CVD (Chemical Vapor Deposition) and PVD (Physical Vapor Deposition) are two widely used coating techniques for cutting tools, each with distinct characteristics and applications. While both methods aim to enhance tool performance by depositing a thin, durable layer onto the substrate, they differ significantly in their processes, coating properties, and suitability for specific machining tasks. PVD involves vaporizing a solid material and depositing it onto the substrate, resulting in thinner, smoother coatings with sharper edges, ideal for precision finishing operations. CVD, on the other hand, uses gaseous precursors that chemically react to form a thicker, rougher coating, providing superior thermal barrier properties and wear resistance, making it better suited for roughing and continuous cutting operations. Understanding these differences is crucial for selecting the right coating method based on the machining requirements and material being processed.
Key Points Explained:
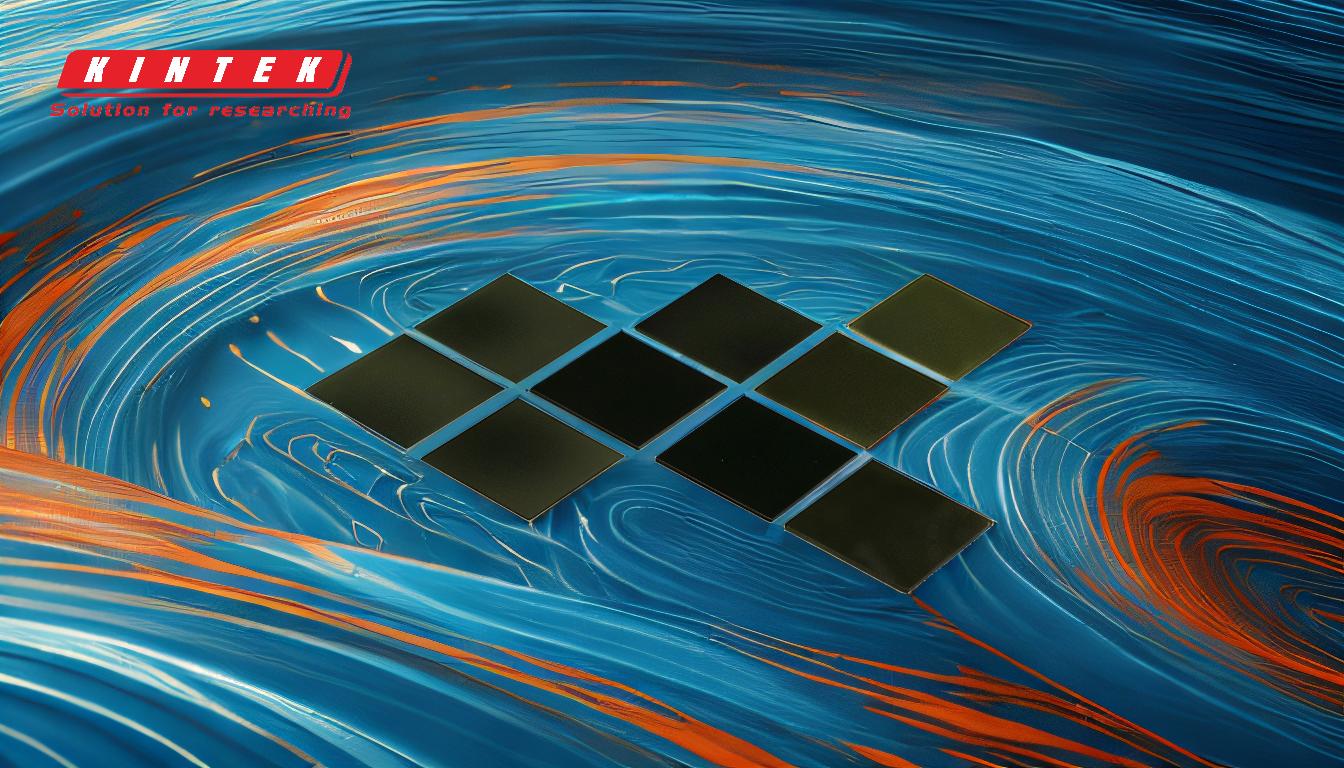
-
Process Differences:
-
PVD:
- Involves vaporizing a solid material (target) using physical methods like arc discharge or sputtering.
- The vaporized atoms condense onto the substrate, forming a thin, smooth coating.
- Operates at relatively low temperatures (250°C to 450°C), making it suitable for heat-sensitive materials.
-
CVD:
- Uses gaseous precursors that chemically react at high temperatures (450°C to 1050°C) to deposit a solid coating.
- The chemical reactions produce a thicker and rougher coating compared to PVD.
- Requires higher temperatures, which can limit its use with heat-sensitive substrates.
-
PVD:
-
Coating Properties:
-
PVD:
- Produces thin coatings (3~5μm) with a smooth surface, resulting in sharper cutting edges.
- Forms compressive stress during cooling, enhancing durability and resistance to cracking.
- Ideal for interrupted cutting processes like milling, where tool edges experience frequent impacts.
-
CVD:
- Generates thicker coatings (10~20μm) with a rougher surface, providing better thermal insulation and wear resistance.
- Suitable for continuous cutting operations like turning, where tools face consistent heat and friction.
-
PVD:
-
Applications in Machining:
-
PVD:
- Best suited for finishing operations that require precision and sharp edges, such as milling, drilling, and threading.
- Commonly used for machining materials like stainless steel, titanium, and heat-treated alloys.
-
CVD:
- More effective for roughing and heavy-duty cutting tasks, such as turning and boring.
- Preferred for machining materials like cast iron, carbon steel, and high-temperature alloys.
-
PVD:
-
Environmental and Operational Considerations:
-
PVD:
- Environmentally friendly, as it does not involve chemical reactions or produce harmful byproducts.
- Lower processing temperatures reduce energy consumption and minimize substrate distortion.
-
CVD:
- Involves chemical reactions that can produce pollutants, requiring proper waste management.
- Higher temperatures may lead to substrate deformation, limiting its use with certain materials.
-
PVD:
-
Advantages and Limitations:
-
PVD:
- Advantages: Thin, sharp coatings; lower processing temperatures; environmentally friendly.
- Limitations: Limited coating thickness; less effective as a thermal barrier.
-
CVD:
- Advantages: Thicker, more durable coatings; superior thermal and wear resistance.
- Limitations: Higher processing temperatures; potential environmental impact.
-
PVD:
By understanding these key differences, purchasers and engineers can make informed decisions about whether to use PVD or CVD-coated cutting tools based on the specific machining requirements, material properties, and desired outcomes.
Summary Table:
Aspect | PVD | CVD |
---|---|---|
Process | Vaporizes solid material, low temperature (250°C–450°C) | Uses gaseous precursors, high temperature (450°C–1050°C) |
Coating Thickness | Thin (3~5μm), smooth surface | Thick (10~20μm), rough surface |
Coating Properties | Sharp edges, compressive stress, durable | Superior thermal barrier, wear-resistant |
Applications | Finishing operations (milling, drilling, threading) | Roughing and heavy-duty cutting (turning, boring) |
Materials | Stainless steel, titanium, heat-treated alloys | Cast iron, carbon steel, high-temperature alloys |
Environmental Impact | Environmentally friendly, no harmful byproducts | Potential pollutants, requires waste management |
Advantages | Sharp coatings, low processing temperatures, eco-friendly | Durable coatings, superior thermal and wear resistance |
Limitations | Limited thickness, less effective as a thermal barrier | High processing temperatures, potential substrate deformation |
Need help choosing the right coating for your cutting tools? Contact our experts today!