The brazing process is a method of joining metal components using a filler metal with a lower melting point than the base materials. It is widely used in industries for creating strong, reliable, and repeatable metallurgical bonds. The process involves heating the components to a specific temperature where the filler metal melts and flows into the joint, followed by cooling to achieve the desired material properties. Brazing can be performed in various environments, such as furnaces, vacuum chambers, or hydrogen atmospheres, depending on the materials and application requirements. This method is suitable for joining simple or complex designs and is often preferred for its ability to produce clean, high-strength joints without the need for fluxes in some cases.
Key Points Explained:
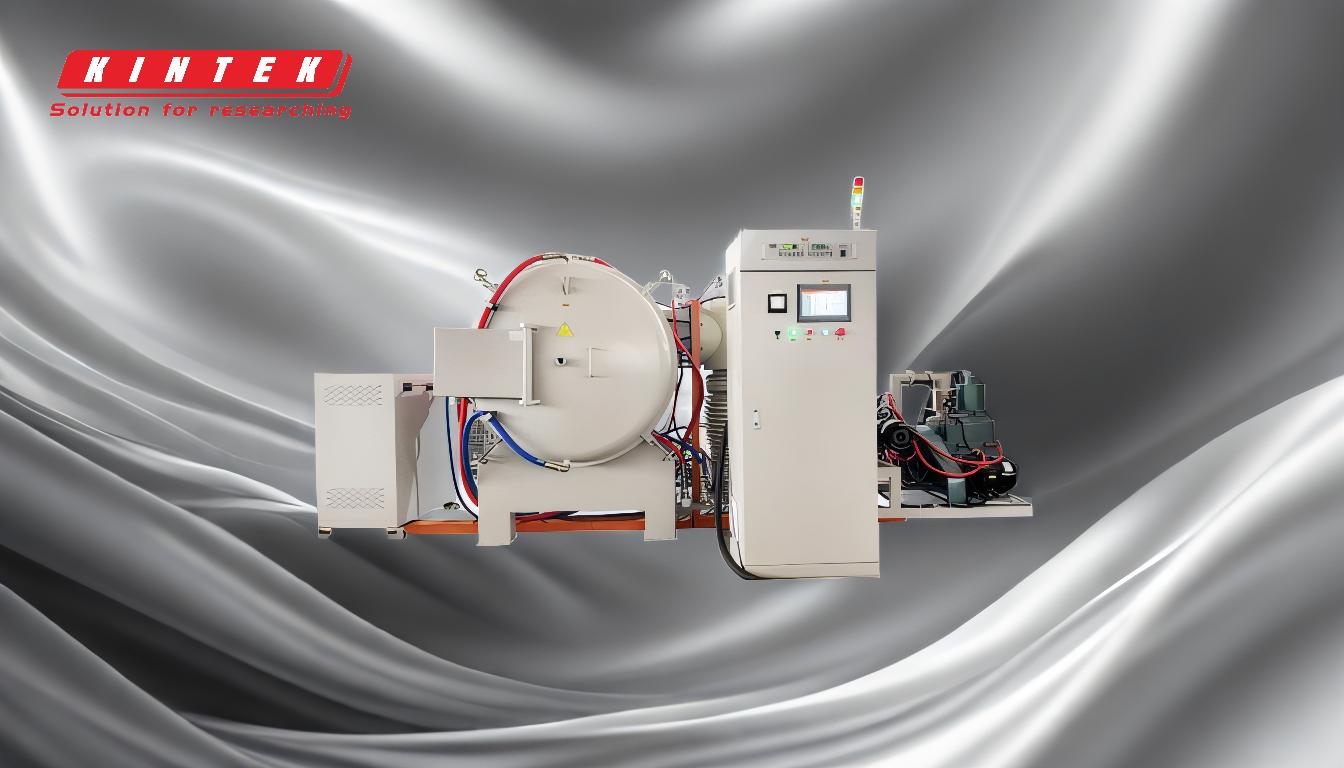
-
Definition and Purpose of Brazing:
- Brazing is a metal-joining process that uses a filler metal with a lower melting point than the base materials.
- The primary purpose is to create a strong, reliable, and repeatable metallurgical bond between components.
-
Types of Brazing Processes:
- Furnace Brazing: A semi-automated process where components are heated in a furnace to the brazing temperature. The filler metal flows into the joint, and the assembly is cooled or quenched to achieve desired properties.
- Vacuum Brazing: This method involves melting a filler metal in a vacuum furnace, eliminating the need for fluxes and reducing contamination. It is ideal for high-temperature applications and produces clean, high-strength joints.
- Hydrogen Brazing: Utilizes high-purity hydrogen to reduce surface oxides on the parent material, improving the flow of the braze alloy and resulting in high-integrity joints.
-
Steps in the Brazing Process:
- Preparation: Clean the parts to remove any contaminants that could affect the joint quality.
- Assembly and Filler Application: Apply the filler metal to the surfaces to be joined and assemble the components.
- Heating: Heat the assembly to the brazing temperature, ensuring the filler metal melts and flows into the joint.
- Cooling: Cool or quench the assembly to achieve the desired material properties.
-
Advantages of Brazing:
- Suitable for joining dissimilar metals and complex designs.
- Produces clean, high-strength joints without the need for fluxes in some cases.
- Repeatable and reliable process for industrial applications.
-
Applications of Brazing:
- Used in industries such as aerospace, automotive, and electronics for joining components in high-temperature or high-stress environments.
- Ideal for applications requiring clean, flux-free joints, such as in medical devices or vacuum systems.
-
Key Considerations:
- The choice of filler metal and brazing environment depends on the base materials and application requirements.
- Proper cleaning and preparation of components are critical to achieving high-quality joints.
- The brazing temperature must be carefully controlled to ensure the filler metal flows properly without damaging the base materials.
By understanding these key points, equipment and consumable purchasers can make informed decisions about selecting the appropriate brazing process and materials for their specific applications.
Summary Table:
Aspect | Details |
---|---|
Definition | Joining metals using a filler metal with a lower melting point. |
Purpose | Create strong, reliable, and repeatable metallurgical bonds. |
Types | Furnace brazing, vacuum brazing, hydrogen brazing. |
Steps | Preparation, assembly, heating, cooling. |
Advantages | Joins dissimilar metals, clean joints, repeatable process. |
Applications | Aerospace, automotive, electronics, medical devices, vacuum systems. |
Key Considerations | Filler metal choice, cleaning, temperature control. |
Need expert advice on brazing processes? Contact us today for tailored solutions!