Sintering is a process where atoms diffuse through a material's microstructure, driven by a gradient in chemical potential, to reduce porosity and enhance material properties such as strength, conductivity, and thermal performance. This diffusion occurs as atoms move from areas of higher chemical potential to lower chemical potential, leading to densification and bonding of particles. The process is influenced by various factors, including temperature, pressure, particle size, composition, and the sintering atmosphere. Optimal sintering conditions depend on the desired properties of the final product, with finer powders and higher temperatures generally improving compaction but requiring careful control of the liquid phase. Sintering is crucial for creating high-performance materials, especially those with high melting points, without the need for complete melting.
Key Points Explained:
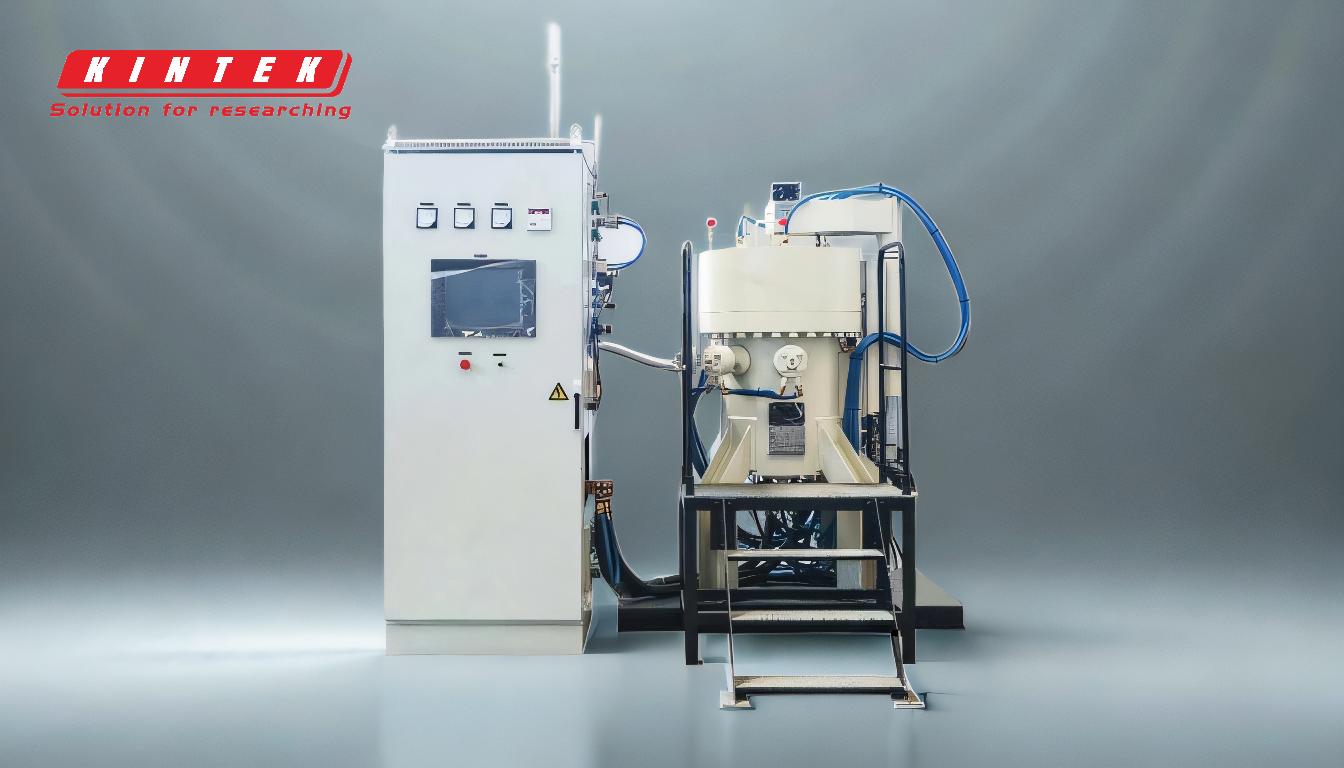
-
Atomic Diffusion and Chemical Potential Gradient:
- Sintering occurs due to the diffusion of atoms through the microstructure of a material.
- This diffusion is driven by a gradient in chemical potential, where atoms move from regions of higher chemical potential to regions of lower chemical potential.
- This movement leads to the bonding of particles and the reduction of porosity, resulting in a denser and stronger material.
-
Factors Influencing Sintering:
- Temperature: Higher temperatures increase the rate of atomic diffusion, enhancing sintering kinetics and improving material properties such as tensile strength and impact energy.
- Pressure: Applied pressure aids in particle rearrangement and the elimination of porosity, leading to better densification.
- Particle Size: Smaller particles have a higher surface area-to-volume ratio, which promotes faster diffusion and better densification.
- Composition: Homogeneous compositions facilitate uniform sintering, whereas heterogeneous compositions can lead to uneven densification.
- Atmosphere: The sintering atmosphere (e.g., air, vacuum, argon, or nitrogen) can affect the chemical reactions and the final properties of the material.
-
Sintering Process Parameters:
- Sintering Temperature and Time: These depend on the material and the desired density of the final product. Higher temperatures generally lead to better densification but must be carefully controlled to avoid excessive grain growth or melting.
- Heating Rate: A controlled heating rate is crucial to ensure uniform densification and avoid defects.
- Layer Thickness and Machine Speed: In industrial sintering, parameters like layer thickness (typically 250-500mm) and machine speed (1.5-4m/min) are controlled to ensure the material is sintered uniformly and reaches the desired endpoint.
-
Benefits of Sintering:
- Strength and Integrity: Sintering imparts mechanical strength and structural integrity to materials.
- Reduced Porosity: The process significantly reduces porosity, enhancing properties like electrical conductivity, thermal conductivity, and translucency.
- High-Melting-Point Materials: Sintering allows the creation of products from metals and ceramics with high melting points without the need for complete melting.
-
Techniques and Equipment:
- Different sintering techniques (e.g., pressure-assisted sintering, spark plasma sintering) are used depending on the material and desired properties.
- Sintering is typically carried out in controlled environments using equipment such as belt conveyors, push furnaces, or batch furnaces.
-
Industrial Considerations:
- Air Volume and Vacuum: In industrial sintering, factors like air volume (e.g., 3200m³ per ton of sintering ore) and vacuum levels are controlled to optimize the process.
- Sintering Endpoint: The process is carefully monitored to ensure the material reaches the desired sintering endpoint, which is critical for achieving the required properties.
In summary, sintering is a complex process influenced by multiple factors, each of which must be carefully controlled to achieve the desired material properties. Understanding these factors and their interactions is essential for optimizing the sintering process and producing high-quality materials.
Summary Table:
Key Aspect | Description |
---|---|
Atomic Diffusion | Driven by chemical potential gradients, leading to particle bonding and densification. |
Influencing Factors | Temperature, pressure, particle size, composition, and sintering atmosphere. |
Process Parameters | Sintering temperature, time, heating rate, layer thickness, and machine speed. |
Benefits | Enhanced strength, reduced porosity, and creation of high-melting-point materials. |
Techniques & Equipment | Pressure-assisted sintering, spark plasma sintering, belt conveyors, and furnaces. |
Industrial Considerations | Air volume, vacuum levels, and sintering endpoint monitoring. |
Optimize your material properties with expert sintering solutions—contact us today to learn more!