Heat treatment is a critical process in metal production that involves controlled heating and cooling to alter the physical and mechanical properties of materials. The cooling process, in particular, plays a pivotal role in determining the final characteristics of the metal, such as hardness, strength, and ductility. Cooling can be achieved through various methods, including air cooling, oil quenching, water quenching, and controlled furnace cooling, each tailored to achieve specific material properties. Understanding the cooling process is essential for optimizing heat treatment outcomes, ensuring the metal meets the desired performance standards for applications in industries like aerospace, automotive, and manufacturing.
Key Points Explained:
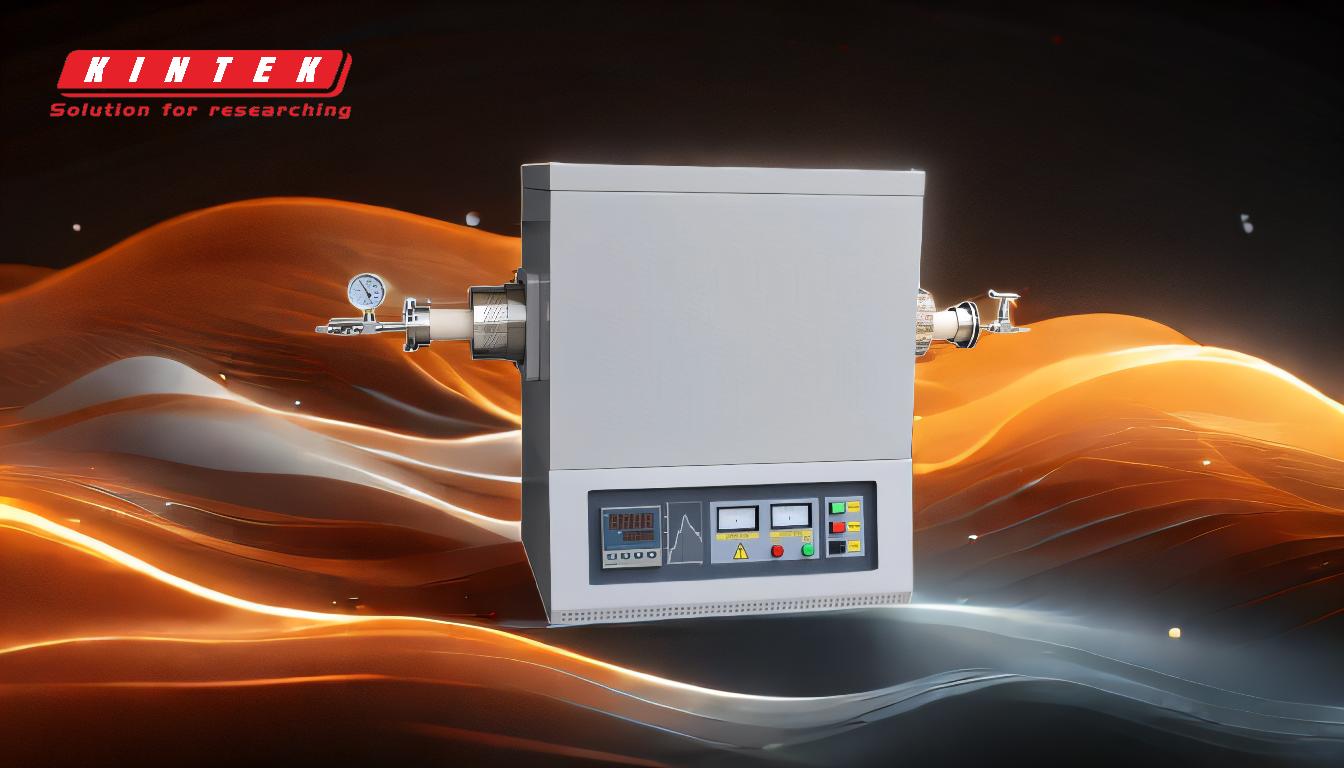
-
Purpose of Cooling in Heat Treatment:
- The cooling process is integral to heat treatment as it determines the microstructure and properties of the metal. Rapid cooling, such as quenching, can harden the metal by transforming its structure into martensite, while slower cooling methods, like air cooling, allow for the formation of softer structures like pearlite or bainite. The choice of cooling method depends on the desired balance between hardness, strength, and ductility.
-
Common Cooling Methods:
- Air Cooling: This is a relatively slow cooling process where the heated metal is allowed to cool naturally in ambient air. It is often used for materials that require moderate strength and ductility, such as low-carbon steels.
- Oil Quenching: Oil is used as a quenching medium to cool the metal at a controlled rate. It is less severe than water quenching, reducing the risk of cracking or distortion, and is commonly used for alloy steels.
- Water Quenching: Water provides rapid cooling, making it suitable for achieving high hardness in materials like carbon steels. However, it can introduce internal stresses and increase the risk of cracking.
- Furnace Cooling: In this method, the metal is cooled slowly inside a furnace. It is typically used for annealing processes to produce a soft and ductile material.
-
Factors Influencing Cooling Rate:
- Material Composition: The alloying elements in the metal influence its hardenability, which determines how quickly it can be cooled without cracking.
- Quenchant Properties: The type of quenching medium (water, oil, or polymer) and its temperature affect the cooling rate and the final properties of the metal.
- Part Geometry: Thicker sections cool more slowly than thinner ones, which can lead to variations in hardness and microstructure across the part.
-
Applications of Cooling Processes:
- Aerospace and Automotive Industries: Components like gears, shafts, and engine parts often undergo heat treatment with precise cooling to achieve high strength and wear resistance.
- Tool Manufacturing: Cutting tools and dies require high hardness and toughness, which are achieved through controlled quenching processes.
- Batch Metal Production: Heat treatment with tailored cooling is used to produce consistent and reliable metal parts for industrial applications.
-
Challenges and Considerations:
- Cracking and Distortion: Rapid cooling can cause thermal stresses, leading to cracking or warping of the metal. Proper selection of quenching medium and process parameters is essential to mitigate these risks.
- Uniformity of Cooling: Ensuring even cooling across the entire part is crucial to avoid variations in material properties.
- Environmental and Safety Concerns: Quenching mediums like oil and water require proper handling and disposal to minimize environmental impact and ensure workplace safety.
By carefully selecting and controlling the cooling process, manufacturers can achieve the desired material properties for specific applications, ensuring the reliability and performance of heat-treated components.
Summary Table:
Aspect | Details |
---|---|
Purpose of Cooling | Determines microstructure, hardness, strength, and ductility of metals. |
Common Methods | Air cooling, oil quenching, water quenching, furnace cooling. |
Influencing Factors | Material composition, quenchant properties, part geometry. |
Applications | Aerospace, automotive, tool manufacturing, batch metal production. |
Challenges | Cracking, distortion, uniformity of cooling, environmental safety concerns. |
Discover the best cooling process for your heat treatment needs—contact our experts today!