Quenching is a critical step in the casting and metalworking processes, where a material is rapidly cooled to achieve specific mechanical properties such as hardness, strength, and toughness. It involves heating the metal to a high temperature and then cooling it rapidly using a quenching medium, such as oil, water, or air. The choice of quenching medium and the cooling rate significantly influence the final properties of the metal. For instance, quenching oil is often preferred for its ability to control the cooling rate and minimize distortion or cracking in the metal. Additionally, processes like Hot Isostatic Pressing (HIPing) can further enhance the material's properties after quenching by improving tensile strength, ductility, and fatigue resistance. Understanding the nuances of quenching and its interaction with other processes is essential for achieving optimal material performance in casting and heat treatment.
Key Points Explained:
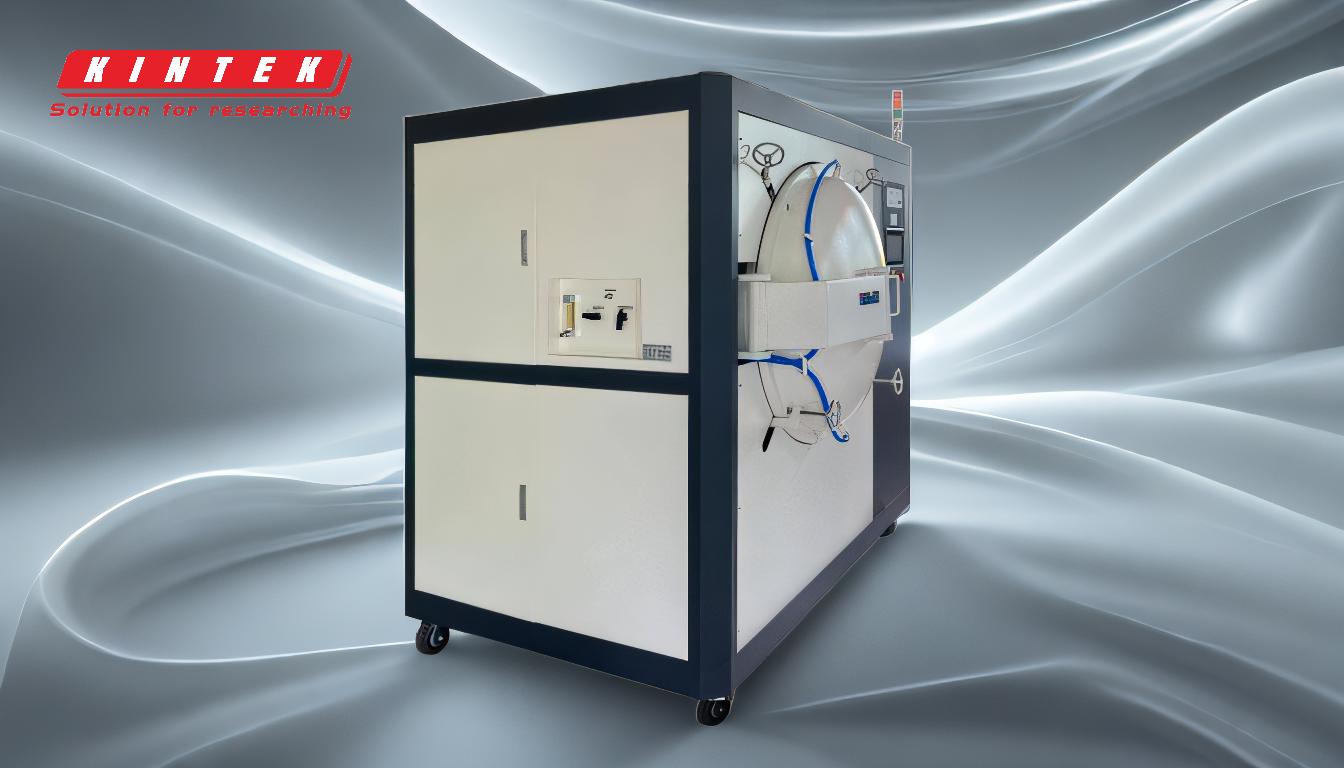
-
Definition of Quenching
Quenching is a heat treatment process where a metal is heated to a high temperature and then rapidly cooled to lock in desired properties such as hardness, strength, and toughness. This rapid cooling prevents the formation of undesirable microstructures and ensures the metal achieves its intended mechanical characteristics. -
Purpose of Quenching in Casting
- Hardness and Strength: Quenching helps increase the hardness and strength of the metal by creating a martensitic microstructure, which is highly resistant to deformation.
- Toughness and Ductility: Proper quenching can also improve toughness and ductility, depending on the cooling rate and the alloy composition.
- Dimensional Stability: It helps maintain the dimensional stability of the cast part by minimizing internal stresses and distortions.
-
Quenching Media and Their Effects
- Oil: Oil is a common quenching medium due to its ability to provide a controlled cooling rate, reducing the risk of cracking or warping. It is particularly suitable for alloy steels and complex geometries.
- Water: Water provides a faster cooling rate, making it ideal for carbon steels but increasing the risk of distortion or cracking.
- Air: Air quenching is used for materials that require slower cooling rates, such as certain tool steels, to achieve a balance between hardness and toughness.
- Polymer Solutions: These are used as an alternative to oil or water, offering adjustable cooling rates and reduced environmental impact.
-
Role of Quenching Oil
Quenching oil plays a vital role in achieving the desired properties of the metal. It ensures a uniform cooling rate, minimizes thermal gradients, and reduces the risk of cracking or distortion. The choice of quenching oil depends on the material being treated and the required mechanical properties. -
Interaction with HIPing (Hot Isostatic Pressing)
- Enhanced Properties: After quenching, processes like HIPing can further improve the material's mechanical properties. HIPing increases tensile and proof strengths by around 5% and ductility by up to 50%.
- Fatigue Resistance: HIPing significantly enhances fatigue properties, with up to tenfold improvements in fatigue life.
- Surface Finish and Toughness: It also improves impact strength, toughness, and machined surface finish, making the material more durable and reliable.
-
Considerations for Equipment and Consumable Purchasers
- Material Compatibility: Ensure the quenching medium is compatible with the material being treated to achieve the desired properties.
- Cooling Rate Control: Select quenching oils or other media that provide the appropriate cooling rate for the specific application.
- Environmental and Safety Factors: Consider the environmental impact and safety of the quenching medium, especially when dealing with oils or polymer solutions.
- Integration with Post-Treatment Processes: Evaluate how quenching interacts with subsequent processes like HIPing to optimize the final material properties.
By understanding these key points, equipment and consumable purchasers can make informed decisions about the quenching process and the materials used, ensuring optimal performance and cost-effectiveness in metalworking and casting applications.
Summary Table:
Key Aspect | Details |
---|---|
Definition | Rapid cooling of heated metal to achieve hardness, strength, and toughness. |
Purpose | Enhances hardness, strength, toughness, and dimensional stability. |
Quenching Media | Oil (controlled cooling), water (fast cooling), air (slow cooling). |
Role of Quenching Oil | Ensures uniform cooling, minimizes cracking, and reduces distortion. |
Interaction with HIPing | Improves tensile strength, ductility, fatigue resistance, and toughness. |
Optimize your casting process with the right quenching solutions—contact our experts today!