Heat treatment is a controlled process used to alter the physical and sometimes chemical properties of metallic materials by heating and cooling them under specific conditions. This process is essential in industries like aerospace, automotive, and manufacturing, as it enhances properties such as strength, ductility, hardness, and temperature resistance. Heat treatment techniques vary depending on the desired outcome, and they can be applied to both ferrous and non-ferrous metals. Common methods include annealing, tempering, and quenching, each tailored to achieve specific material characteristics. The process ensures a balance between cost and quality, making it a cornerstone of modern metallurgy.
Key Points Explained:
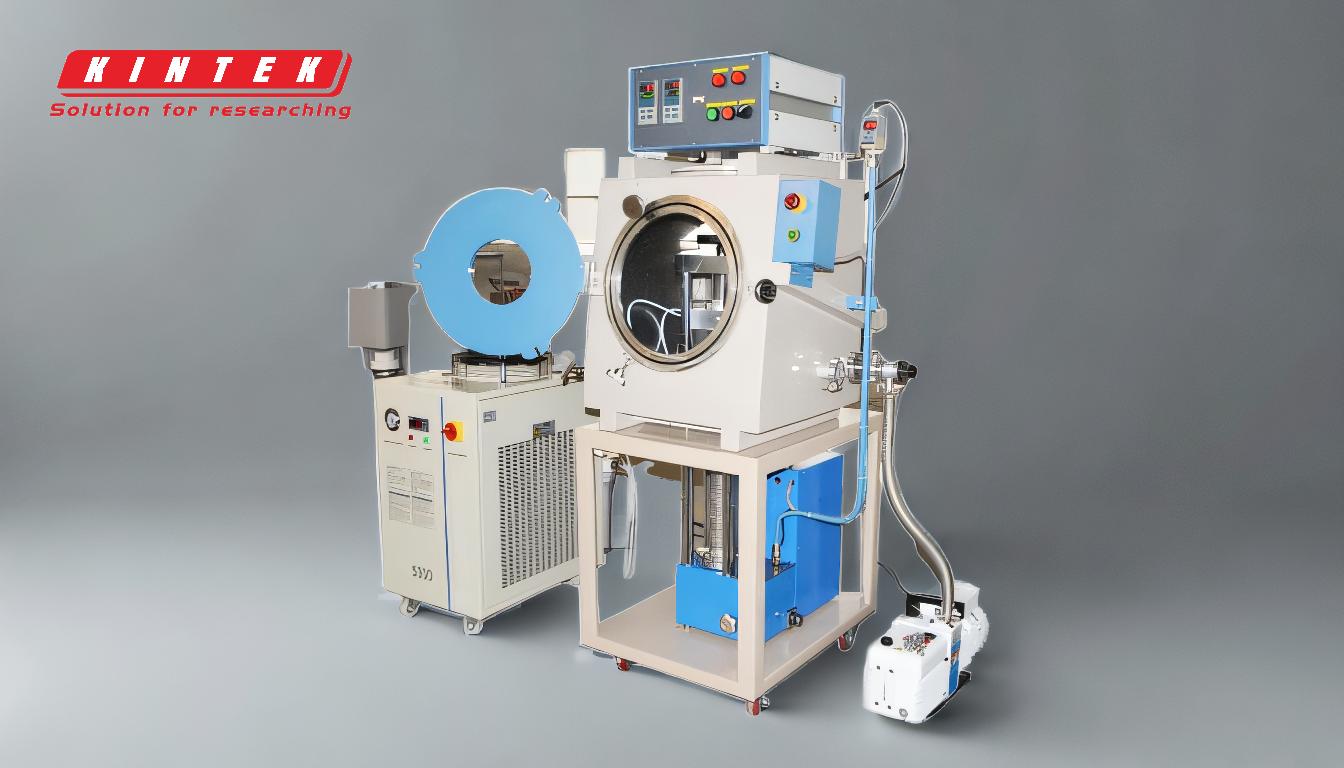
-
Definition and Purpose of Heat Treatment:
- Heat treatment involves heating and cooling metals under controlled conditions to alter their physical and mechanical properties.
- The primary goals are to improve strength, ductility, hardness, and resistance to wear, corrosion, and temperature extremes.
- It is a critical process in industries such as aerospace, automotive, and manufacturing, where material performance is paramount.
-
Types of Heat Treatment Processes:
-
Annealing: This process involves heating the metal above its critical temperature and then slowly cooling it to refine the grain structure, reduce hardness, and improve ductility. Types of annealing include:
- Supercritical or Full Annealing: Heating above the upper critical temperature (Ac3) followed by slow cooling.
- Intercritical Annealing: Heating above the final transformation temperature (Ac1) and either slow cooling or holding below the lower critical temperature.
- Subcritical Annealing: Heating just below the Ac1 point followed by slow cooling.
- Tempering: Used after hardening, tempering involves reheating the metal to a lower temperature to reduce brittleness and increase toughness and ductility.
- Quenching: Rapid cooling of the metal from a high temperature to lock in a hardened structure, often followed by tempering to balance hardness and toughness.
-
Annealing: This process involves heating the metal above its critical temperature and then slowly cooling it to refine the grain structure, reduce hardness, and improve ductility. Types of annealing include:
-
Applications of Heat Treatment:
- Heat treatment is widely used in the production of aircraft and automotive components, where high strength and durability are required.
- It is also applied in the manufacturing of batch metal parts, ensuring consistency and quality across large-scale production.
-
Role of Atmosphere Control in Heat Treatment:
- The use of a vacuum or controlled atmosphere during heat treatment can enhance the process by removing air and preventing oxidation or contamination.
- This is particularly useful when specific gaseous mediums are required to achieve desired surface finishes or material properties.
-
Heat Treatment and Material Properties:
- Heat treatment can significantly improve the physical properties of metals, making them suitable for demanding industrial applications.
- For example, it can increase the hardness of steel for cutting tools or enhance the ductility of aluminum for aerospace components.
-
Heat Treatment Equipment:
- Various types of equipment are used in heat treatment, such as furnaces, ovens, and heat press machines. These include:
- Thermostatic Heat Press: Maintains a constant temperature during the process.
- Pulse Heat Press: Uses intermittent heating for precise control.
- Duplex Heat Press: Allows for simultaneous processing of multiple parts.
- Swing Away Heat Press: Provides flexibility in handling large or complex components.
- Various types of equipment are used in heat treatment, such as furnaces, ovens, and heat press machines. These include:
-
Importance of Heat Treatment in Modern Industry:
- Heat treatment ensures that metals meet the stringent requirements of modern applications, balancing cost and quality.
- It plays a vital role in extending the lifespan and performance of metal components, reducing the need for frequent replacements and maintenance.
By understanding the principles and techniques of heat treatment, manufacturers can optimize the properties of metallic materials, ensuring they meet the demands of various industrial applications.
Summary Table:
Aspect | Details |
---|---|
Definition | Controlled heating and cooling to alter physical and chemical properties. |
Key Goals | Improve strength, ductility, hardness, and resistance to wear and corrosion. |
Common Methods | Annealing, tempering, quenching. |
Applications | Aerospace, automotive, and manufacturing industries. |
Equipment Used | Furnaces, ovens, heat press machines. |
Importance | Balances cost and quality, extends lifespan of metal components. |
Optimize your metallic materials with expert heat treatment solutions—contact us today!