The sintering process in dentistry, particularly for zirconia, is a critical thermal treatment that transforms zirconia powder into a dense, strong, and durable ceramic material suitable for dental restorations like crowns, bridges, and implants. This process involves several stages, including powder preparation, compaction, and controlled heating in a zirconia sintering furnace. The goal is to reduce porosity and increase density, resulting in a material with enhanced mechanical properties. The process typically includes heating, sintering, and cooling phases, ensuring the material achieves its final hardness and structural integrity.
Key Points Explained:
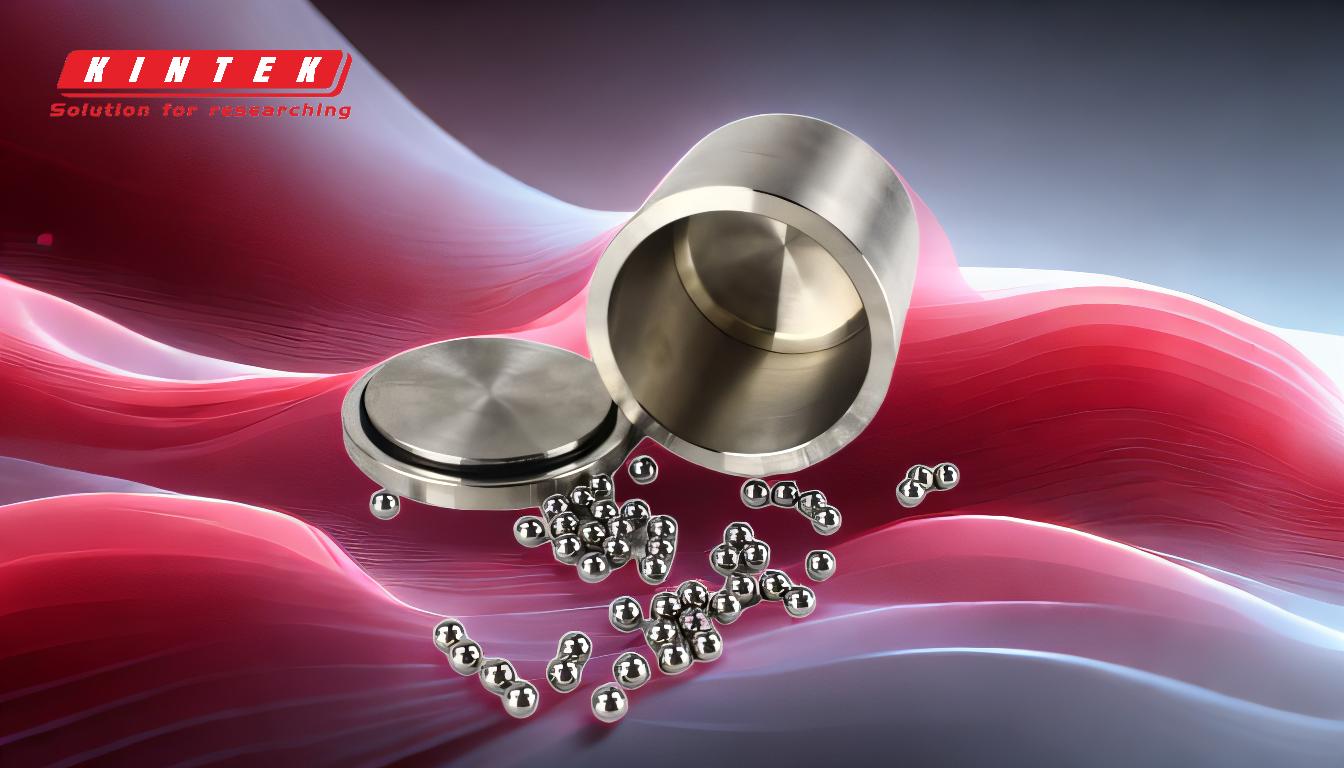
-
Overview of the Sintering Process:
- Sintering is a thermal process used to densify zirconia powder by heating it below its melting point. This process eliminates porosity and strengthens the material, making it suitable for dental applications.
- The process is divided into three main phases: heating, sintering, and cooling. Each phase is carefully controlled to ensure optimal material properties.
-
Stages of the Sintering Process:
- Powder Preparation: The zirconia powder is mixed with binders, deflocculants, and other additives to create a homogeneous slurry. This slurry is then shaped into the desired form, such as a crown or bridge, using techniques like cold pressing or 3D printing.
- Compaction: The shaped powder, known as the "green part," is compacted to remove air pockets and ensure uniformity. This step is crucial for achieving a dense final product.
- Heating and Sintering: The green part is placed in a zirconia sintering furnace and subjected to controlled heating. The temperature is carefully regulated to facilitate particle bonding without melting the material. During this phase, particles undergo diffusion, forming necks and densifying the structure.
- Cooling: After sintering, the material is slowly cooled to room temperature. This allows the zirconia to solidify into a rigid and cohesive structure with minimal internal stresses.
-
Role of the Sintering Furnace:
- The zirconia sintering furnace is a critical component of the sintering process. It provides precise temperature control and uniform heating, ensuring consistent results.
- The furnace operates at temperatures below the melting point of zirconia, allowing the material to densify through solid-state diffusion rather than liquefaction.
-
Benefits of Sintering in Dentistry:
- Enhanced Mechanical Properties: Sintering increases the density and hardness of zirconia, making it highly resistant to wear and fracture.
- Biocompatibility: The process ensures that the final product is free from impurities, making it safe for use in the human body.
- Aesthetic Appeal: Sintered zirconia can be polished and colored to match natural teeth, providing both functional and cosmetic benefits.
-
Applications in Dentistry:
- Sintered zirconia is widely used for dental crowns, bridges, and implants due to its strength, durability, and biocompatibility.
- The material's ability to withstand the forces of chewing and its resistance to staining make it an ideal choice for long-term dental restorations.
-
Challenges and Considerations:
- Precision in Temperature Control: Achieving the correct sintering temperature is crucial. Overheating can lead to grain growth and reduced strength, while insufficient heating may result in incomplete densification.
- Cooling Rate: Rapid cooling can cause thermal stresses, leading to cracks or warping. A controlled cooling rate is essential to maintain the material's integrity.
In summary, the sintering process in dentistry is a sophisticated thermal treatment that transforms zirconia powder into a high-performance ceramic material. By carefully controlling each stage of the process, dental professionals can produce restorations that are strong, durable, and aesthetically pleasing. The zirconia sintering furnace plays a pivotal role in ensuring the success of this process, making it an indispensable tool in modern dental laboratories.
Summary Table:
Key Aspect | Details |
---|---|
Overview | Thermal process to densify zirconia powder, reducing porosity and enhancing strength. |
Stages | Powder preparation, compaction, heating, sintering, and controlled cooling. |
Role of Sintering Furnace | Ensures precise temperature control and uniform heating for optimal results. |
Benefits | Enhanced mechanical properties, biocompatibility, and aesthetic appeal. |
Applications | Dental crowns, bridges, and implants. |
Challenges | Precision in temperature control and cooling rate to avoid defects. |
Discover how the sintering process can elevate your dental restorations—contact our experts today!