Physical vapor deposition (PVD) on plastic is a process that involves depositing thin, durable, and functional coatings onto plastic substrates. This technique is widely used to enhance the properties of plastics, such as improving scratch resistance, electrical and thermal conductivity, and corrosion resistance. PVD involves converting a solid target material into a vapor phase in a low-pressure chamber, which then deposits onto the plastic substrate, forming a strong and durable coating. This method is particularly valuable in industries requiring decorative and functional finishes on plastic components.
Key Points Explained:
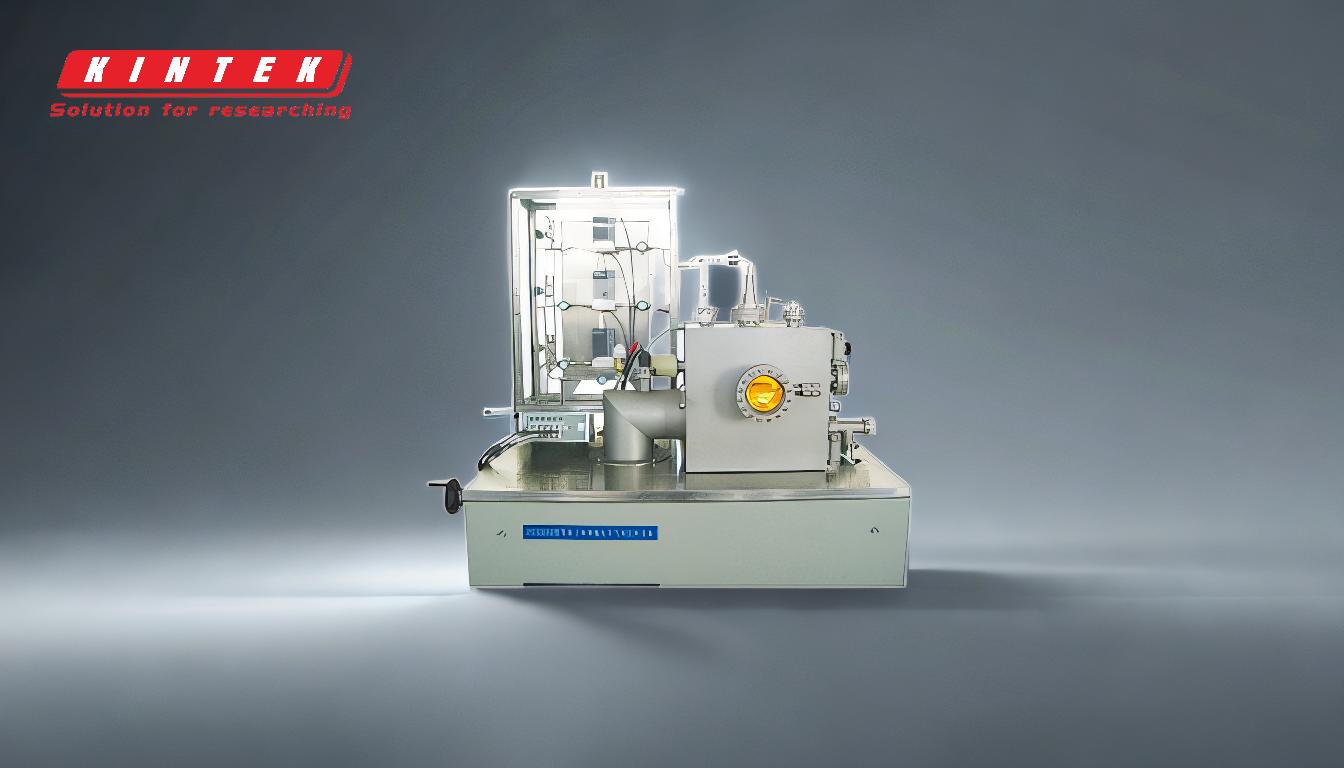
-
Definition and Purpose of PVD on Plastic:
- Physical vapor deposition (PVD) is a process where a solid material is vaporized in a vacuum and then deposited onto a substrate, such as plastic, to create a thin, durable coating.
- The primary purpose of PVD on plastic is to enhance its functional and decorative properties. This includes improving scratch resistance, electrical and thermal conductivity, and providing a barrier against corrosion and high temperatures.
-
Process of PVD:
- The PVD process begins with the solid target material being converted into a vapor phase. This is typically achieved through methods such as sputtering, evaporation, or ion plating.
- The vaporized material then travels through a low-pressure chamber and deposits onto the plastic substrate, forming a thin film.
- The resulting coating is highly durable and can withstand exposure to harsh environments, making it suitable for various industrial applications.
-
Advantages of PVD on Plastic:
- Durability: PVD coatings are known for their hardness and resistance to wear, making them ideal for applications where the plastic component is subject to mechanical stress.
- Corrosion Resistance: The coatings provide a protective barrier that prevents corrosion, extending the lifespan of the plastic part.
- Aesthetic Appeal: PVD can be used to create decorative finishes with a wide range of colors and textures, enhancing the visual appeal of plastic products.
- Improved Conductivity: By depositing conductive materials, PVD can improve the electrical and thermal conductivity of non-conductive plastics, expanding their use in electronic applications.
-
Comparison with Chemical Vapor Deposition (CVD):
- While both PVD and CVD are used to deposit thin films, they differ in their processes. CVD involves injecting a volatile precursor into a chamber, which reacts or decomposes to form the coating. In contrast, PVD involves the physical vaporization of a solid material.
- PVD is generally preferred for plastic substrates because it operates at lower temperatures, reducing the risk of thermal damage to the plastic.
-
Applications of PVD on Plastic:
- Automotive Industry: PVD coatings are used on plastic components to improve their durability and resistance to environmental factors.
- Electronics: Conductive PVD coatings on plastics are used in electronic devices to enhance performance and reliability.
- Consumer Goods: Decorative PVD coatings are applied to plastic products such as watches, jewelry, and household items to improve their aesthetic appeal and durability.
-
Evolution of PVD Technology:
- PVD has been in use for over 100 years, but significant advancements have been made in the last 30 years with the development of plasma-assisted PVD (PAPVD).
- PAPVD technologies, such as direct current (DC) diode, radio-frequency (RF), and ion beam-assisted coatings, have expanded the capabilities and applications of PVD, making it a versatile and effective method for coating plastics.
In summary, physical vapor deposition on plastic is a versatile and effective method for enhancing the properties of plastic materials. By providing durable, functional, and decorative coatings, PVD enables the use of plastics in a wide range of demanding applications across various industries.
Summary Table:
Aspect | Details |
---|---|
Definition | Process of depositing thin, durable coatings on plastic substrates. |
Purpose | Enhances functional and decorative properties of plastics. |
Process | Solid material vaporized in a vacuum and deposited onto plastic. |
Advantages | Durability, corrosion resistance, aesthetic appeal, improved conductivity. |
Applications | Automotive, electronics, consumer goods. |
Comparison with CVD | PVD operates at lower temperatures, reducing thermal damage to plastics. |
Evolution | Advanced PAPVD technologies expand PVD capabilities. |
Discover how PVD coatings can transform your plastic components—contact our experts today!