Pulse Plasma Sintering (PPS) is an advanced sintering technique that utilizes pulsed high electric current discharges to heat and sinter powdered materials while simultaneously applying pressure. This method involves placing the material in a graphite die between two graphite punches, where a capacitor charged to a high voltage generates current pulses to heat the material. PPS is known for its rapid heating and cooling rates, short holding times, and the ability to achieve densification at lower temperatures compared to conventional sintering methods. This makes it particularly effective for creating high-density materials with enhanced mechanical properties.
Key Points Explained:
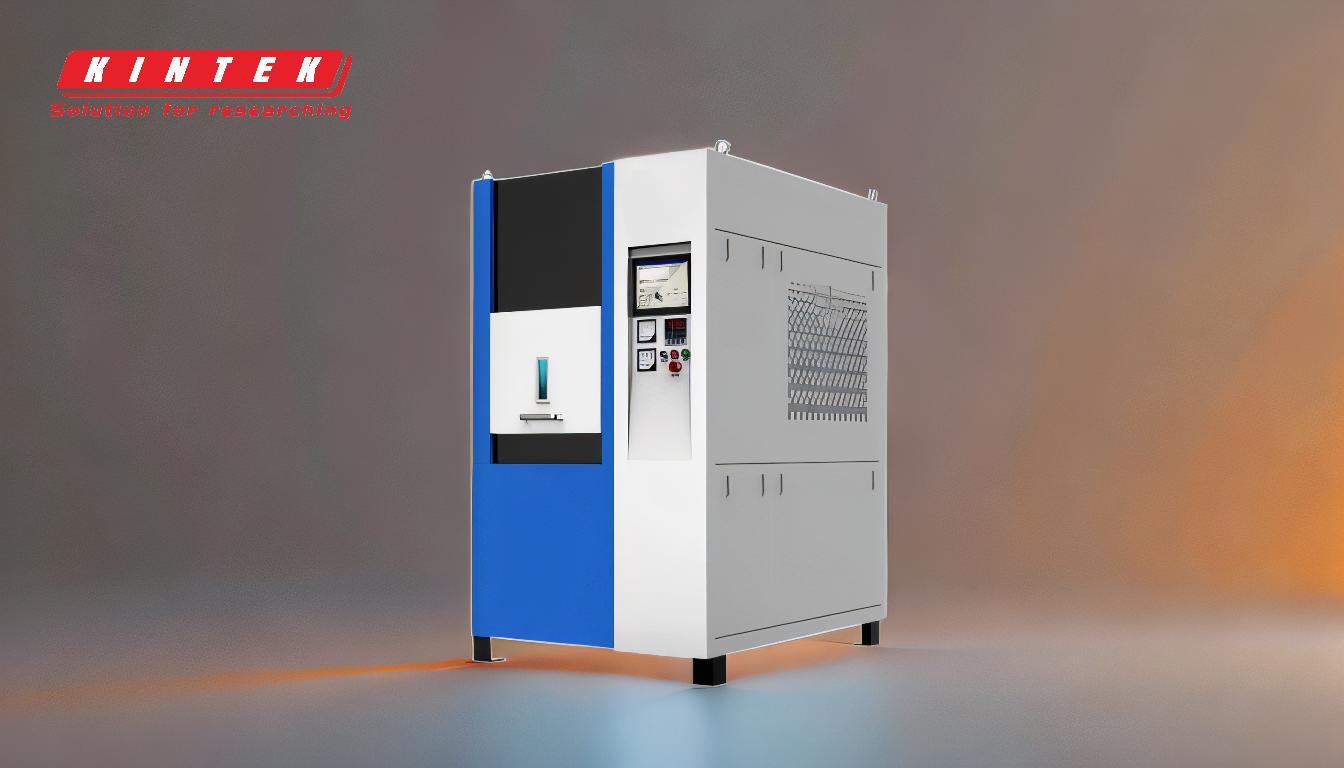
-
Mechanism of Pulse Plasma Sintering (PPS):
- PPS uses pulsed high electric current discharges to heat the powdered material while it is being pressed.
- The current pulses are generated by discharging a capacitor charged to a high voltage (up to 10 kV).
- The material is placed in a graphite die between two graphite punches, which act as both the pressure application tool and the heating source.
-
Advantages of PPS:
- Rapid Heating and Cooling Rates: PPS allows for very fast heating and cooling, which helps in achieving dense materials in a short time.
- Lower Sintering Temperatures: The process can achieve densification at temperatures several hundred degrees lower than conventional sintering methods.
- Short Holding Times: The quick process reduces the time the material is exposed to high temperatures, minimizing grain growth and preserving material properties.
-
Comparison with Other Sintering Methods:
- Conventional Sintering: Involves heating the powder compact without external pressure, typically requiring longer times and higher temperatures.
- Spark Plasma Sintering (SPS): Similar to PPS, SPS uses an electric current and pressure but is often confused with plasma generation, which is not actually present.
- Microwave Sintering: Uses microwave energy for heating, suitable for ceramics but may not be as effective for metals.
- Hot Isostatic Pressing (HIP): Applies high pressure and temperature uniformly from all directions, but is generally slower and more expensive.
-
Applications of PPS:
- Ceramics and Metals: PPS is particularly effective for sintering ceramics and metallic powders, producing materials with high density and excellent mechanical properties.
- Complex Shapes: The method can be used to create complex three-dimensional shapes with high precision.
- Advanced Materials: PPS is suitable for advanced materials that require precise control over microstructure and density.
-
Technical Considerations:
- Material Conductivity: The effectiveness of PPS can depend on the electrical conductivity of the material being sintered.
- Die Material: Graphite is commonly used for the die and punches due to its high thermal conductivity and ability to withstand high temperatures.
- Energy Efficiency: The rapid process and lower temperatures make PPS an energy-efficient sintering method.
-
Future Prospects:
- Research and Development: Ongoing research aims to optimize PPS parameters for different materials, potentially expanding its applications.
- Industrial Adoption: As the benefits of PPS become more widely recognized, it is likely to see increased adoption in industries requiring high-performance materials.
In summary, Pulse Plasma Sintering is a highly efficient and effective method for sintering powdered materials, offering significant advantages in terms of speed, temperature, and material properties. Its unique combination of rapid heating, lower temperatures, and short processing times makes it a valuable technique in the production of advanced materials.
Summary Table:
Aspect | Details |
---|---|
Mechanism | Pulsed high electric current discharges heat and press powdered materials. |
Advantages | Rapid heating/cooling, lower sintering temperatures, short holding times. |
Applications | Ceramics, metals, complex shapes, advanced materials. |
Comparison | Faster and more efficient than conventional sintering methods. |
Future Prospects | Ongoing research and increasing industrial adoption. |
Unlock the potential of Pulse Plasma Sintering for your materials—contact us today to learn more!