Quenching is a critical heat treatment process used to enhance the mechanical properties of metals, such as hardness and strength. It involves rapidly cooling a heated workpiece by immersing it in a quenching medium like oil, gas, or water. Each quenching method has its own advantages and disadvantages, depending on the material, desired properties, and application. For instance, vacuum gas quenching uses inert gases like argon or helium, resulting in a smooth surface finish without the need for cleaning, while vacuum oil quenching offers faster cooling rates and bright, oxidation-free surfaces. However, quenching can also introduce challenges, such as distortion or cracking due to rapid cooling. Understanding the pros and cons of quenching helps in selecting the most suitable method for specific applications.
Key Points Explained:
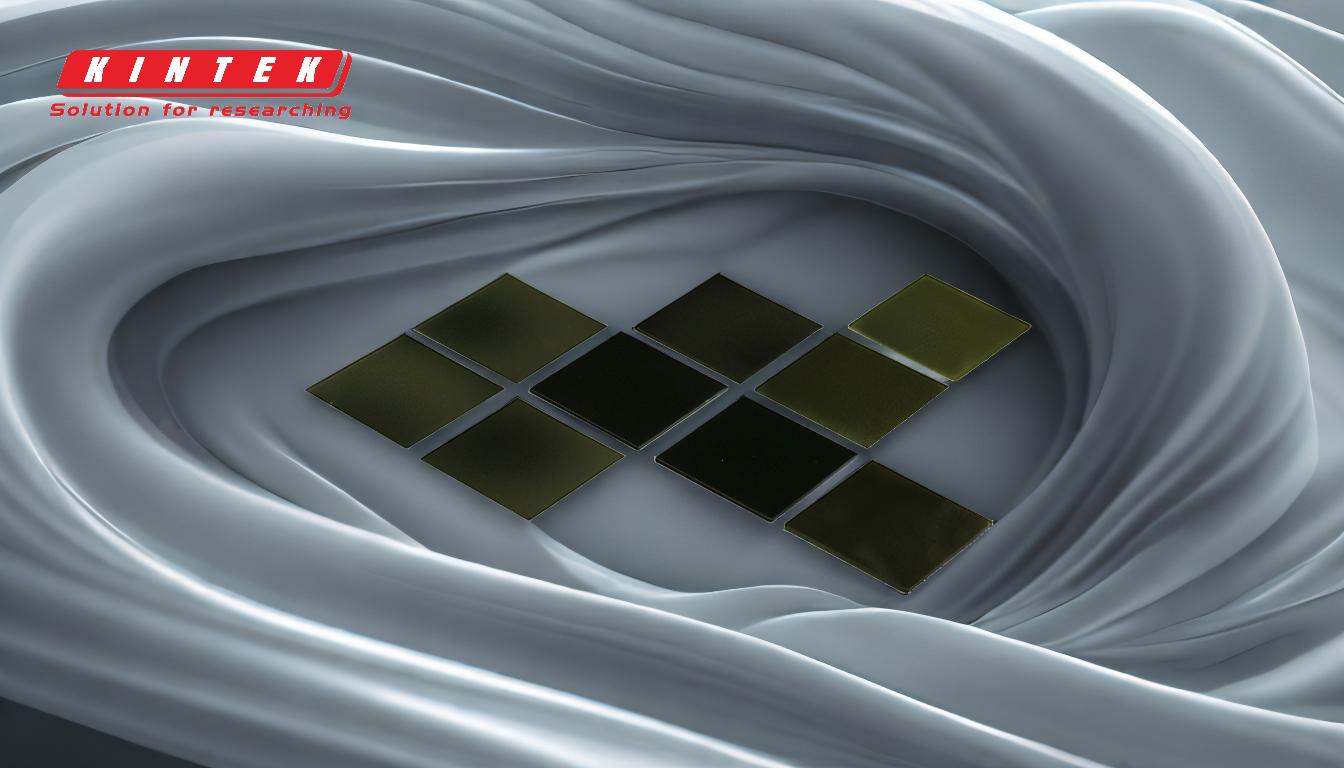
-
Advantages of Quenching:
- Enhanced Mechanical Properties: Quenching significantly increases the hardness and strength of metals by transforming their microstructure, particularly in steel, where it forms martensite.
- Surface Quality: Vacuum gas quenching uses high-purity inert gases like argon or helium, ensuring a smooth surface finish without the need for additional cleaning. Similarly, vacuum oil quenching produces bright, oxidation-free surfaces with good organizational properties.
- Precision and Control: Quenching in a vacuum furnace eliminates surface oxidation and decarburization, ensuring consistent material properties. The ability to manage partial gas pressure allows for advanced processes like carburizing or carbonitriding at low pressures, reducing cycle times.
-
Disadvantages of Quenching:
- Risk of Distortion and Cracking: Rapid cooling during quenching can cause internal stresses, leading to distortion or cracking in the workpiece. This is particularly problematic for complex shapes or thin sections.
- Limited Cooling Rates: While oil quenching cools faster than gas quenching, it may still not be sufficient for certain high-speed applications, potentially limiting its effectiveness for some materials.
- Cost and Complexity: Vacuum quenching methods, such as gas or oil quenching, require specialized equipment and controlled environments, increasing operational costs and complexity compared to traditional quenching methods.
-
Comparison of Quenching Methods:
- Vacuum Gas Quenching: Ideal for applications requiring a clean, oxidation-free surface. However, it may not provide the same cooling rate as oil quenching, making it less suitable for materials requiring rapid cooling.
- Vacuum Oil Quenching: Offers faster cooling rates and is better suited for achieving high hardness in materials. However, it requires post-quenching cleaning and may introduce more distortion compared to gas quenching.
-
Applications and Considerations:
- Material Selection: The choice of quenching method depends on the material being treated. For example, high-alloy steels may benefit more from vacuum gas quenching due to their sensitivity to oxidation.
- Workpiece Geometry: Complex or thin-walled components are more prone to distortion and cracking, making controlled quenching methods like vacuum quenching preferable.
- Cost-Benefit Analysis: While vacuum quenching methods offer superior surface quality and precision, their higher costs must be weighed against the benefits for each specific application.
By carefully evaluating the advantages and disadvantages of quenching, manufacturers can optimize their heat treatment processes to achieve the desired material properties while minimizing risks and costs.
Summary Table:
Aspect | Advantages | Disadvantages |
---|---|---|
Enhanced Properties | Increases hardness and strength; transforms microstructure (e.g., martensite). | Risk of distortion or cracking due to rapid cooling. |
Surface Quality | Smooth, oxidation-free surfaces (vacuum gas quenching); bright surfaces (oil). | Oil quenching requires post-cleaning; gas quenching has slower cooling rates. |
Precision and Control | Eliminates oxidation and decarburization; allows advanced processes. | Higher costs and complexity with vacuum quenching methods. |
Cooling Rates | Oil quenching offers faster cooling for high hardness. | Limited cooling rates may not suit high-speed applications. |
Ready to optimize your heat treatment process? Contact our experts today to find the best quenching solution for your needs!