Balanced and unbalanced magnetron sputtering are two configurations of magnetron sputtering systems, a widely used physical vapor deposition (PVD) technique for thin film coating. The primary difference lies in the arrangement and strength of the magnetic fields, which influence plasma confinement, electron behavior, and ion current density. Balanced magnetrons confine the plasma close to the target, while unbalanced magnetrons allow some electrons to escape towards the substrate, enhancing ionization and improving thin film quality. This distinction makes unbalanced magnetrons more suitable for applications requiring high-quality coatings with better adhesion and uniformity.
Key Points Explained:
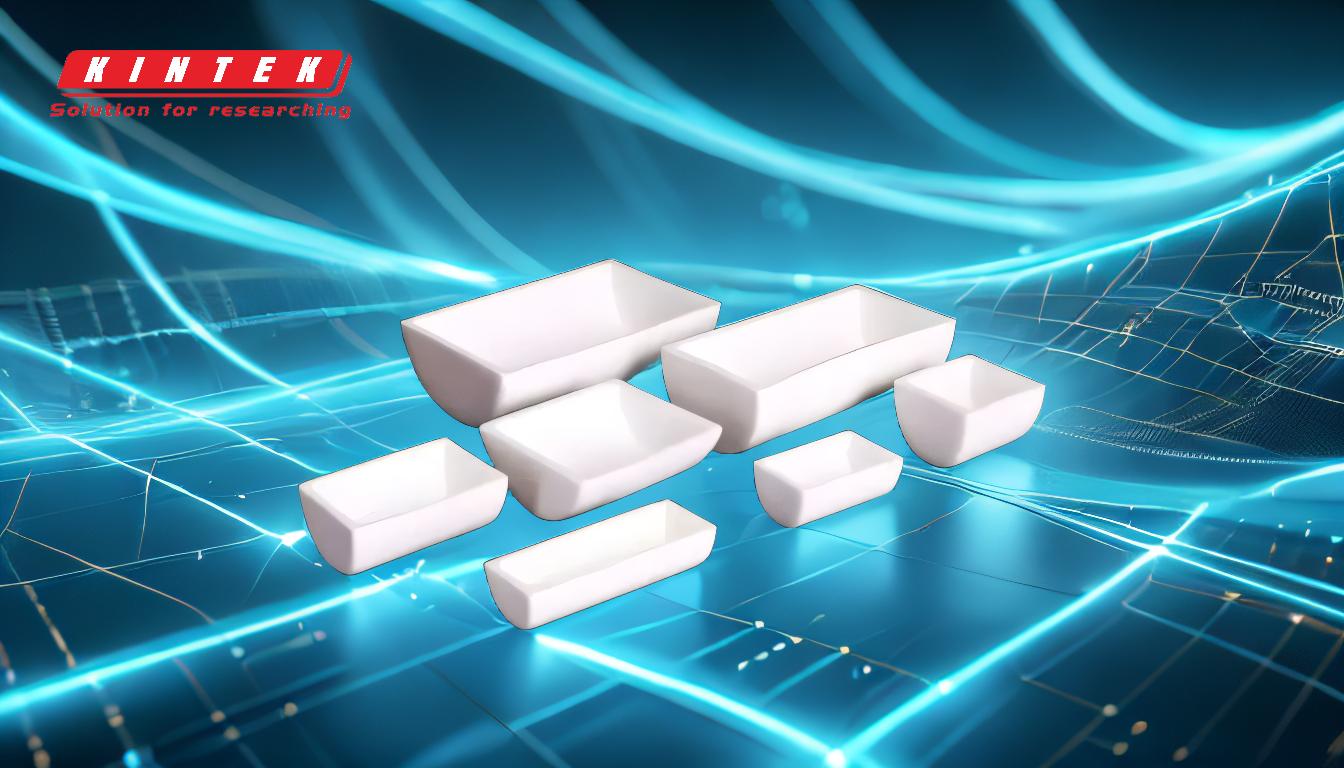
-
Magnetic Field Configuration:
- In balanced magnetron sputtering, the magnetic field lines are closed and symmetric, with all magnets having the same strength. This configuration traps electrons near the cathode (target) region, confining the plasma to a small area.
- In unbalanced magnetron sputtering, the central magnet is weaker than the outer ring magnets, creating an asymmetric magnetic field. This allows some magnetic field lines to extend toward the substrate, enabling electrons to escape from the target region and reach the substrate.
-
Plasma Confinement and Electron Behavior:
- Balanced magnetrons tightly confine the plasma to the target area, which limits the ionization of sputtered atoms and reduces the ion current density at the substrate.
- Unbalanced magnetrons allow electrons to escape toward the substrate, increasing ionization in the substrate region. This results in a higher ion current density, which enhances the energy and mobility of sputtered atoms, leading to better film adhesion and quality.
-
Thin Film Quality and Deposition Rate:
- Balanced magnetrons are typically used for applications where high deposition rates are required, but the film quality may be lower due to limited ionization near the substrate.
- Unbalanced magnetrons improve thin film quality by increasing ionization and ion bombardment of the growing film. This results in denser, more uniform coatings with better mechanical and optical properties.
-
Modification Techniques:
- Balanced magnetrons can be modified into unbalanced magnetrons using techniques such as adjusting magnet strengths or using toroidal-shaped magnets. This modification significantly increases the deposition rate and improves coating quality.
- For multiple targets, a technique called closed-field unbalanced magnetron sputtering is used. This method creates a closed magnetic field loop between targets, further enhancing ionization and deposition uniformity.
-
Applications:
- Balanced magnetrons are suitable for applications requiring high deposition rates but less stringent film quality, such as decorative coatings or simple protective layers.
- Unbalanced magnetrons are preferred for advanced applications requiring high-quality films, such as optical coatings, wear-resistant coatings, and semiconductor devices.
By understanding these differences, equipment and consumable purchasers can select the appropriate magnetron sputtering system based on their specific coating requirements, balancing factors like deposition rate, film quality, and cost.
Summary Table:
Feature | Balanced Magnetron | Unbalanced Magnetron |
---|---|---|
Magnetic Field | Symmetric, closed field lines | Asymmetric, extends toward substrate |
Plasma Confinement | Tightly confined to target area | Electrons escape toward substrate |
Ion Current Density | Lower at substrate | Higher at substrate |
Film Quality | Lower due to limited ionization | Higher due to increased ionization and ion bombardment |
Deposition Rate | High | Moderate to high |
Applications | Decorative coatings, simple protective layers | Optical coatings, wear-resistant coatings, semiconductor devices |
Need help choosing the right magnetron sputtering system? Contact our experts today for tailored solutions!