Heat treatment is a critical process in the aerospace industry, ensuring that aircraft components meet the rigorous demands of extreme conditions. By altering the metallurgical properties of metal parts through controlled heating and cooling, heat treatment enhances strength, durability, and performance. Vacuum heat treatment, in particular, is essential for protecting alloys from contamination and ensuring even heating and faster cooling. This process improves grain structure, reduces stress, and extends the lifespan of components, ultimately contributing to safer, more efficient, and longer-lasting aircraft.
Key Points Explained:
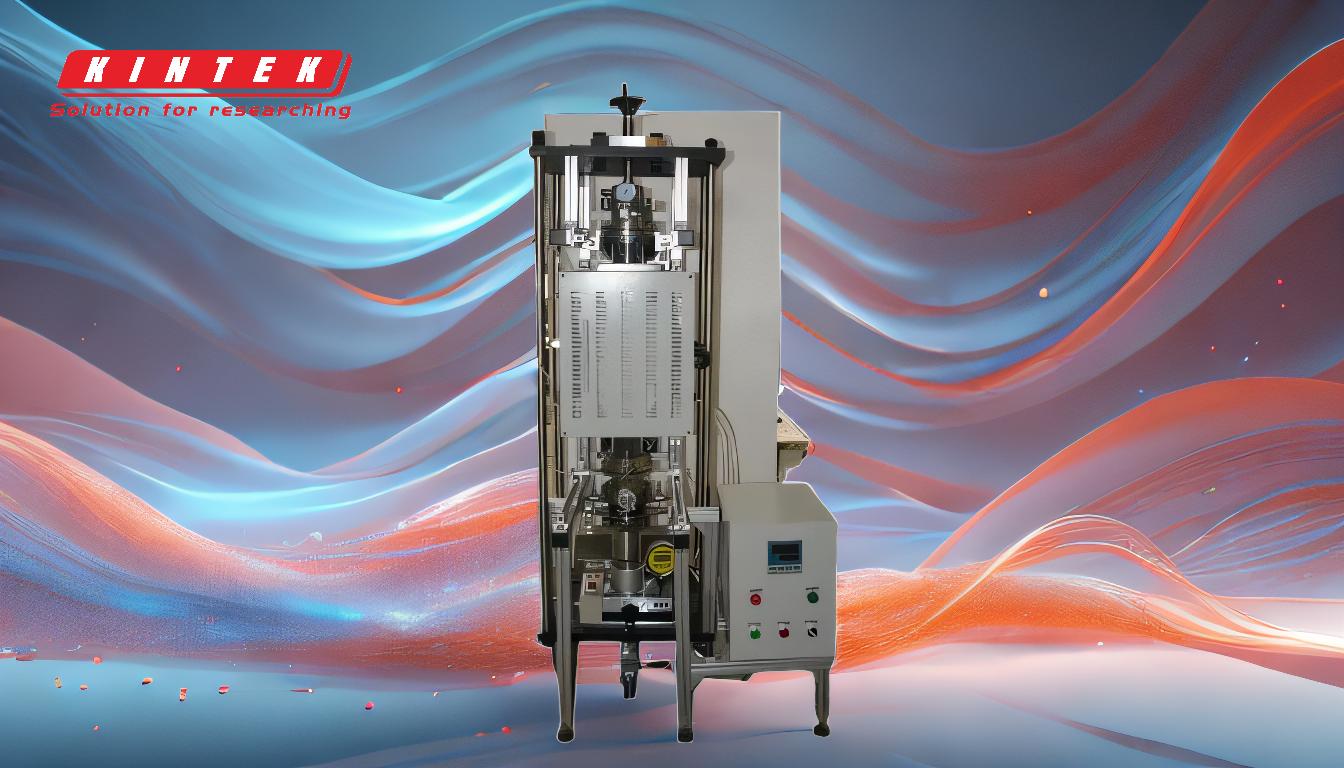
-
Enhancing Material Properties:
- Heat treatment modifies the metallurgical properties of metal parts, improving their strength, durability, and performance.
- This is crucial for aerospace components, which must withstand extreme conditions such as high stress, temperature fluctuations, and fatigue.
-
Vacuum Heat Treatment:
- Vacuum heat treatment is particularly important in aerospace applications. It protects metal alloys from contamination by oxygen, nitrogen, or hydrogen, which can degrade material quality.
- This method ensures even heating and faster cooling, leading to more consistent and reliable material properties.
-
Improving Grain Structure:
- Heat treatment refines the grain structure of alloys, making them more uniform and less prone to defects.
- Improved grain structure enhances the overall strength and fatigue life of components, which is vital for the longevity and safety of aircraft.
-
Reducing Stress on Metal Parts:
- The process of heat treatment helps to relieve internal stresses in metal parts that can occur during manufacturing.
- Reduced stress levels contribute to the durability and reliability of aerospace components, minimizing the risk of failure during operation.
-
Extending Component Lifespan:
- By enhancing material properties and reducing stress, heat treatment extends the lifespan of aerospace components.
- This leads to fewer repairs and replacements, reducing maintenance costs and improving the overall efficiency of aircraft operations.
-
NASA's Role in Defining Heat Treatment Standards:
- NASA has defined nine types of vacuum heat treatments, which are essential for building aircraft with higher strength materials.
- These standards ensure that aerospace components meet the rigorous demands of modern aviation, contributing to safer and more reliable aircraft.
-
Critical for Extreme Conditions:
- Aerospace components are subjected to extreme conditions, including high stress, temperature variations, and fatigue.
- Heat treatment ensures that these components can withstand such conditions, maintaining optimal performance and safety.
-
Contribution to Aircraft Efficiency:
- The improved strength and durability of heat-treated components contribute to the overall efficiency of aircraft.
- Enhanced performance and reduced maintenance needs lead to more reliable and cost-effective aircraft operations.
-
Ensuring Safety and Reliability:
- The primary goal of heat treatment in the aerospace industry is to ensure the safety and reliability of aircraft.
- By improving material properties and extending component lifespan, heat treatment plays a crucial role in maintaining the high standards required in aviation.
In summary, heat treatment, particularly vacuum heat treatment, is indispensable in the aerospace industry. It enhances material properties, improves grain structure, reduces stress, and extends the lifespan of components, all of which are critical for ensuring the safety, reliability, and efficiency of aircraft. NASA's defined standards further underscore the importance of this process in meeting the rigorous demands of modern aviation.
Summary Table:
Key Benefit | Description |
---|---|
Enhanced Material Properties | Improves strength, durability, and performance of aerospace components. |
Vacuum Heat Treatment | Protects alloys from contamination, ensures even heating, and faster cooling. |
Improved Grain Structure | Refines grain structure for uniform strength and reduced defects. |
Reduced Stress | Relieves internal stresses, enhancing component reliability. |
Extended Component Lifespan | Reduces repairs and replacements, lowering maintenance costs. |
NASA Standards | Defines nine vacuum heat treatments for higher-strength aerospace materials. |
Aircraft Efficiency | Enhances performance and reduces maintenance, improving operational efficiency. |
Safety and Reliability | Ensures components withstand extreme conditions, maintaining high safety standards. |
Learn how heat treatment can optimize your aerospace components—contact our experts today!