Heat treatment processes such as annealing, tempering, and quenching are essential in altering the physical and mechanical properties of metals. Annealing involves heating the metal to a specific temperature and then slowly cooling it to soften the material, improve ductility, and relieve internal stresses. Tempering, on the other hand, follows quenching and involves reheating the metal to a lower temperature to reduce brittleness and increase toughness. Quenching rapidly cools the metal after heating to achieve high hardness and strength, often at the expense of ductility. Each process serves distinct purposes and is chosen based on the desired outcome for the metal's properties.
Key Points Explained:
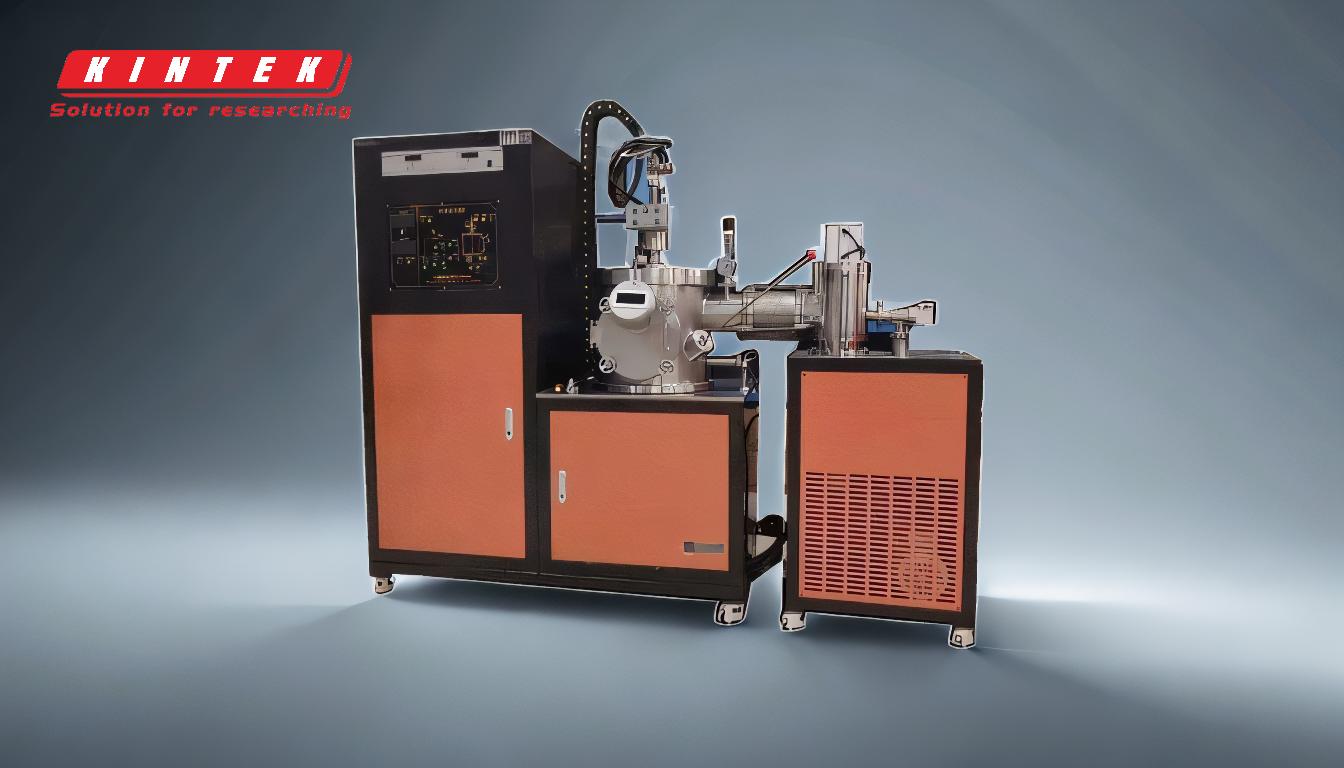
-
Annealing:
- Purpose: Annealing is primarily used to soften metals, improve ductility, and relieve internal stresses. This process makes the metal more workable and less prone to cracking during subsequent manufacturing processes.
- Process: The metal is heated to a specific temperature (above its recrystallization temperature) and then slowly cooled, often in a furnace. This slow cooling allows the metal's microstructure to reform into a more stable and less stressed state.
- Applications: Annealing is commonly used in the production of steel, copper, and aluminum products where improved machinability and formability are required.
-
Tempering:
- Purpose: Tempering is used to reduce the brittleness of metals that have been hardened through quenching. It increases toughness and ductility while maintaining a significant level of hardness.
- Process: After quenching, the metal is reheated to a temperature below its critical point and then cooled. The temperature and duration of tempering are carefully controlled to achieve the desired balance between hardness and toughness.
- Applications: Tempering is often applied to tools, blades, and structural components that require a combination of hardness and resistance to impact.
-
Quenching:
- Purpose: Quenching is used to rapidly cool metals to achieve high hardness and strength. This process is essential for creating materials that can withstand high stress and wear.
- Process: The metal is heated to a high temperature and then rapidly cooled, usually by immersing it in a quenching medium such as water, oil, or air. This rapid cooling locks the metal's microstructure in a hardened state.
- Applications: Quenching is commonly used in the production of gears, shafts, and other components that require high surface hardness and wear resistance.
-
Comparison of Processes:
- Temperature and Cooling Rate: Annealing involves slow cooling, tempering involves reheating and controlled cooling, and quenching involves rapid cooling.
- Microstructural Changes: Annealing results in a softer, more ductile microstructure. Tempering modifies the hardened microstructure to reduce brittleness. Quenching creates a hard, brittle microstructure that is then tempered to improve toughness.
- End Properties: Annealing improves machinability and formability, tempering balances hardness and toughness, and quenching maximizes hardness and strength.
-
Selection of Process:
- The choice between annealing, tempering, and quenching depends on the desired properties of the final product. For example, a component that requires high wear resistance might undergo quenching followed by tempering, while a component that needs to be easily machined might be annealed.
Understanding these processes and their effects on metal properties is crucial for selecting the appropriate heat treatment method to achieve the desired performance characteristics in metal components.
Summary Table:
Process | Purpose | Key Steps | Applications |
---|---|---|---|
Annealing | Softens metal, improves ductility, relieves internal stresses | Heat to specific temperature, slow cooling | Steel, copper, aluminum products requiring machinability and formability |
Tempering | Reduces brittleness, increases toughness while maintaining hardness | Reheat quenched metal to a lower temperature, controlled cooling | Tools, blades, structural components needing hardness and impact resistance |
Quenching | Achieves high hardness and strength at the expense of ductility | Heat to high temperature, rapid cooling in water, oil, or air | Gears, shafts, components requiring high surface hardness and wear resistance |
Need help choosing the right heat treatment process for your metal components? Contact our experts today!