Hot Isostatic Pressing (HIP) is a manufacturing process used to improve the properties of materials by applying high temperature and pressure uniformly from all directions. This technique is widely utilized across various industries for purposes such as eliminating microshrinkage in castings, consolidating powders, and diffusion bonding. HIP is particularly valuable in the production of high-performance components for aerospace, automotive, medical, and energy sectors. It is also essential in the manufacturing of advanced ceramics, lithium-ion batteries, and fuel cells, among other applications. The process enhances material density, strength, and reliability, making it indispensable for industries requiring high-quality and durable materials.
Key Points Explained:
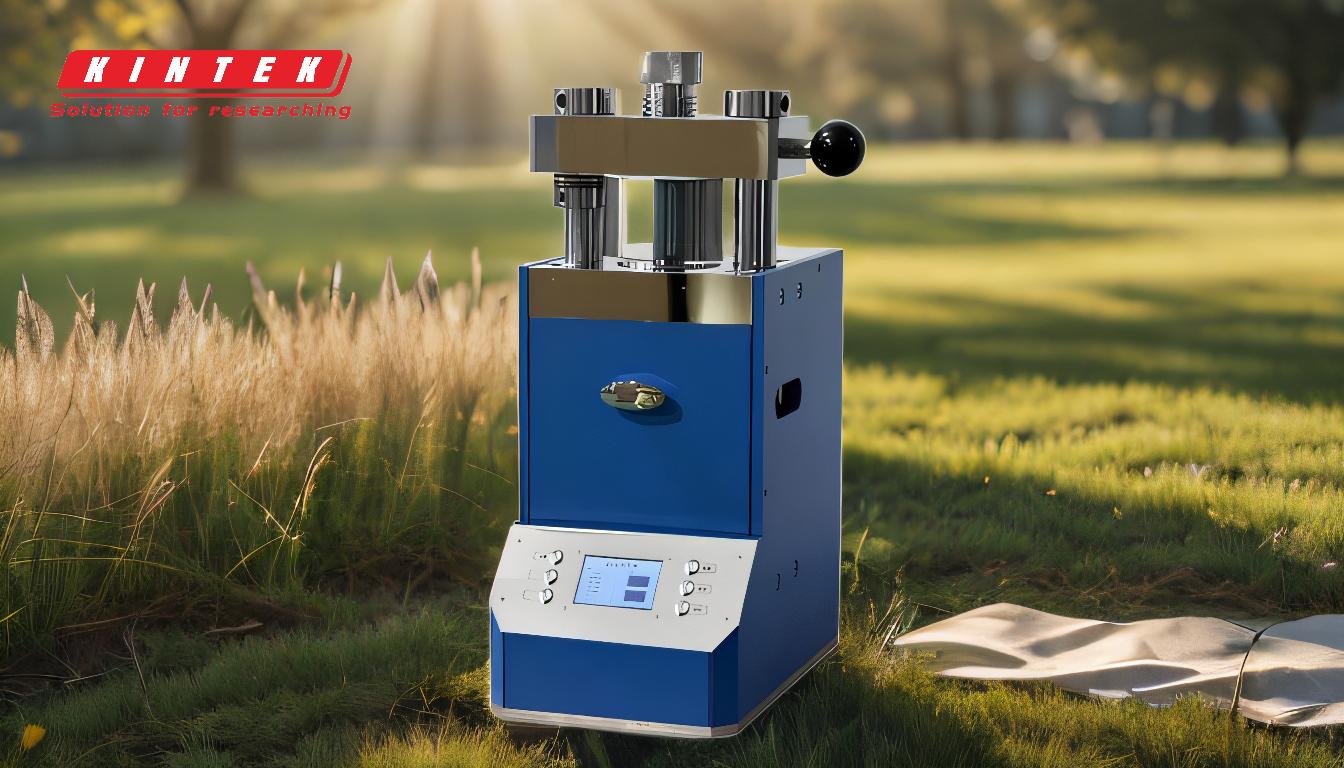
-
Elimination of Microshrinkage in Castings:
- HIP is extensively used to eliminate microshrinkage and internal porosity in castings. This is crucial for improving the mechanical properties and reliability of components, especially in industries like aerospace and automotive where failure is not an option. The process involves subjecting the material to high temperatures and pressures, which helps in closing voids and enhancing material density.
-
Consolidation of Powders:
- HIP is employed to consolidate powders into solid materials. This is particularly useful in the production of advanced ceramics, metals, and composites. The uniform pressure and temperature ensure that the powders are fully densified, resulting in materials with superior strength and performance. This application is vital in industries such as electronics, where high-performance materials are required.
-
Diffusion Bonding (Cladding):
- Diffusion bonding, often referred to as cladding, is another key application of HIP. This process involves joining two or more materials without the use of adhesives or solder. The high temperature and pressure facilitate atomic diffusion across the material interfaces, creating strong and durable bonds. This technique is widely used in the manufacturing of medical devices and high-performance components for the oil and gas industry.
-
Applications in Advanced Ceramics:
- HIP is an excellent forming process for high-performance ceramics such as zirconia and alumina. These materials are used in applications requiring high strength, wear resistance, and thermal stability. The process ensures that the ceramics are fully densified, enhancing their mechanical properties and making them suitable for use in harsh environments.
-
Energy Storage Technologies:
- HIP plays a crucial role in the production of energy storage technologies, including lithium-ion batteries and fuel cells. The process helps in consolidating electrode materials and improving their density, which in turn enhances the performance and longevity of the batteries. This is particularly important in the development of efficient and reliable energy storage solutions for various applications.
-
Medical and Electronics Industries:
- In the medical industry, HIP is used to manufacture high-strength and biocompatible materials for implants and prosthetics. In the electronics industry, it is employed to produce components with high precision and reliability. The uniform pressure and temperature ensure that the materials are free from defects, making them suitable for critical applications.
-
Production of New Alloy Products:
- HIP technology is used to produce new alloy products that are difficult to manufacture using traditional casting methods. The process allows for the creation of complex shapes and structures with enhanced material properties. This is particularly beneficial in industries such as aerospace and automotive, where advanced materials are required to meet stringent performance criteria.
-
Warm Isostatic Press:
- A warm isostatic press is a specialized type of HIP equipment used for compression and static heating in processing and manufacturing. It is particularly useful in the production of lithium batteries, where it helps in consolidating electrode materials and improving their performance. The warm isostatic press operates at lower temperatures compared to traditional HIP, making it suitable for materials that are sensitive to high heat.
In summary, Hot Isostatic Pressing (HIP) is a versatile and essential process used across various industries to enhance material properties and produce high-performance components. Its applications range from eliminating defects in castings to consolidating powders and bonding materials, making it a critical technology in modern manufacturing.
Summary Table:
Application | Key Benefit |
---|---|
Elimination of Microshrinkage | Improves material density and reliability in castings |
Consolidation of Powders | Produces fully densified materials for advanced ceramics and composites |
Diffusion Bonding (Cladding) | Creates strong, durable bonds without adhesives or solder |
Advanced Ceramics | Enhances strength, wear resistance, and thermal stability |
Energy Storage Technologies | Improves density and performance of lithium-ion batteries and fuel cells |
Medical and Electronics | Manufactures high-strength, biocompatible materials and precision components |
New Alloy Products | Enables production of complex shapes with enhanced material properties |
Warm Isostatic Press | Consolidates electrode materials for lithium batteries at lower temperatures |
Interested in how HIP can benefit your industry? Contact us today to learn more!