The carburizing process is a heat treatment method used to increase the surface hardness and wear resistance of low-carbon steel while maintaining a ductile and tough core. This is achieved by diffusing carbon into the surface layer of the metal at high temperatures, typically below its melting point, in a carbon-rich environment. The process involves heating the steel in a furnace, exposing it to carbon-rich elements like propane gas, and allowing the carbon to diffuse into the surface. After carburizing, the steel is often quenched in oil to harden the surface, resulting in a hard outer layer and a softer, more malleable core. This method is widely used in industries requiring durable and wear-resistant components, such as automotive and machinery manufacturing.
Key Points Explained:
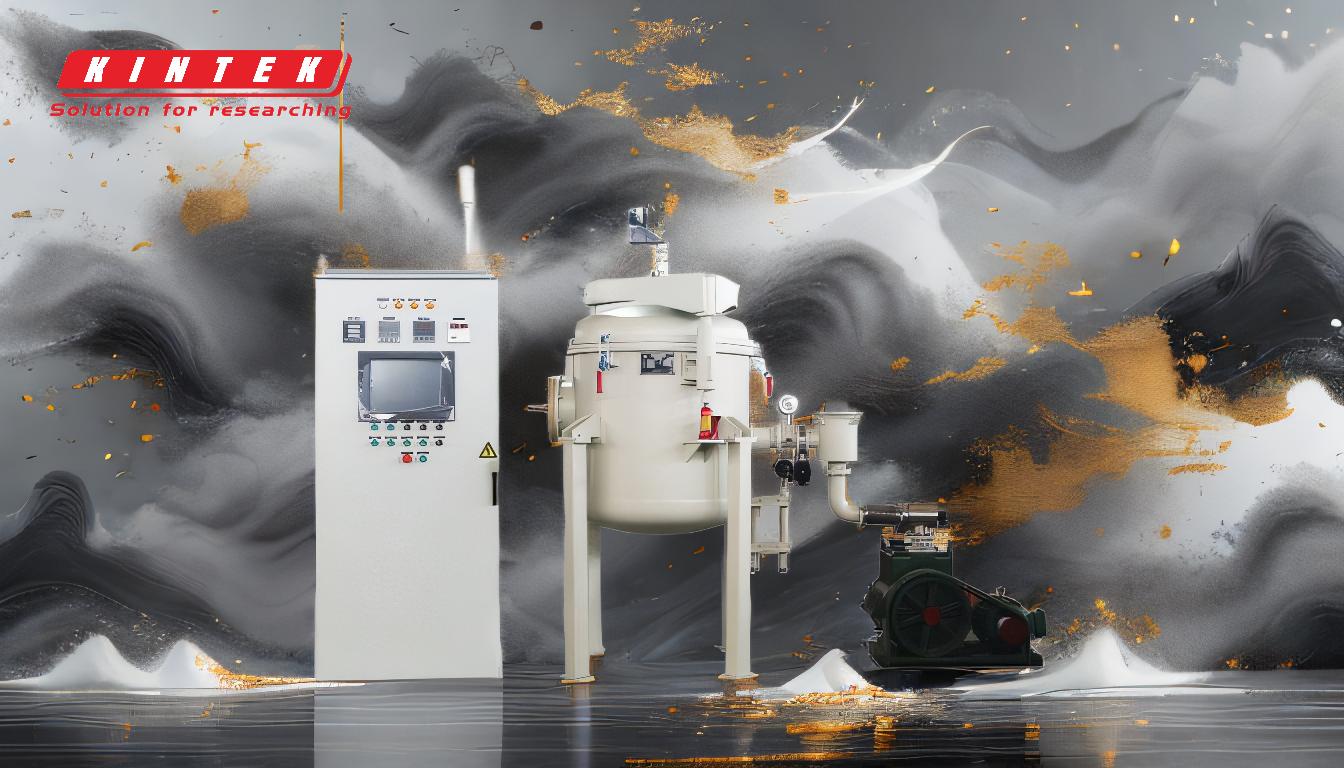
-
Purpose of Carburizing:
- Carburizing is primarily used to increase the surface hardness and wear resistance of low-carbon steel.
- It achieves this by enriching the surface layer with carbon, which enhances hardenability while maintaining the core's ductility and toughness.
- This dual property is essential for components that require both surface durability and internal strength, such as gears, shafts, and bearings.
-
Process Overview:
- The steel is heated in a furnace to a temperature below its melting point, typically between 850°C and 950°C.
- It is then exposed to a carbon-rich environment, such as propane gas, methane, or endothermic atmosphere.
- The carbon atoms diffuse into the steel's surface, creating a carbon-rich layer.
-
Steps in Carburizing:
- Step 1: Preparation: The steel part is cleaned and placed in a furnace.
- Step 2: Heating: The furnace is heated to the desired temperature, ensuring uniform heat distribution.
- Step 3: Carbon Introduction: A carbon-rich gas (e.g., propane) is introduced into the furnace.
- Step 4: Carbon Diffusion: The heat causes the gas to break down, releasing carbon atoms that diffuse into the steel's surface.
- Step 5: Quenching: After carburizing, the steel is rapidly cooled (quenched) in oil or another medium to harden the surface.
-
Types of Carburizing:
- Gas Carburizing: Uses carbon-rich gases like propane or methane in a controlled atmosphere furnace.
- Vacuum Carburizing: Conducted in a vacuum furnace to minimize oxidation and improve carbon diffusion.
- Liquid Carburizing: Involves immersing the steel in a carbon-rich liquid bath, such as molten salt.
- Pack Carburizing: The steel is packed in a carbon-rich material (e.g., charcoal) and heated in a sealed container.
-
Benefits of Carburizing:
- Surface Hardness: The carbon-enriched surface becomes highly resistant to wear and abrasion.
- Core Toughness: The core remains soft and ductile, providing impact resistance.
- Precision Control: Case depth (typically 0.020″ to 0.050″) and carbon concentration can be precisely controlled.
- Versatility: Suitable for a wide range of low-carbon steel alloys and complex geometries.
-
Applications of Carburized Steel:
- Automotive Industry: Used for gears, crankshafts, and camshafts to enhance durability.
- Machinery: Applied to components like bearings, rollers, and cutting tools for improved wear resistance.
- Aerospace: Utilized in parts requiring high strength-to-weight ratios and fatigue resistance.
-
Considerations for Equipment and Consumables:
- Furnace Selection: Choose furnaces with precise temperature control and uniform heat distribution.
- Carbon Sources: Use high-quality carbon-rich gases or materials to ensure consistent results.
- Quenching Medium: Select appropriate quenching oils or liquids based on the steel type and desired hardness.
- Masking Materials: Use carbon-stopping paints or coatings to protect areas that should not be carburized.
-
Advantages Over Other Heat Treatment Methods:
- Carburizing provides a deeper and more uniform case hardening compared to methods like flame hardening or induction hardening.
- It is cost-effective for large-scale production and suitable for complex parts.
By understanding the carburizing process, equipment purchasers can make informed decisions about the types of furnaces, gases, and consumables required to achieve optimal results for their specific applications.
Summary Table:
Aspect | Details |
---|---|
Purpose | Increases surface hardness and wear resistance while maintaining core toughness. |
Process Temperature | 850°C to 950°C, below the steel's melting point. |
Carbon Sources | Propane, methane, endothermic atmosphere, molten salt, or charcoal. |
Key Steps | Preparation, heating, carbon introduction, diffusion, and quenching. |
Types | Gas, vacuum, liquid, and pack carburizing. |
Benefits | Surface hardness, core toughness, precision control, and versatility. |
Applications | Automotive gears, machinery bearings, aerospace components. |
Ready to enhance your steel components with carburizing? Contact our experts today for tailored solutions!