PVD (Physical Vapor Deposition) tools refer to equipment and machinery used to apply thin, durable coatings to various substrates, particularly cutting tools and other industrial components. These coatings enhance wear resistance, reduce friction, and prevent adhesion between tools and workpieces. PVD tools are widely used in industries such as metalworking, plastic injection molding, and semiconductor manufacturing. The process involves vaporizing a solid material in a vacuum and depositing it as a thin film on the target surface. Common coatings include titanium nitride (TiN) and chromium nitride (CrN), which provide high hardness and corrosion resistance. PVD tools are essential for producing high-performance, long-lasting industrial tools.
Key Points Explained:
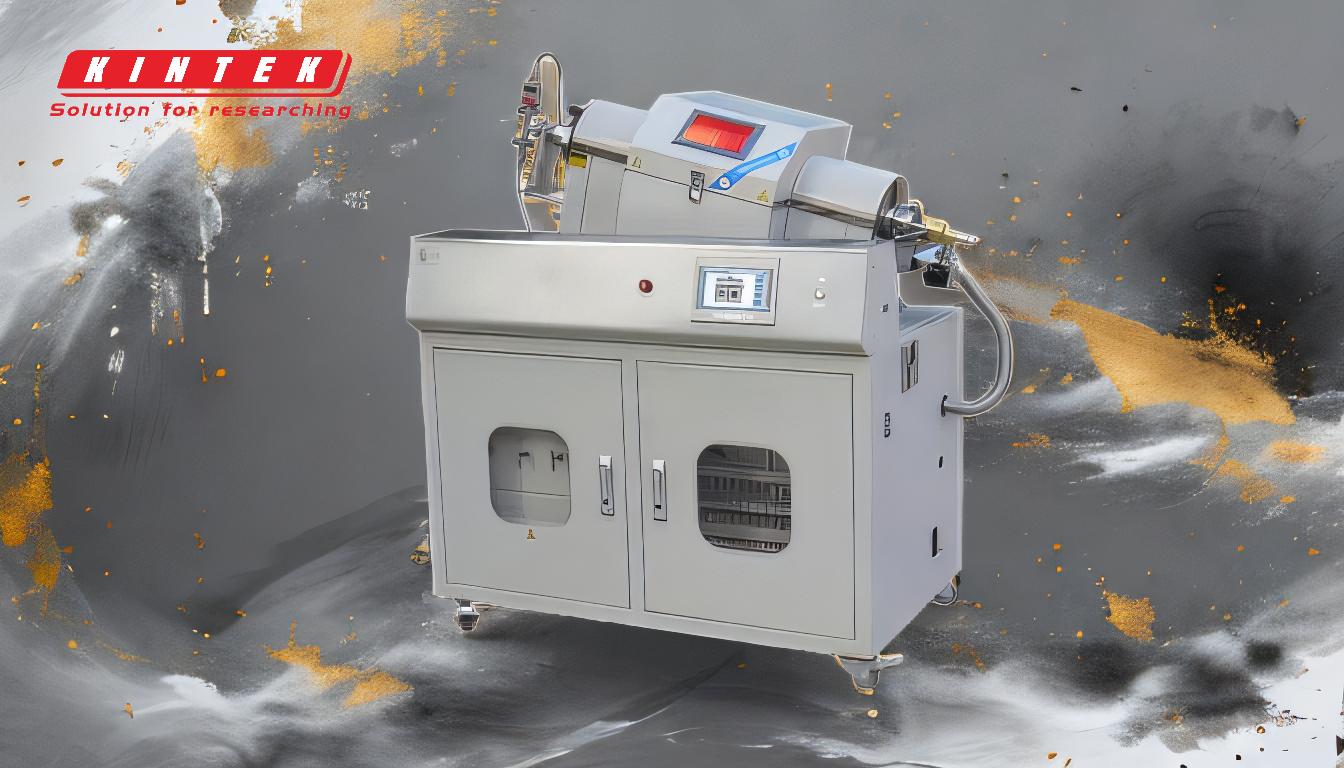
-
Definition of PVD Tools:
- PVD tools are specialized equipment used to apply thin, durable coatings to substrates through the Physical Vapor Deposition process.
- These tools are critical in industries requiring enhanced surface properties, such as wear resistance, reduced friction, and corrosion protection.
-
Applications of PVD Tools:
- Cutting Tools: PVD tools are extensively used to coat steel cutting tools, such as drills and screwdrivers, with materials like titanium nitride (TiN) and chromium nitride (CrN). These coatings improve tool lifespan and performance.
- Plastic Injection Molding: PVD-coated tools reduce the risk of adhesion and sticking between the tool and the workpiece, enhancing efficiency in plastic manufacturing.
- Semiconductor and Electronics: PVD tools are used to deposit thin films for semiconductor devices, thin-film solar panels, and other electronic components.
- Packaging: PVD is employed to create aluminized PET films for food packaging and balloons, providing barrier properties and durability.
-
Coating Characteristics:
- The coatings applied by PVD tools are typically less than 4µm thick, ensuring minimal impact on the tool's dimensions.
- These coatings are characterized by high hardness and low friction, making them ideal for heavy-duty applications.
- Common materials used in PVD coatings include ceramics, titanium nitride (TiN), and chromium nitride (CrN), which offer excellent wear and corrosion resistance.
-
PVD Process Overview:
- Vacuum Environment: The PVD process is conducted under high-temperature vacuum conditions to ensure purity and uniformity of the coating.
- Gasification of Precursor Material: A solid precursor material is gasified using high-power electricity or a laser, creating a vapor of the coating material.
- Plasma Creation: The gas is ionized to form plasma, often using an inductively coupled plasma (ICP) system. High-energy electrons collide with gas molecules, dissociating them into atoms.
- Deposition: The vaporized atoms are transported to the substrate, where they condense and form a thin, uniform film.
-
Advantages of PVD Tools:
- Enhanced Tool Performance: PVD coatings significantly improve the wear resistance and lifespan of cutting tools and machinery.
- Reduced Friction and Adhesion: The low-friction properties of PVD coatings minimize sticking between tools and workpieces, improving operational efficiency.
- Corrosion Resistance: Coatings like TiN and CrN provide excellent protection against corrosion, extending the life of tools in harsh environments.
- Versatility: PVD tools can deposit a wide range of materials, making them suitable for diverse applications across multiple industries.
-
Industries Benefiting from PVD Tools:
- Metalworking: PVD-coated tools are essential for machining and cutting operations, offering improved durability and performance.
- Plastic Manufacturing: PVD coatings reduce wear and adhesion in plastic injection molding tools, enhancing productivity.
- Electronics and Semiconductors: PVD tools are used to deposit thin films for electronic components, ensuring high performance and reliability.
- Packaging and Consumer Goods: PVD-coated films and surfaces provide durability and functionality in food packaging and other consumer applications.
-
Future Trends and Demand:
- The demand for PVD tools is growing due to the increasing need for high-quality, durable coatings in industrial applications.
- Innovations in PVD technology, such as advanced plasma generation techniques and new coating materials, are expanding the capabilities and applications of PVD tools.
- The semiconductor and renewable energy sectors are expected to drive significant growth in the PVD tools market, particularly for thin-film solar panels and electronic devices.
By understanding the role and capabilities of PVD tools, purchasers can make informed decisions about investing in equipment that enhances productivity, reduces maintenance costs, and improves the performance of industrial tools and components.
Summary Table:
Aspect | Details |
---|---|
Definition | Equipment for applying thin, durable coatings via Physical Vapor Deposition. |
Applications | Cutting tools, plastic molding, semiconductors, packaging. |
Coating Materials | Titanium nitride (TiN), chromium nitride (CrN), ceramics. |
Key Benefits | Wear resistance, reduced friction, corrosion protection. |
Industries Served | Metalworking, plastic manufacturing, electronics, packaging. |
Process Overview | Vacuum-based deposition of vaporized materials onto substrates. |
Ready to enhance your tools' performance? Contact us today to learn more about PVD solutions!