Sputtering is a physical vapor deposition (PVD) technique used to deposit thin films of materials onto substrates. It involves creating a plasma by applying a high voltage to a target material in a vacuum chamber filled with an inert gas, typically argon. The plasma ionizes the gas atoms, which then collide with the target material, ejecting atoms or molecules from its surface. These ejected particles travel through the vacuum and deposit onto a substrate, forming a thin film. Sputtering is widely used in industries such as semiconductors, optics, and coatings due to its ability to produce high-quality, uniform films at relatively low temperatures, making it suitable for heat-sensitive materials.
Key Points Explained:
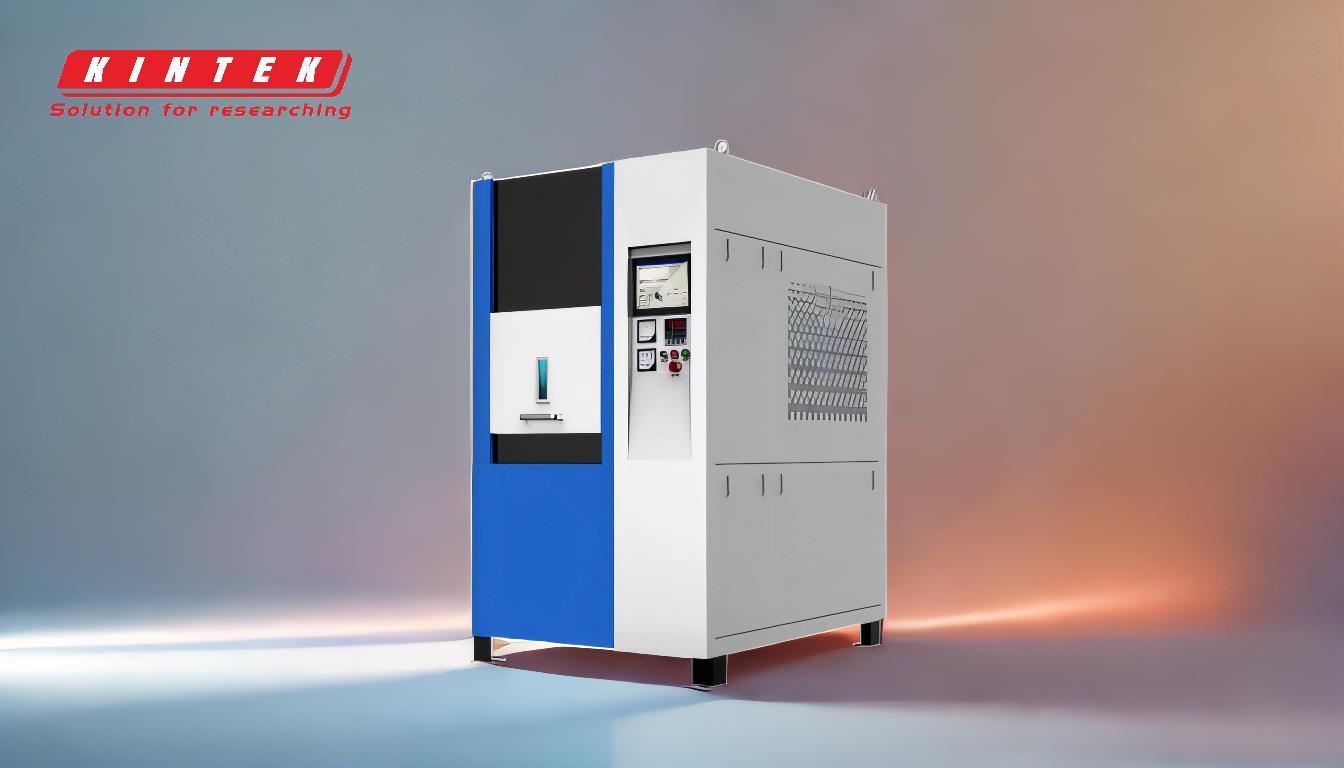
-
Basic Principle of Sputtering:
- Sputtering is a process where atoms are ejected from a solid target material due to bombardment by high-energy ions.
- The target material is placed in a vacuum chamber, and an inert gas (usually argon) is introduced.
- A high voltage is applied between the target (cathode) and the chamber, creating a plasma.
- The plasma ionizes the gas atoms, which are then accelerated toward the target, causing collisions that eject target atoms.
-
Role of Plasma in Sputtering:
- Plasma is a partially ionized gas containing free electrons, ions, and neutral atoms.
- In sputtering, the plasma is generated by applying a high voltage, which ionizes the inert gas.
- The positively charged gas ions are attracted to the negatively charged target, where they collide and transfer momentum to the target atoms, ejecting them.
-
Deposition of Thin Films:
- The ejected target atoms travel through the vacuum and deposit onto a substrate placed opposite the target.
- The deposited atoms form a thin film on the substrate, layer by layer.
- This process is highly controllable, allowing for precise thickness and uniformity of the film.
-
Advantages of Sputtering:
- Low Temperature Process: Sputtering can be performed at low temperatures, making it suitable for heat-sensitive substrates like plastics.
- High-Quality Films: The films produced are dense, uniform, and have good adhesion to the substrate.
- Versatility: A wide range of materials, including metals, alloys, and ceramics, can be deposited using sputtering.
-
Types of Sputtering:
- DC Sputtering: Uses a direct current (DC) power supply to create the plasma. Suitable for conductive materials.
- RF Sputtering: Uses radio frequency (RF) power to sputter non-conductive materials.
- Magnetron Sputtering: Incorporates magnetic fields to enhance the plasma density, increasing the sputtering rate and efficiency.
-
Applications of Sputtering:
- Semiconductor Industry: Used for depositing thin films of metals, oxides, and nitrides in the fabrication of integrated circuits.
- Optical Coatings: Used to create anti-reflective, reflective, and protective coatings on lenses and mirrors.
- Decorative Coatings: Used to apply thin films of metals and alloys for decorative purposes on products like watches and jewelry.
- Hard Coatings: Used to deposit wear-resistant coatings on tools and components.
-
Re-Sputtering:
- In some cases, the deposited material can be re-sputtered, where the deposited atoms are bombarded again, leading to further refinement or modification of the film.
- This process can improve the quality and properties of the deposited film.
-
Momentum Transfer in Sputtering:
- The key mechanism in sputtering is the transfer of momentum from the high-energy ions to the target atoms.
- This momentum transfer causes the target atoms to be ejected from the surface and travel toward the substrate.
-
Vacuum Environment:
- Sputtering is performed in a high vacuum to prevent contamination from air or other gases.
- The vacuum also ensures that the sputtered particles travel in straight lines to the substrate, resulting in uniform deposition.
-
Substrate Compatibility:
- Sputtering is compatible with a wide range of substrates, including metals, glass, ceramics, and polymers.
- The low-temperature nature of the process allows for the coating of heat-sensitive materials without damage.
In summary, sputtering is a versatile and widely used thin film deposition technique that relies on the ejection of target atoms due to ion bombardment. The process is performed in a vacuum environment, uses plasma to ionize inert gas, and deposits high-quality films on various substrates. Its applications span multiple industries, making it a critical technology in modern manufacturing and materials science.
Summary Table:
Aspect | Details |
---|---|
Basic Principle | Atoms ejected from a target material by high-energy ion bombardment. |
Role of Plasma | Plasma ionizes inert gas, accelerating ions to collide with the target. |
Deposition Process | Ejected atoms deposit onto substrates, forming thin, uniform films. |
Advantages | Low temperature, high-quality films, versatile material compatibility. |
Types of Sputtering | DC, RF, and Magnetron sputtering for different materials and applications. |
Applications | Semiconductors, optical coatings, decorative coatings, and hard coatings. |
Key Benefit | Suitable for heat-sensitive materials and precise film thickness control. |
Discover how sputtering can enhance your manufacturing process—contact our experts today!