Tempering and annealing are both heat treatment processes used to alter the physical and chemical properties of metals, making them suitable for manufacturing. Tempering involves heating metal to a lower temperature and cooling it rapidly to improve toughness and reduce brittleness, while annealing involves heating metal to a higher temperature and cooling it slowly to soften the material, improve ductility, and relieve internal stresses. Both processes are essential for enhancing the mechanical properties of metals, but they differ in temperature ranges, cooling rates, and the specific outcomes they achieve.
Key Points Explained:
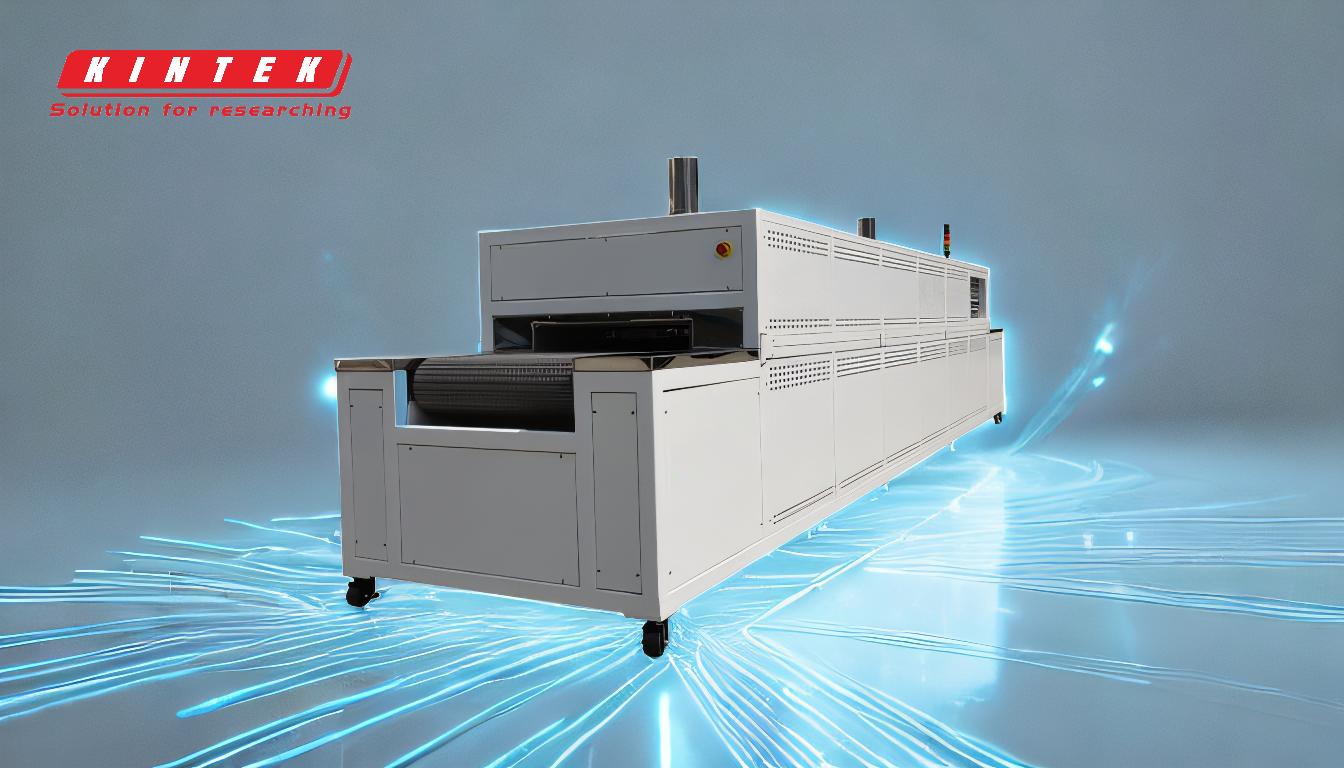
-
Definition and Purpose of Heat Treatment:
- Heat treatment involves controlled heating and cooling of metals to achieve desired physical and chemical properties.
- Common goals include improving hardness, toughness, ductility, and stress relief.
- Processes like tempering and annealing are part of a broader range of heat treatment methods, including quenching, case hardening, and normalizing.
-
Annealing: Process and Outcomes:
- Temperature Range: Annealing typically occurs at high temperatures, often between 1,200°F and 2,400°F, depending on the material.
- Cooling Rate: The metal is cooled slowly, often in a furnace or by burying it in insulating material, to allow the microstructure to stabilize.
-
Purpose:
- Softens the metal, making it easier to machine or form.
- Improves ductility and reduces internal stresses.
- Refines grain structure for better mechanical properties.
- Applications: Used in manufacturing processes where malleability and reduced hardness are required, such as in wire drawing or sheet metal forming.
-
Tempering: Process and Outcomes:
- Temperature Range: Tempering is performed at lower temperatures, typically between 300°F and 1,000°F, after hardening processes like quenching.
- Cooling Rate: The metal is cooled at a faster rate than annealing, often in air or oil.
-
Purpose:
- Reduces brittleness and increases toughness.
- Balances hardness and ductility for improved performance.
- Relieves internal stresses caused by rapid cooling during quenching.
- Applications: Commonly used for tools, springs, and structural components that require a combination of strength and flexibility.
-
Key Differences Between Tempering and Annealing:
- Temperature: Tempering uses lower temperatures compared to annealing.
- Cooling Rate: Tempering involves faster cooling, while annealing requires slow cooling.
- Outcomes: Tempering focuses on toughness and stress relief, whereas annealing emphasizes softening and ductility.
-
Common Heat Treatment Methods:
- Through-Hardening: Increases hardness throughout the material.
- Case Hardening: Hardens only the surface layer, leaving the core softer.
- Quenching: Rapid cooling to achieve high hardness but may increase brittleness.
- Normalizing: Similar to annealing but with faster cooling to refine grain structure.
- Carburizing: Adds carbon to the surface to increase hardness.
-
Importance of Controlled Atmospheres:
- Heat treatment often requires specific atmospheres (e.g., hydrogen, nitrogen, or argon) to prevent oxidation and ensure uniform results.
- Processes like bright annealing use pure hydrogen or nitrogen to minimize surface oxidation.
-
Applications in Manufacturing:
- Annealing: Used for materials that need to be shaped or machined, such as copper wires or steel sheets.
- Tempering: Applied to components that require a balance of hardness and toughness, such as gears, blades, and springs.
-
Stress Relief and Homogenization:
- Both tempering and annealing can relieve internal stresses caused by machining, forming, or welding.
- Homogenization during annealing ensures uniform properties throughout the material.
-
Material-Specific Considerations:
- Different metals and alloys require specific heat treatment parameters to achieve optimal results.
- For example, steel is commonly tempered after quenching, while aluminum alloys may undergo precipitation hardening.
-
Role in Enhancing Mechanical Properties:
- Heat treatment processes like tempering and annealing are critical for achieving the desired mechanical properties in metals, ensuring they meet performance requirements for specific applications.
By understanding the principles and applications of tempering and annealing, manufacturers can select the appropriate heat treatment process to optimize the properties of metals for their intended use.
Summary Table:
Aspect | Tempering | Annealing |
---|---|---|
Temperature Range | 300°F - 1,000°F | 1,200°F - 2,400°F |
Cooling Rate | Faster (air or oil) | Slower (furnace or insulating material) |
Purpose | Improves toughness, reduces brittleness | Softens metal, improves ductility |
Applications | Tools, springs, structural components | Wire drawing, sheet metal forming |
Need help choosing the right heat treatment process? Contact our experts today!