The best temperature for hardening steel depends on the type of steel, its carbon content, and the desired properties. Generally, steel is heated to a temperature where it becomes austenitic, typically between 800°C and 900°C, followed by rapid cooling (quenching) to achieve maximum hardness. However, the exact temperature varies based on the steel's composition and intended application. Proper temperature control is crucial, as it influences grain boundary diffusion and bulk diffusion, which directly affect the material's final hardness and microstructure.
Key Points Explained:
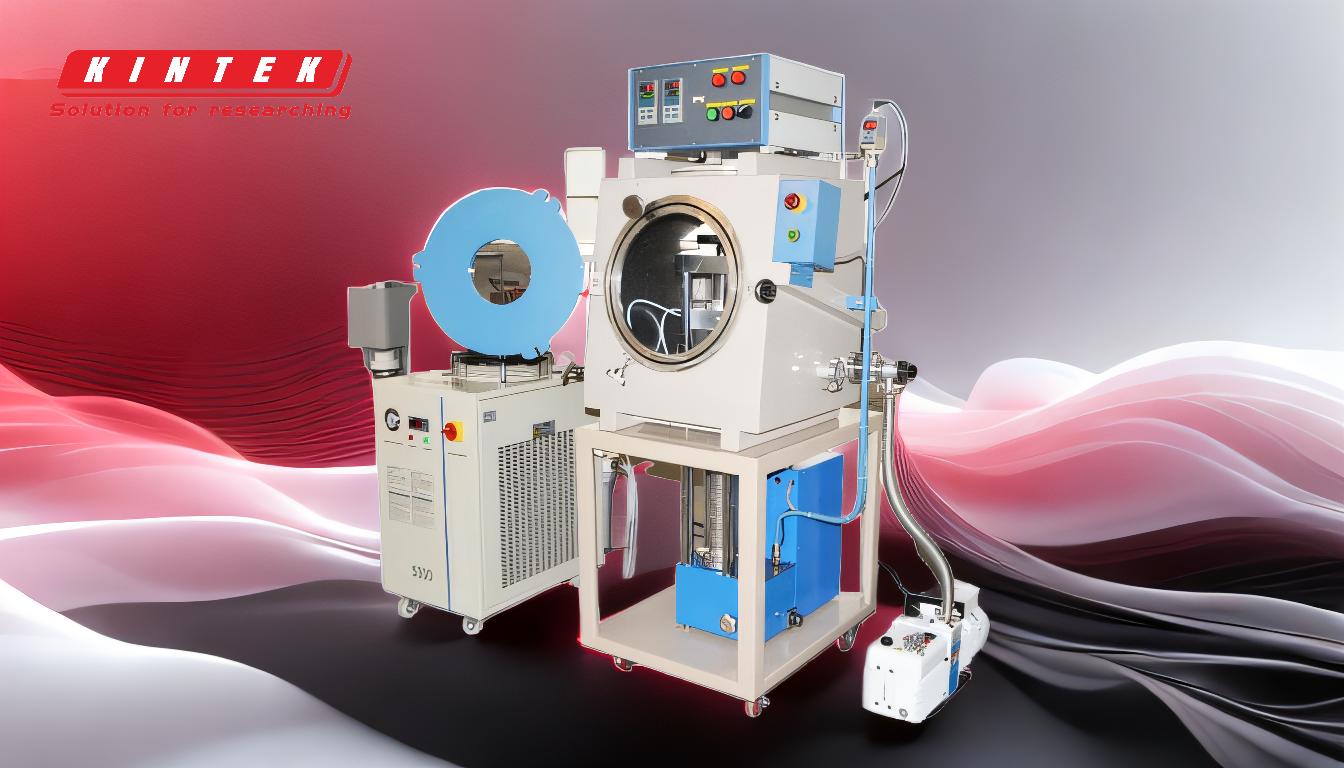
-
Importance of Temperature in Hardening Steel:
- Temperature control is critical during the hardening process because it directly influences the steel's microstructure. Heating steel to the correct austenitizing temperature ensures the formation of a uniform austenite phase, which is essential for achieving optimal hardness after quenching.
- Grain boundary diffusion and bulk diffusion are temperature-dependent processes. These diffusion mechanisms determine how atoms rearrange during heating and cooling, affecting the steel's final properties.
-
Optimal Temperature Range:
- For most carbon steels, the hardening temperature typically ranges between 800°C and 900°C. This range ensures the steel reaches the austenitic phase, where carbon is uniformly dissolved in the iron matrix.
- The exact temperature depends on the steel's carbon content. Low-carbon steels require higher temperatures, while high-carbon steels may need slightly lower temperatures to avoid excessive grain growth.
-
Role of Quenching:
- After heating, steel must be rapidly cooled (quenched) in water, oil, or air, depending on the steel type. Quenching locks the austenite into a hard, brittle martensitic structure.
- The quenching medium and cooling rate are equally important as the heating temperature. Improper cooling can lead to insufficient hardness or cracking.
-
Material-Specific Considerations:
- Different steel alloys have unique hardening requirements. For example, tool steels or stainless steels may require specific temperature ranges tailored to their alloying elements.
- Overheating can cause grain coarsening, reducing toughness, while underheating may result in incomplete austenitization, leading to soft spots.
-
Practical Applications:
- In industrial settings, precise temperature control is achieved using furnaces equipped with thermocouples and digital controllers. This ensures consistent results and minimizes defects.
- For small-scale applications, such as knife-making, a muffle furnace or forge is often used to reach the required hardening temperature.
By understanding these key points, a purchaser can make informed decisions about the equipment and processes needed for hardening steel, ensuring the desired hardness and durability are achieved.
Summary Table:
Key Factor | Details |
---|---|
Optimal Temperature Range | 800°C–900°C for most carbon steels, depending on carbon content. |
Quenching Process | Rapid cooling in water, oil, or air to lock in martensitic structure. |
Material-Specific Needs | Tool steels and stainless steels may require tailored temperature ranges. |
Temperature Control | Critical for uniform austenitization and avoiding defects like grain growth. |
Applications | Industrial furnaces or small-scale tools like muffle furnaces for precision. |
Need precise temperature control for hardening steel? Contact our experts today to find the right solution!