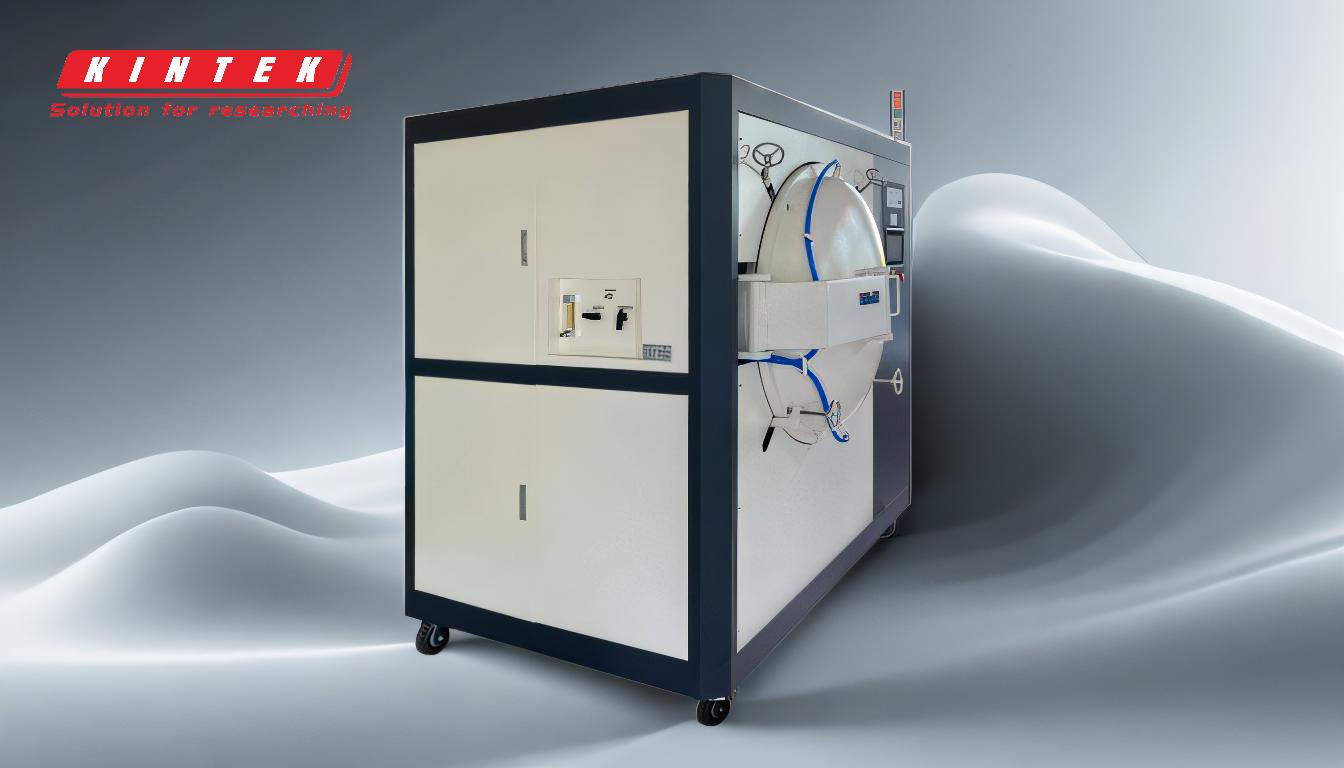
-
Purpose of a Furnace Tray:
- A furnace tray is primarily used to hold materials or samples inside the furnace during heating or processing.
- It ensures that the materials are evenly exposed to heat, which is crucial for achieving consistent results in processes like annealing, sintering, or heat treatment.
-
Materials Used in Furnace Trays:
- Furnace trays are constructed from materials that can withstand high temperatures and resist thermal degradation.
- Common materials include:
- Stainless Steel: Offers durability and resistance to oxidation, making it suitable for moderate-temperature applications.
- Ceramic: Ideal for high-temperature environments due to its excellent thermal stability and resistance to thermal shock.
- Refractory Metals: Such as tungsten or molybdenum, used in extreme high-temperature applications.
-
Design and Structure:
- Furnace trays are designed to fit seamlessly within the furnace chamber, ensuring efficient heat transfer and minimal heat loss.
- They often feature perforations or slots to allow for better airflow and heat circulation, which is particularly important in processes requiring uniform heating.
-
Compatibility with Furnace Types:
- Furnace trays are tailored to specific furnace types, such as muffle furnaces, box furnaces, or tube furnaces.
- The design and dimensions of the tray are matched to the furnace's internal structure to optimize performance.
-
Role in Heat Distribution:
- The tray plays a critical role in distributing heat evenly across the materials placed on it.
- Uneven heat distribution can lead to inconsistent results, making the tray's design and material choice vital for achieving desired outcomes.
-
Maintenance and Durability:
- Furnace trays are subject to wear and tear due to repeated exposure to high temperatures and thermal cycling.
- Regular inspection and maintenance are necessary to ensure their longevity and performance.
- In some cases, trays may need to be replaced periodically to maintain furnace efficiency.
-
Applications of Furnace Trays:
- Furnace trays are used in a wide range of industries and applications, including:
- Laboratory Research: For heating samples in controlled environments.
- Industrial Manufacturing: For processes like heat treatment, sintering, or annealing of metals and ceramics.
- Material Testing: To evaluate the thermal properties of materials under high-temperature conditions.
- Furnace trays are used in a wide range of industries and applications, including:
By understanding the role, materials, and design of furnace trays, users can make informed decisions when selecting or maintaining these components for their specific furnace applications.
Summary Table:
Key Aspect | Details |
---|---|
Purpose | Holds materials/samples during heating; ensures even heat distribution. |
Materials | Stainless steel, ceramic, refractory metals (e.g., tungsten, molybdenum). |
Design | Fits furnace chamber; perforations for airflow; ensures efficient heating. |
Compatibility | Tailored for muffle, box, or tube furnaces. |
Heat Distribution | Critical for uniform heating and consistent results. |
Maintenance | Requires regular inspection; may need periodic replacement. |
Applications | Laboratory research, industrial manufacturing, material testing. |
Need help selecting or maintaining furnace trays? Contact our experts today for tailored solutions!