Heat treatment of aluminum is a critical process used to enhance its mechanical properties, such as hardness, strength, and ductility. The best method for heat treatment depends on the specific aluminum alloy and the desired properties. Common methods include solution heat treatment, aging (natural or artificial), and annealing. Each method has its own set of parameters, such as temperature, time, and cooling rate, which must be carefully controlled to achieve the desired results. Understanding the alloy composition and the intended application is essential for selecting the appropriate heat treatment method.
Key Points Explained:
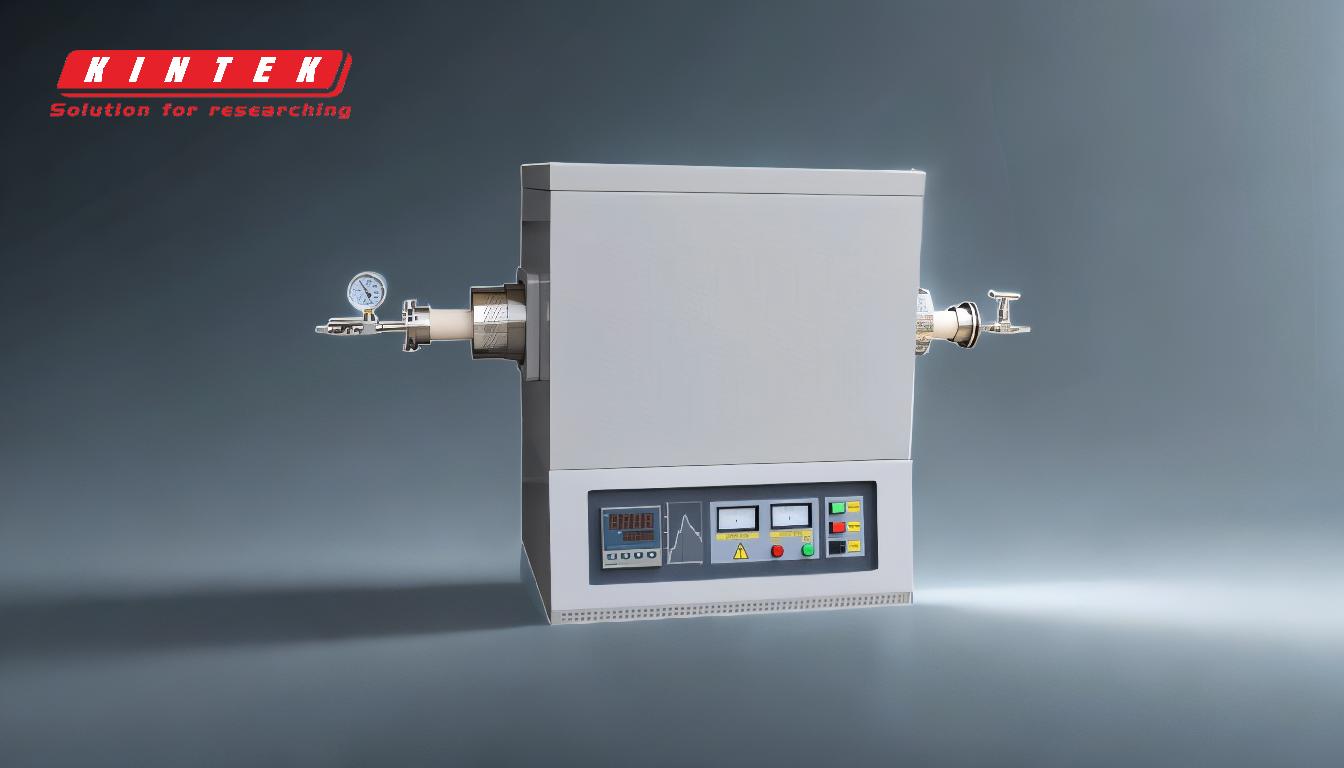
-
Solution Heat Treatment:
- Purpose: This process involves heating the aluminum alloy to a temperature where the alloying elements dissolve into the aluminum matrix, forming a solid solution.
- Temperature: Typically between 450°C to 540°C, depending on the alloy.
- Time: The material is held at this temperature for a sufficient time to allow the alloying elements to fully dissolve.
- Cooling: Rapid cooling, often by quenching in water, is required to maintain the solid solution at room temperature.
- Application: This method is commonly used for alloys that are intended to be aged, such as 2000, 6000, and 7000 series aluminum alloys.
-
Aging (Precipitation Hardening):
- Natural Aging: After solution heat treatment, the alloy is left at room temperature to allow the alloying elements to precipitate out of the solid solution, forming fine particles that strengthen the material.
- Artificial Aging: This involves heating the alloy to a lower temperature (typically 120°C to 190°C) for a controlled period to accelerate the precipitation process.
- Effect: Aging increases the strength and hardness of the aluminum alloy, making it suitable for high-stress applications.
- Application: Commonly used for aerospace and automotive components where high strength-to-weight ratios are required.
-
Annealing:
- Purpose: Annealing is used to soften the aluminum, making it more ductile and easier to work with.
- Temperature: The alloy is heated to a temperature between 300°C to 410°C, depending on the alloy.
- Time: The material is held at this temperature for a period sufficient to allow recrystallization and grain growth.
- Cooling: Slow cooling, often in the furnace, is used to prevent the formation of internal stresses.
- Application: This method is often used for aluminum sheets and wires that need to be formed or bent without cracking.
-
Alloy-Specific Considerations:
- 2000 Series (Al-Cu): These alloys are typically solution heat treated and then aged to achieve high strength.
- 6000 Series (Al-Mg-Si): These alloys are often solution heat treated and artificially aged to achieve a balance of strength and corrosion resistance.
- 7000 Series (Al-Zn): These alloys are solution heat treated and aged to achieve the highest strength among aluminum alloys.
-
Process Control:
- Temperature Control: Precise temperature control is crucial to avoid overheating, which can lead to grain growth and reduced mechanical properties.
- Time Management: The duration of heat treatment must be carefully controlled to ensure complete dissolution or precipitation of alloying elements.
- Cooling Rate: The rate of cooling after heat treatment affects the final properties of the aluminum. Rapid cooling is generally used for solution heat treatment, while slow cooling is used for annealing.
-
Equipment:
- Furnaces: High-quality furnaces with precise temperature control are essential for effective heat treatment.
- Quenching Tanks: For solution heat treatment, quenching tanks with water or other cooling media are necessary to achieve rapid cooling.
- Aging Ovens: For artificial aging, ovens with controlled temperature and time settings are required.
In conclusion, the best method for heat treatment of aluminum depends on the specific alloy and the desired properties. Solution heat treatment followed by aging is commonly used for high-strength applications, while annealing is used for applications requiring increased ductility. Proper process control and equipment are essential to achieve the desired results.
Summary Table:
Method | Purpose | Temperature Range | Cooling | Application |
---|---|---|---|---|
Solution Heat Treatment | Dissolve alloying elements into the aluminum matrix for solid solution. | 450°C to 540°C | Rapid cooling (quenching) | Used for 2000, 6000, and 7000 series alloys. |
Aging (Natural/Artificial) | Strengthen material by precipitating alloying elements. | 120°C to 190°C | Room temperature or controlled | High-strength applications like aerospace and automotive components. |
Annealing | Soften aluminum for increased ductility and workability. | 300°C to 410°C | Slow cooling (in furnace) | Used for aluminum sheets and wires requiring forming or bending. |
Need help selecting the right heat treatment method for your aluminum alloy? Contact our experts today!