Isostatic pressing is a versatile manufacturing process used across multiple industries to enhance material properties and produce high-performance components. It involves applying uniform pressure from all directions to materials, which reduces porosity, increases density, and improves mechanical properties. This process is widely used for powder consolidation, defect healing in castings, and creating advanced materials for industries such as aerospace, automotive, medical, energy, and electronics. It is particularly valuable for producing complex shapes, high-strength ceramics, and alloys that are difficult to manufacture using traditional methods. Additionally, it plays a critical role in energy storage technologies like lithium-ion batteries and fuel cells, as well as in the production of pharmaceuticals, explosives, and nuclear fuel.
Key Points Explained:
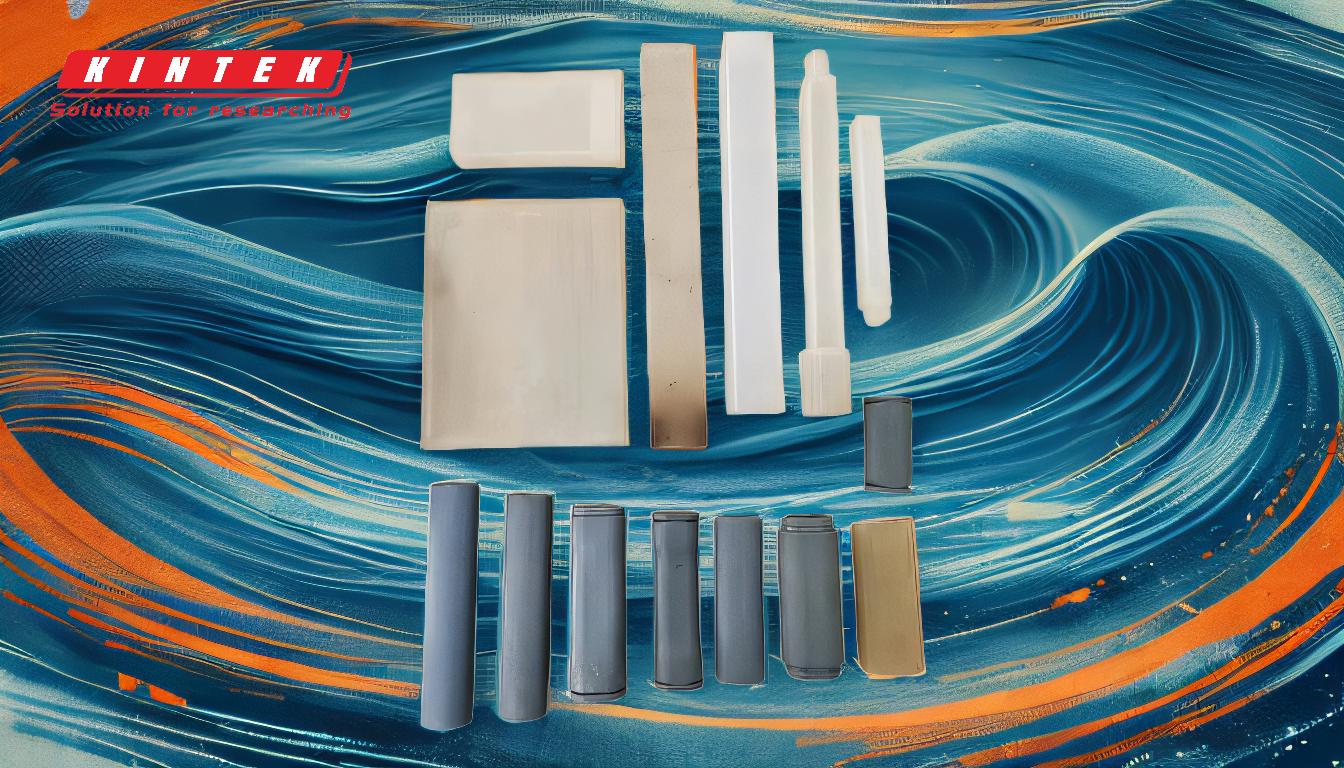
-
Definition and Purpose of Isostatic Pressing:
- Isostatic pressing is a manufacturing process that applies uniform pressure from all directions to materials, such as metals, ceramics, composites, and plastics.
- The primary purpose is to reduce porosity, increase density, and improve mechanical properties like strength, durability, and workability.
- It is used for both powder consolidation (forming solid materials from powders) and defect healing (repairing imperfections in castings).
-
Applications Across Industries:
- Aerospace and Defense: Used to manufacture high-performance components that require exceptional strength and durability, such as turbine blades and structural parts.
- Automotive: Enhances the density and performance of materials used in engine components, transmission systems, and lightweight structural parts.
- Medical: Produces biocompatible materials for implants, prosthetics, and surgical tools with precise shapes and high strength.
- Energy and Power: Applied in the production of lithium-ion batteries, fuel cells, and components for the oil and gas industry.
- Electronics and Semiconductors: Used to create electrical connectors, insulators, and other high-performance electronic components.
- Pharmaceuticals and Chemicals: Enables the production of uniform and dense materials for drug delivery systems and chemical processing equipment.
- Nuclear Fuel: Used to manufacture dense and stable nuclear fuel pellets.
-
Material Types Processed:
- Metals: Enhances the density and mechanical properties of metals, making them suitable for high-stress applications.
- Ceramics: Produces advanced ceramics with high strength and precision, such as zirconia and alumina ceramics.
- Composites: Combines different materials to create components with tailored properties for specific applications.
- Plastics and Carbon: Used to produce high-performance plastic and carbon-based materials for specialized uses.
-
Benefits of Isostatic Pressing:
- Improved Material Properties: Reduces porosity and increases density, leading to better mechanical performance.
- Complex Shape Formation: Allows for the creation of intricate and complex shapes that are difficult to achieve with traditional manufacturing methods.
- Cost Efficiency: Lowers tooling costs and reduces material waste, making it a cost-effective solution for high-performance components.
- Versatility: Suitable for a wide range of materials and industries, offering tailored solutions for specific requirements.
-
Role in Advanced Technologies:
- Energy Storage: Plays a critical role in the production of lithium-ion batteries and fuel cells, which are essential for renewable energy and electric vehicles.
- Additive Manufacturing (3D Printing): Enhances the properties of 3D-printed parts by reducing porosity and improving density, making them suitable for demanding applications.
- New Alloy Development: Enables the creation of advanced alloys that are difficult to produce using traditional casting methods.
-
Specific Applications:
- Waste Form Classes: Used to produce stable and dense waste forms for nuclear and hazardous waste management.
- Explosives and Ferrites: Ensures uniform density and performance in explosive materials and magnetic ferrites.
- Food Industry: Applied in the production of dense and uniform food products with enhanced shelf life and quality.
In summary, isostatic pressing is a critical process for enhancing material properties and producing high-performance components across a wide range of industries. Its ability to reduce porosity, increase density, and create complex shapes makes it indispensable in fields such as aerospace, automotive, medical, energy, and electronics.
Summary Table:
Aspect | Key Details |
---|---|
Definition | Uniform pressure applied from all directions to reduce porosity and increase density. |
Applications | Aerospace, automotive, medical, energy, electronics, pharmaceuticals, and more. |
Materials Processed | Metals, ceramics, composites, plastics, and carbon-based materials. |
Benefits | Improved mechanical properties, complex shape formation, cost efficiency, versatility. |
Advanced Technologies | Energy storage (batteries, fuel cells), additive manufacturing, new alloy development. |
Ready to enhance your materials with isostatic pressing? Contact us today to learn more!